Three years after deploying passive 125 kHz RFID tags to track its tool usage, the Byrne Group, a British concrete substructure construction firm, has expanded its use of the system to identify users of its 16,000 assets—including tools, excavators, trailers and other heavy equipment, as well as consumables like gloves and boots—across its numerous construction projects. The company is also using the technology to manage the online ordering of those items.
By introducing RFID-enabled ID badges for each of its up to 2,000 employees, the Byrne Group can maintain an electronic record of which personnel utilize which assets. In this way, the company can prevent an unqualified employee from operating equipment for which he or she is untrained, as well as track which consumable assets have been used on a particular project, and identify workers who use too many of a specific consumable item, or that take an asset without returning it.
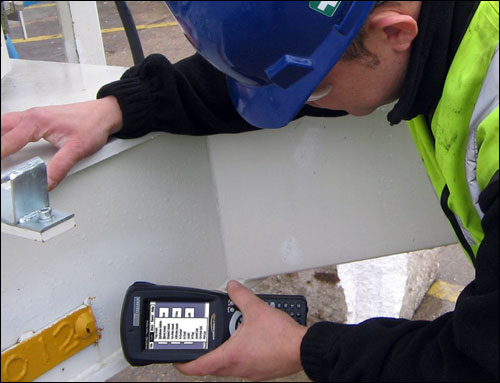
Based on the reduction in theft alone, as well as improved efficiency, the Byrne Group expects to recoup its cost of expanding the RFID system by next year, says Paul Brooks, one of the firm’s managers.
In 2008, enterprise asset-management solutions supplier 4H Solutions provided the Byrne Group with its original RFID-based tracking system which included 4H’s Assettagz software, which interprets RFID read events and provides information and alerts based on those events. Independently, 4H Solutions provided Byrne with COINS‘ Plant Manager software, an application for asset-managing application running on a server hosted by 4H. Byrne used Plant Manager to compile an electronic catalog of all of its equipment and consumables, enabling job site staff to order equipment and supplies from the central depot via the Internet.
The Byrne Group has projects throughout the United Kingdom, including in Heathrow Airport and at the London Olympics Stadium. Prior to using RFID, the company manually tracked assets on its various sites, using pen and paper. The firm estimated it was losing £100,000 ($153,000) worth of consumables and other small items annually. Not only were assets misplaced or stolen, identifying what was needed for a particular project and recording that transaction was a flawed process, the company reports, since each engineer or foreman had his or her own way of describing those items. Furthermore, consumables such as gloves, helmets and other personal protective equipment (PPE), as well as timber, small tools and signs, were not being tracked at all.
Initially, in 2007, the company attached low-frequency (LF) 125 kHz RFID tags to all of its products. The tags, which operate via the proprietary RFID air-interface protocol, come in several forms: plastic credit card-style tags for PPEs, glass tags embedded in tools and molded plastic tags for lifting gear. By using Psion Teklogix‘s handheld readers at the company’s central depot in Mitcham, where all equipment is stored before being commissioned to construction sites (currently, there are 11), employees could store data regarding which items were checked out, and when that occurred. Those assets are then moved to “mini stores” on the construction site, to be distributed as necessary. In August 2008, each staff member at the Mitcham depot was issued an RFID-enabled ID card containing the same type of 125 kHz RFID tag.
Each asset tag stored a unique ID number corresponding to data about that item, which was stored in the server hosted by 4H Solutions. This data included limited information regarding its inspections record. The Byrne Group wanted more data, however, such as which specific individuals had utilized a particular piece of equipment, and if they were trained and authorized to do so. The company also wanted to monitor which personnel used consumables, as well as the amount being used. This would enable it to address problems if, for instance, specific employees were taking out too many gloves or other items, and to also track the exact quantity of PPEs being used on a particular job, so that similar jobs could be price-bid accordingly in the future. In addition, the company wanted to improve its ordering system, so that orders could be placed electronically by each construction site’s mini store, thereby making the ordering system more efficient and reducing the number of errors that could be made on phone- or paper-based orders.
In late 2009, says Andrew Davies, 4H Solutions’ sales director, the Byrne Group launched the next phase of the system, to improve the inventory system by integrating Assettagz with the Plant Manager software. Consequently, a worker at a construction site can access the e-catalog using his ID number, in order to select items and place an order, which is then sent to the Assettagz system to be picked.
Consequently, a worker at a construction site can access this e-catalog using his ID number, in order to select items and place an order.
At the Mitcham depot, workers retrieve orders off the server, along with a picking lists for those assets. Those picking lists are then sent to the handheld devices at the depot via a Wi-Fi connection, using Assettagz software, which interprets RFID read events and provides information and alerts based on those events. On the handheld device, the software displays a picking list that an employee can utilize to collect the ordered items. Those assets are then delivered to the job site. When items are sent back to the depot, a staff member uses the handheld to read their tags, and the Assettagz software identifies those objects and indicates they have been returned.
Also in late 2009, the Byrne Group began providing ID badges to each of its employees. At every construction site’s store, a worker can present his or her ID badge, which is read using one of the two handheld readers at that location. The tags of the items requested by that staff member are then read as well, linking them to that particular individual. If he or she is not trained to use that asset, the handheld’s screen displays an alert warning the store’s staff not to allow that transaction. All data is transmitted from the handheld to the server via a GPRS cellular connection.
If the item is due for inspection, an alert is also displayed in the system, so that management can know to schedule the appropriate inspections. Inspectors can then use the handheld device by first reading the tag, along with their own ID badge, and following prompts related to the inspection, indicating what was done, along with the equipment’s condition.
After the system was expanded, Brooks says, employees began using fewer consumables. The Byrne Group now knows more accurately when it needs to replenish a specific consumable at a particular mini store, based on the RFID data. What’s more, he notes, the company has reduced the need to reorder items due to an initial order not having been filled, and has also decreased the labor previously spent searching for missing equipment, as well as maintaining paper-based records of which personnel had ordered and received which equipment.