A container manufacturer has begun testing an Industrial Internet of Thing (IIoT)-based automated sensor-management solution from Arrowhead Systems for its depalletizers, to capture data about the equipment’s health and thereby prevent production downtime. Based on those results, the company, which has asked to remain unnamed, plans to test the system for adoption in palletizers, in which aluminum cans or other containers are automatically stacked for shipment to beverage companies. The sensor data is captured, managed, displayed and forwarded to users via Movicon.NExT 4.0 software, supplied by Emerson Automation Solutions.
The aluminum container industry is under pressure, the company reports. A boom in cans for sodas, seltzer drinks, water, beer and wine is creating an historic demand for aluminum containers. Arrowhead’s research, the firm adds, finds that the current global capacity is 285 billion drink cans annually, despite a global demand of more than 350 billion. The industry will thus be challenged to keep up with this demand by manufacturing more cans at a faster pace.
Arrowhead partnered with Emerson Automation Solutions in 2019 to provide a machine health monitoring solution for its high-speed palletizers and depalletizers, aimed at reducing the risk of downtime for production. The company’s Busse SJI Viper High Speed Bulk Palletizer and Alpha Turbo High Speed Depalletizer each employ Emerson’s machine health monitoring technology, with a focus on pneumatic systems, to provide users with overall operator effectiveness. The system, which utilizes Wi-Fi, IO-Link or other cable connectivity, is adaptable for use with other container products.
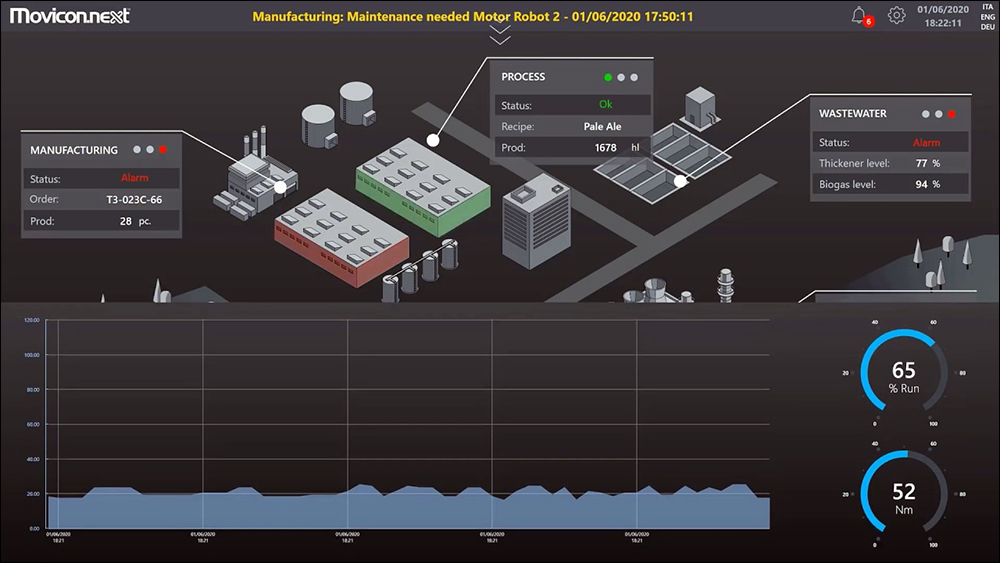
A sample Movicon.NExT 4.0 screen
Arrowhead Systems makes conveyor, packaging machinery and line-productivity solutions for customers in many sectors, including food, beverages, household items, personal-care products, container manufacturing and more, according to Tim Krueger, Arrowhead’s president and COO. Its Busse palletizers automate container stacking where cans are manufactured, while its depalletizers then remove those containers from pallets at a beverage manufacturer’s site. The firm also provides engineering services for aftermarket support.
The palletizers are used at the end of a manufacturing line to align containers and stack them on pallets, at a rate of 4,000 cans per minute. The company’s customers that palletize containers send products to their own customers (food and beverage companies), where Arrowhead provides depalletizers to offload them so they can be filled with products. The Busse system has been in use since 1946, and Arrowhead was launched in 1974.
Arrowhead says it currently provides the majority of high-speed palletizers used by the can manufacturing industry. The company’s products have historically come with IO-Link sensors to monitor the health of its equipment, capturing key data such as motor temperatures, component vibrations and air loss. That information helps users track how cylinders function, as well as monitor whether any problems occur with the motors, for example. Traditionally, however, the collected data had to be viewed onsite, and it could not be shared remotely in real time.
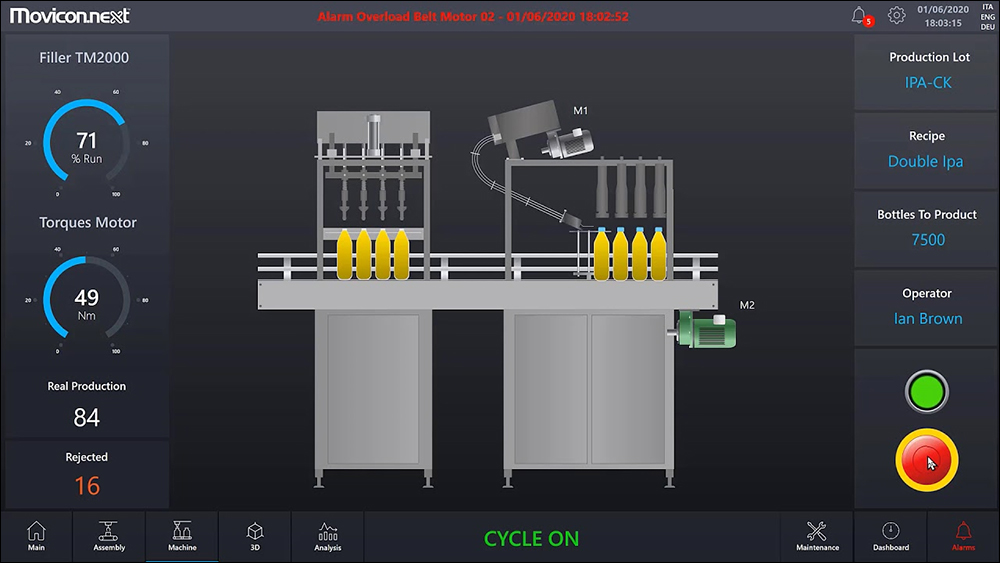
Another Movicon.NExT 4.0 screen
With the Emerson partnership, Arrowhead is offering a health-management solution that collects sensor data and delivers relevant information to the operator or maintenance team, which can include system analytics and health information. The information is processed at the edge by a local data historian with a local display, or via remote monitoring on a tablet or smartphone that provides operators with an easily accessible tool to monitor health, according to Chris Noble, an Emerson business-development IIoT consultant for food and beverages.
Arrowhead built the system to help the container industry address the increased demand for products by ensuring equipment failures do not cause delays. Downtime for maintenance can be costly in large-volume manufacturing, Krueger says. In fact, it can cost companies tens of thousands of dollars per hour in lost revenue if a production line shuts down. Unexpected equipment failures sometimes require hours or days of downtime if, for instance, a replacement part is not readily available.
Therefore, Arrowhead began working with Emerson to develop its health and wellness monitoring system to provide automated data and predictive maintenance analytics. The system is intended to give operators, maintenance personnel and management insight into what is happening to equipment and when an issue needs to be addressed. The new solution captures key conditions, and Emerson’s software manages that data and provides information on dashboards that not only display what sensor information falls outside established parameters, but also provides some diagnosis.
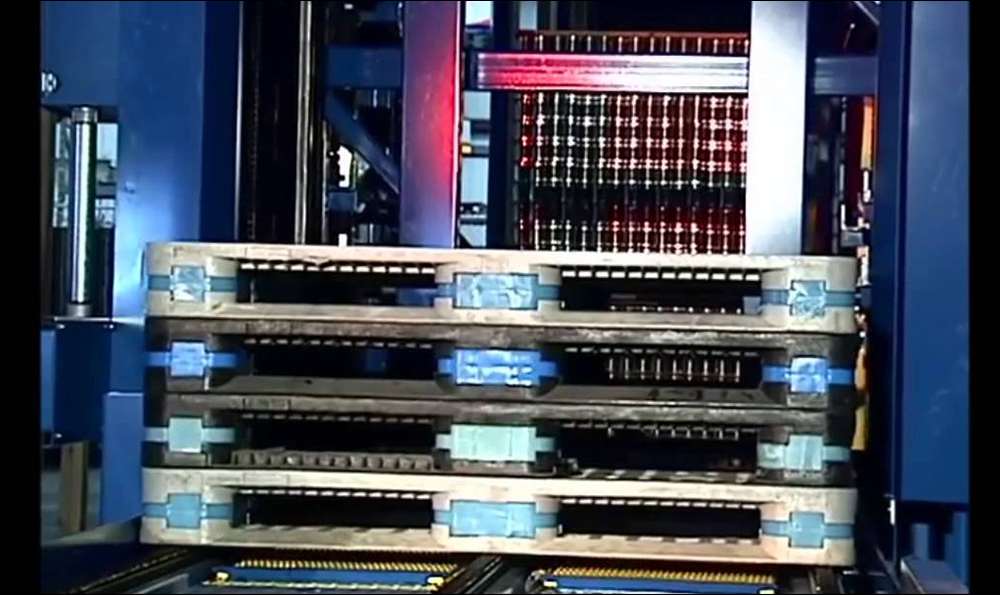
The Busse SJI Viper High Speed Bulk Palletizer
The collected information can be forwarded to authorized parties via text or e-mail. In addition, Emerson’s software captures trending data over time, in order to identify any anomalies. The system can be integrated with production software. How data is captured, managed and shared varies according to the needs of a particular manufacturer, Krueger says, adding, “We work with customers as to how they want to use this data.”
For instance, Krueger says, some businesses already have high-level production-monitoring systems in place, in which case data can be pushed to those existing systems so a plant manager can receive a notification, for example, that a problem is pending. The solution is designed to be agnostic when it comes to management software. “We’re just one piece of a line,” he states. “Companies don’t want to buy 15 different systems or subscriptions. With Emerson, we are providing a system so that companies can take that data and use it however they want, through their own systems.”
For the future, Arrowhead now has a potential roadmap to offer a service by which it can manage data as a service for those using its equipment. “That depends on the needs of our customers,” Krueger says. The technology is intended to keep production high, even as businesses meet increasing demands, with the additional challenge of a changing workforce. For instance, manufacturers are contending with potential “brain drain” as site management and operators are retiring. Some firms face challenges in finding skilled maintenance technicians to take the place of the more experienced workers they replace.
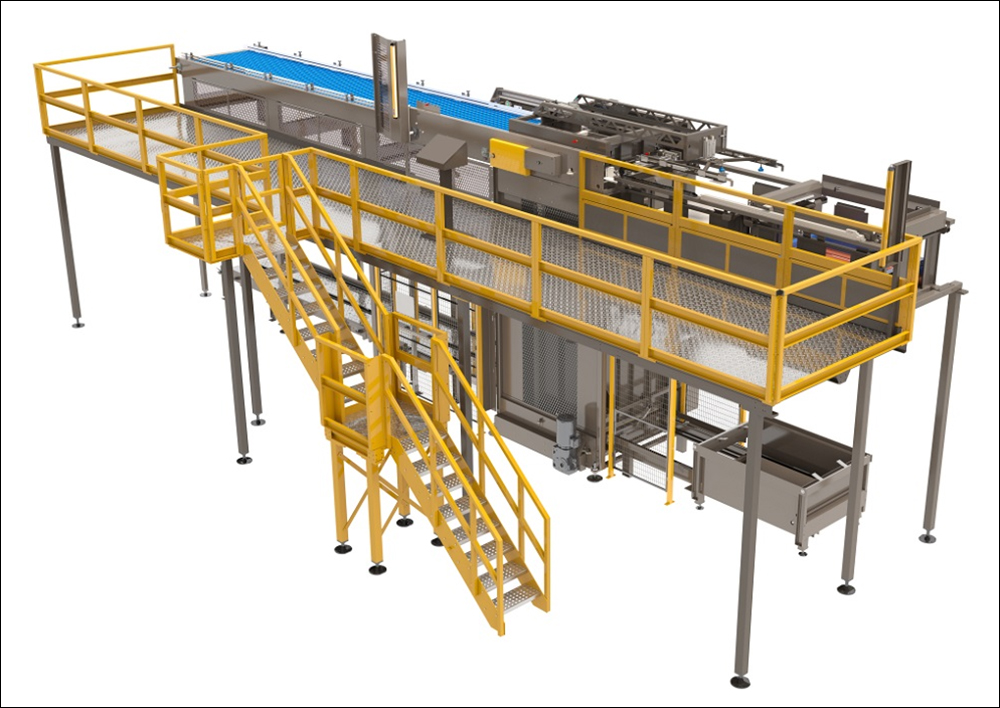
The Alpha Turbo High Speed Depalletizer
Therefore, Krueger reports, the Busse machine health monitoring system was designed to be easy to use—in fact, his 13-year-old son could operate it after only 30 minutes of training. Arrowhead worked with onsite engineers at the container manufacturing site, along with Krueger’s son. The group trained the teen, then altered some sensor data and put the youth to work observing the system. He was able to identify when there was a problem, and the onsite touchscreen displayed where that issue may have occurred so that he could generally describe where maintenance might be required. “The engineers did great,” Krueger recalls, “because they were able to make it possible for him to do that effectively.”
Emerson Automation Solutions provides solutions for the oil and gas and manufacturing sectors, including software for asset performance management, control and operator performance, digital twin and simulation, and manufacturing execution systems. Arrowhead is leveraging Emerson’s latest automation and control software, Movicon NExT 4.0, which can be provided in either wired or wireless format, Noble says. “It’s very flexible,” he states. “Out-of-the-box data can be captured locally, or it can be in the cloud where those not on the plant floor can view data.”