Conair, a U.S. manufacturer and marketer of health and beauty products and kitchen appliances, is taking another step toward using radio frequency identification to track every item it sells, from factory to store. The company’s RFID-focused subsidiary, United Security Applications ID (USA ID), is developing an RFID interrogator that will be utilized in Conair’s Costa Rica and Chinese factories to encode tags applied to products as they are manufactured and prepared for shipping. Once the devices are put in place—which is slated to occur in the first half of 2010—USA ID expects Conair to tag all of the products it manufactures, says Paul Arguin, Conair/USA ID’s director of technology and engineering.
The deployment is part of the company’s two-pronged effort to employ RFID technology to improve supply chain visibility for itself, as well as for customs authorities and the U.S. Department of Homeland Security (DHS). Conair—one of the 50 largest importers to the United States—has also developed RFID-based container seals, which it is attaching to some containers it uses to ship its products to the United States. The seals enable Conair, logistics companies, customs officials and the DHS to confirm what is in a container, ensure it has not been tampered with and enable Conair to locate that container and its contents. According to Arguin, a new version of the seal—a bolt containing a passive UHF EPC Gen 2 RFID tag, designed to be inexpensive and look like non-RFID container bolts already on the market—will be in use for international shipping once it receives its ISO/PAS 17712 certification (a safety standard required for mechanical seals), which is expected to happen this month).
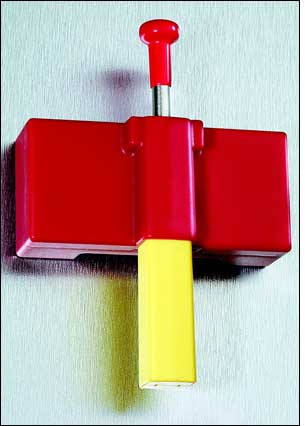
In 2002, Conair first began tagging products destined for Wal-Mart to comply with that retailer’s RFID policy. It formed USA ID to develop RFID solutions that would not only provide valuable data to Wal-Mart regarding the products’ whereabouts, but also offer Conair visibility into its supply chain. USA ID also began working with the DHS in 2002 to improve the security of shipments arriving in the United States from other countries. In this effort, USA ID developed an RFID-enabled container seal with an EPC Gen 2 passive UHF tag that could ensure a container had not been opened, and provide an electronic manifest that could be accessed by customs or the DHS as the container passed through U.S. ports. Since USA ID began developing its EPC Gen 2 container seal, several other companies—such as Secura Shield—have developed their own versions as well.
This year, Conair launched a pilot program whereby it tested whether RFID technology could improve out-of-stocks. The company tagged products at the item level as they were shipped to Sam’s Club‘s distribution centers (DCs) and stores throughout the country. Conair attached EPC Gen 2 RFID tags manufactured by USA ID to the packaging of Cuisinart and Waring products, as well as other high-end personal-care items. An RFID tag was applied to each item and read as it left Conair’s warehouse in South Haven, Miss., then was read again at Sam’s Club’s DCs and stores. Software designed by USA ID then uploaded information derived from RFID interrogators located at the DCs and stores, thereby enabling Conair to receive updates regarding those items’ locations. With that data, Conair was better able to reduce out-of-stocks and ensure stores had sufficient product, thereby increasing sales.
“We saw a significant increase,” Arguin says. “It raised eyebrows for everybody, not just Conair,” but also Sam’s Club. “We believe that the increased sales were directly related to both Conair and our customer [Sam’s Club] having visibility of out-of-stocks.” Because low-inventory alerts could be sent based on data from the tag reads as they were received at stores, along with point-of-sale data indicating sales of products, the reordering of products occurred more quickly than it had with the manual system, he says. “We believe that overlooking out-of-stock conditions is eliminated. You can’t sell what isn’t on the shelf.”
Based on the success of its Sam’s Club pilot, Conair’s South Haven warehouse began tagging master cartons—which carry four to six hair driers apiece—destined for Wal-Mart stores. Each tag will be encoded with a unique ID number linked to data about the corresponding carton and the products contained within. The tagging process commenced in September, for products that will be shipped in November.
Conair is tagging only the master cartons, but not the packaging of individual items within, in order to reduce the labor that would otherwise be expended by Conair’s staff. The hair driers arriving at Conair’s DC, for example, are already boxed in the master cartons by the appliances’ manufacturer in Costa Rica or China, and tagging the items individually would require opening the cartons and, in some cases, removing the products to apply labels. When Conair shipped tagged items to Sam’s Club, workers at Conair’s South Haven warehouse did, in fact, open each carton and apply tags to the tops of all item boxes contained within (removing the items to apply tags was unnecessary in that case).
Conair’s goal is to have the products tagged by the manufacturers, Arguin says, thus reducing the step of applying tags at the South Haven warehouse. In this effort, USA ID’s new encoder is being developed in partnership with Adasa, which currently produces mobile RFID interrogators that will be modified for Conair’s purposes. Conair and Adasa are jointly developing the new model, which is on wheels and will be designed so it can be rolled to the area where an encoding workstation is needed, and then be put to use with minimal effort by employees at the manufacturing facilities.
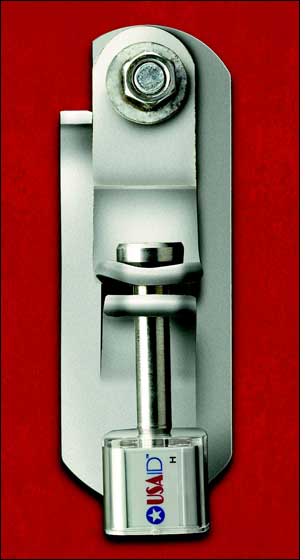
The new encoder is designed to be more portable than similar interrogators on the market. It will be battery-operated, inexpensive and work with a wireless, wired or Bluetooth connection, and it will also come with a touch-screen display and accommodate a reel of labels up to 2 feet in diameter.
“Both Adasa and Conair/USA ID believe this device, in combination with our labels, will revolutionize the industry,” Arguin states, “by reducing the cost of implementing item-level labeling and make this goal within reach of everyone.”
The cart will enable Conair’s third-party manufacturers to encode tags with an EPC number and then attach tags by first scanning the bar-coded UPC product number, which triggers the device to encode an RFID label and peel it from the backing. The label can then be applied to the product boxes as the items come off the assembly line, either manually or by machine. In so doing, the products will come to Conair’s U.S. warehouses already tagged at the item level. The encoder is being manufactured in Costa Rica, and is slated to be tested for label encoding at Conair’s manufacturing facility in that country, in the first quarter of 2010.
For container tagging, USA ID first developed a container seal with a built-in UHF Gen 2 96-bit RFID tag with a unique ID number that links to an electronic manifest on USA ID’s server. The seal consists of a 4-inch-long steel bolt that is inserted into a container’s door hasp. To seal the door, the bolt locks onto an RFID-enabled body. Once the bolt is married to that body, a fixed or handheld RFID interrogator can be used to read the seal’s tag ID number at the point of origin, or at distribution centers as the containers are transported. An external GPS receiver can be integrated in the seal’s body.
Alternatively, an internal GPS receiver can be placed inside the container with the cargo, to track its location without being seen, for security purposes. Whether internal or external, the GPS receiver transmits the container’s location via a GPRS or SMS connection. A handheld RFID interrogator can then transmit the tag’s unique ID number—via Wi-Fi or GPRS, or plugged into a PC with an Ethernet cable—to USA ID’s server, where the information is stored and displayed for authorized users. GPS data from the same container is linked to that ID number on the server.
Since launching the first version of its RFID-enabled container seal, Conair has developed a shorter model that more closely resembles other container seals in use—a feature requested in the Hong Kong port at which Conair piloted the technology. The company applies the seals to containers as they move domestically, either by truck or rail. The second-generation seal, consisting of a bolt less than 3 inches in length that locks onto a body approximately 1 inch in width, length and height, has an EPC Gen 2 RFID tag with 512 bits of user memory. This seal is less expensive than the first-generation version, Arguin says—approximately the same cost as a non-RFID bolt seal. The first generation has a range of approximately 30 feet, while the new, shorter version—now awaiting ISO approval—has a range of 10 to 15 feet. Once the new container bolt is approved, Conair intends to use it for international transport of goods coming from manufacturers.
With the new version, like its predecessor, customs agents equipped with RFID readers could scan the container seal to obtain its electronic manifest. With the second-generation seal, the tag’s 512-bit user memory is large enough to store the manifest, thereby facilitating the container-inspection process. As long as the seal does not send a signal indicating it has been damaged or broken, a customs agent would know that container has not been opened, and that its contents have thus not been altered.
Although the DHS and logistics companies have shown an interest in the technology, they have not yet adopted it, in part because they have not acquired the hardware—handheld interrogators—required to read the tags. “We did a demonstration with customs last summer, and they were very enthusiastic,” says John Mayorek, Conair’s senior VP.
USA ID is currently in the process of marketing and selling the RFID technology Conair is using to other companies. “This is right on the verge of busting loose,” Mayorek notes, with product manufacturers and retailers looking at the labeling solution, and ocean carriers and trucking companies showing an interest in the GPS-enabled container seal. “My own personal observation is that these products [RFID labels and container seals] are definitely needed.” Conair currently employs 10 to 15 workers at each of its warehouses, he says, just to track inventory to ensure that the actual warehouse stock is what the computer says it is, and that nothing is obsolete or missing.
“If we could scan every item,” Mayorek states, “we could eliminate a lot of unnecessary steps and shorten up the supply chain.” While he says RFID has been slow to be adopted, in some cases that is because no one wants to be the first to adopt the technology. “It takes someone like Conair and USA ID to prove the results first,” Arguin says.
By the third quarter of 2010, Conair expects to have every product tagged.