It has been 10 months since Container Centralen (CC), a Danish firm that owns and maintains trolleys used by the horticulture industry, went live with its RFID deployment, which involved installing passive EPC Gen 2 RFID tags onto 3.84 million trolleys used by its European clientele, as well as the accompanying infrastructure of RFID readers at 60 CC depots and four repair shops.
Speaking on Wednesday at the RFID Journal LIVE! Europe 2011 conference and exhibition, held in Amsterdam, Soren Moller Sorensen, CC’s chief operating officer, explained that although his company experienced some initial resistance from customers with regard to the tagging project, many are now expressing strong curiosity about radio frequency identification, and, in some recent cases, interest in instituting new RFID-enabled applications involving the trolleys.
“Customers are not talking negative about RFID anymore,” Sorensen stated. “It’s much more constructive now. Horticulture companies are asking what they can do with RFID, and which readers they should buy.”
Container Centralen’s customers had expressed worry that tracking trolleys via RFID might cause confidential company information to be accessible by competitors, Sorensen explained, or somehow infringe on their privacy.
CC began using the tags on Jan. 10, 2011, after several project delays due to customer hesitation. “We were ready, but the customers needed more time to learn about RFID and prepare for the RFID project,” Sorensen noted while on the sidelines of the conference.
Attaching an RFID tag to the base of each one of its 3.84 million trolleys—which contain shelves and are used to transport, store and display plants—took only about two and a half months, Sorensen said, because CC asked its customers to perform the tagging themselves, using specially designed tags manufactured by Confidex. Though CC’s property, the trolleys are used on the premises of 200,000 of its customers, comprising growers, wholesalers, exporters, consolidators, transport companies and retailers—many of them small businesses.
The project was initially slated for completion in February 2010 (see Container Centralen Says It’s Ready to Roll Out RFID in Europe), but CC’s customers claimed they required additional time to understand what was being asked of them for the tagging project, dubbed “Operation Chip It,” as well as what the possibilities were with regard to RFID. Container Centralen tried again, setting a mandatory deadline of October 2010 for completing the tagging—but that deadline was also abandoned as CC continued to educate members of the horticulture supply chain regarding the technology’s benefits.
The extensive information campaign about the RFID project actually began several years prior to the January 2011 kickoff for using tagged trolleys. The campaign intensified in fall 2010, leading up to the launch date, with information regularly sent to all 200,000 customers and partners.
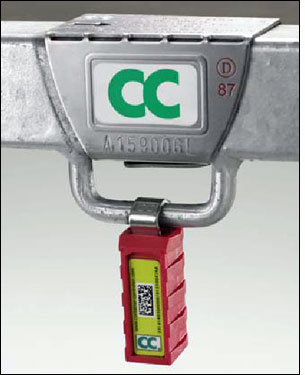
According to Sorensen, some customers balked upon learning that in order to ensure that they did not accept any counterfeit trolleys, they had to use an RFID reader that would cost a minimum of €400 ($551). “People would say, ‘I can get a cell phone for €1—why should I buy an RFID reader for €400?'” Sorensen said.
Although the reader was a one-off cost—whereas with phones, users pay a monthly fee—it was a challenge in people’s minds, Sorensen explained. “Now, this attitude no longer prevails,” he said. “Customers and the project have matured, and are getting used to the technology now.”
Sorensen estimated that Container Centralen’s customers have purchased almost 5,000 interrogators to date, in order to improve their own internal handling of the tagged trolleys.
The tagging was primarily designed to ensure each trolley’s authenticity. Counterfeit trolleys were frequently put into the pool and not maintained, Sorensen noted. If a wheel falls off while a trolley is loaded with plants, he said, not only are the plants lost, but a large mess must then be cleaned up.
Container Centralen has purchased roughly 250 Nordic ID PL 3000 handheld readers for its own use. The company is utilizing the devices to identify each trolley moved into its facilities, and is using the RFID technology to automate the paperwork necessary when shipments are transported between its depots. CC, Sorensen reported, has achieved a “substantial” cost savings with improved logistics efficiency and depot administration, though he declined to provide a specific amount.
This fall, Dutch horticulture products supplier BAAS Plantenservice announced that it was rolling out an application based on the information it collects from the RFID-tagged CC containers. Thanks to an application developed by Mieloo & Alexander—an RFID integrator that served as a technology supplier to some of the partners on the project—BAAS Plantenservice has increased visibility regarding plant shipments. BAAS’ suppliers now apply a bar-coded label containing the BAAS order number to each trolley. That information is linked to the CC tag number, and is then forwarded to BAAS and its transport companies, in order to improve inbound logistics. Drivers employ a Nordic ID handheld to read the CC tags so that BAAS Plantenservice can know when goods will arrive. BAAS processes up to 14,000 CC trolleys daily during peak times. Sorensen believes that the application may be the first large follow-on application based on CC’s RFID-tagged trolleys.
“Our tags made the application possible,” Sorensen said. “We’re very happy that companies can use the RFID tag for identification on the load carrier and integrating the data. It’s a breakthrough—not for CC, but for the whole horticulture business.”
Now that its RFID implementation is complete, Sorensen said, Container Centralen is considering its next steps toward improving the trolleys—perhaps by introducing plastic shelves. Some ideas are being tested on a small scale, he added, though it would be a huge investment if all shelves (currently made of steel and plywood) were to be replaced with plastic. Tagging each individual shelf of every trolley could be another option, but such a project would also take place only after close consideration, and after talks were held with the largest industry stakeholders.
If the shelves were tagged, CC’s customers using the trolleys could link product, sales and order data together with information about a particular trolley’s physical location. Many plant orders are loaded onto a shelf based on what can fit. It would be of value to know how they are packed and distributed, Sorensen indicated.