When warehouse workers at Singapore company Keystone Cable process an order for its telecommunication and electric cables, they need to locate large reels of specific products and then return them to storage so that those reels can be accessed again for future orders. The warehouse contains thousands of reels, and a single worker can spend 30 to 45 minutes locating the correct one. The company has installed a technological solution that employs passive ultrahigh-frequency (UHF) RFID tags on reels, as well as on racks at its storage locations. The firm reports that a forklift driver now requires only about five minutes to retrieve a cable reel. The RFID solution, provided by the Singapore Institute of Manufacturing Technology (SIMTech), includes Xerafy passive Data Trak II RFID tags and Phychips‘ Arete Mobile Pop Smart RFID dongle readers connected to Android phones.
Keystone Cable manufactures insulated cables and sells them to customers in the building and infrastructure, oil and data, and data communications sectors. The company produces thousands of different types of cables, each stored on its own reel—a drum made of either steel or wood. Wooden drums range from 32 centimeters by 60 centimeters in size (1 foot by 2 feet), to 70 centimeters by 100 centimeters, while steel drums range from 85 centimeters by 120 centimeters in size, to 120 centimeters by 240 centimeters (4 feet by 8 feet). A fully loaded reel can weigh up to five metric tons (11,000 pounds). Therefore, retrieving the appropriate cable to fulfill each customer’s order proved to be a major challenge. A warehouse worker received an order form from the sales department, indicating the serial number printed on the reel and the length of cable to be cut from that drum. He then searched for that reel. Making this process even more difficult, the cables look very similar, so ensuring the correct serial number on a product before picking it for a customer is crucial.
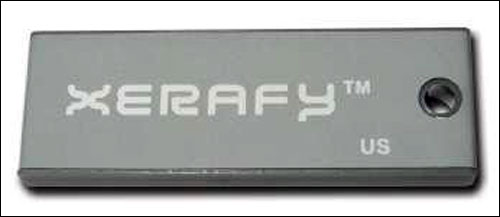
The employee used a forklift to move the drum to the cutting area, where the cable was cut and recoiled onto a smaller reel. That smaller reel was then shipped to the customer, and the larger drum was returned to the storage area. Prior to the RFID system’s installation, staff members typically just looked for the nearest available storage space and placed the reel there.
The cable company sought a quicker way for workers to find reels. The firm first looked into active RFID tags, says Derek Zhu, Keystone Cable’s senior strategy manager. However, he explains, “the system would have been too complex for our situation,” due to the large reader infrastructure that would have been required, and “the cost was much more expensive [than passive RFID)], far exceeding our budget requirement.”
“The passive RFID solution proposed by SIMTech was both economical and suitable for our situation,” Zhu says. Keystone Cable began conducting feasibility tests with SIMTech in spring of this year, and the system was taken live in June. Using an RFID reader dongle that plugs into a smartphone’s headphone jack, as well as SIMTech’s smartphone app for linking the collected data to a hosted server, enables the solution to remain relatively low-cost. By buying passive tags rather than active ones, the company also saves money.
Keystone Cable has applied tags directly to hundreds of steel storage racks, both indoors and outdoors, at its more than 100,0000-square-foot facility. It also applied two tags to each of approximately 500 reels, one on each side, in order to ensure that the unique ID number encoded on the tag can be captured by a reader, no matter on which side of the reel a user is located. Each staff member carries a Phychips RFID reader plugged into a smartphone. The SIMTech phone app manages the read data culled, displaying order details as well as the results of read events, and indicating when the correct reel has been located for a particular order, as well as when a drum is put away in the right location.
When the warehouse first receives a reel of newly manufactured cable, a worker inputs that reel’s serial number into his phone, and then interrogates the reel’s tag ID to link the two numbers. Once the drum is put away, the employee inputs the reel’s ID number into his phone app, which then displays the rack location tag ID. The rack numbers are very systematic, Zhu adds, and personnel know where to find that rack ID within the facility. Once the worker puts the drum away, he reads the tag affixed to that storage rack to confirm the specific reel has been returned to the specified storage space.
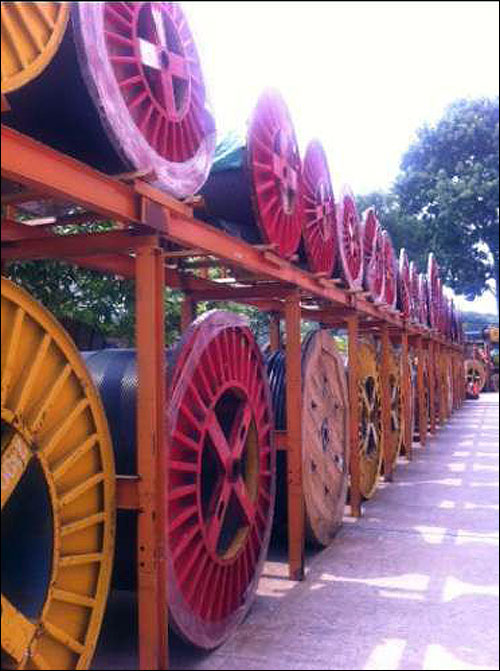
When a paper order is received, that order still shows the reel’s serial number, and with the RFID solution, workers then input that ID number into the handheld. The app determines which RFID number is linked to that reel, along with the storage rack’s tag ID number. It then displays the rack ID on the user’s handheld device, and the employee can simply drive to that location and retrieve the proper drum.
In the past, after cutting the length of cable required to fill an order, a worker merely placed the reel back in any convenient available storage space, which made it difficult for employees to find it for a subsequent order. With the SIMTech solution, the staff member returns the reel to the authorized location from which it had come, and again reads the location tag to ensure it is being put away properly.
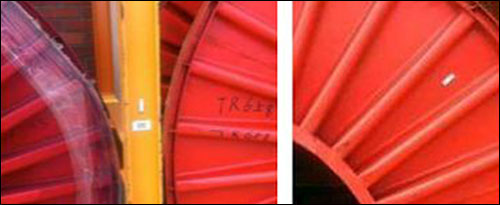
Since the system was installed, the company reports, the process of retrieving reels has been reduced from 30 to 45 minutes, down to about five minutes.
“We are currently looking into expanding our warehouse capacity,” Zhu says, “so we will continue to use this technology to track more drums stored at more locations.”