AL-KO, a German producer of industrial air conditioners for airport hangars and other spaces, is employing a radio frequency identification solution to plan its production more precisely, by tracking the movements of parts between two production sites located 550 kilometers (342 miles) apart.
Since most of the air conditioners that the company makes are customized for particular buyers, each model must be configured differently. This requires that different parts be grouped together for each order at a single location, and then be shipped to the company’s final production site.
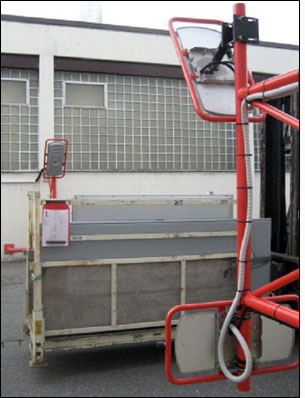
Parts, such as housings for the air-conditioning systems, are produced in the city of Lutherstadt Wittenberg, not far from Berlin. Final production of the air conditioners occurs in southern Germany, in the town of Jettingen-Scheppach. If a part is unavailable during production in Jettingen-Scheppach, the resultant delays can be costly to AL-KO, says Alexander Lins, an industrial engineer and AL-KO’s head of warehouse logistics in Jettingen-Scheppach.
Before the RFID system was deployed, production managers were often unsure of which specific parts they had on hand at any given time. “Colleagues in Wittenberg send the parts we order to Jettingen-Scheppach on a daily basis,” Lins explains, “but sometimes, we weren’t clear about which parts arrived overnight.”
That, Lins says, is why AL-KO’s director decided to test an RFID solution to track parts moving between the two sites, and to provide a real-time overview of the production status in the company’s existing SAP system.
AL-KO asked Vienna-based auto-ID specialist B&M to design and test a solution that would address this issue. Following a short and successful pilot, the system was installed at the beginning of 2009. The error rate prior to RFID’s implementation, according to the company, was 10 percent; the percentage of improvement since the system’s deployment has yet to be quantified.
B&M Tricon designed a system in which Deister Electronic UDC 160 ultrahigh-frequency (UHF) on-metal transponders are slipped into pouches for delivery notes attached to shrink-wrapped parts in Lutherstadt Wittenberg. The parts are produced in that city, and workers pick and pack individual orders of those parts that must then be sent to Jettingen-Scheppach for final production.
Multiple orders of various products, such as air-conditioning panels, are placed on a single load carrier. Once that carrier is full, an employee shrink-wraps it and assigns it a Handling Unit number generated by the SAP system. That number is then encoded on the Deister tag using a Deister UDL 50 desktop reader. A worker slips the tag into the delivery-notice pouch and zips it closed, attaching the pouch to the outside of the plastic-wrapped load via a Velcro-like fastener.
During the next step, a forklift driver moves the load carrier to the truck-loading area. The driver utilizes an onboard tablet PC to input the license-plate number of the truck onto which he or she plans to place the carrier, and then moves the pallets holding the tagged air-conditioner parts through an RFID gate. The system records the tag’s Handling Unit number, the truck’s license-plate information and the time of loading, and then notifies the Jettingen-Scheppach plant regarding which parts are en route, via an automatic dispatch notification. With receipt of the notice, managers in Jettingen-Scheppach can better manage their production schedules.
Upon arrival in southern Germany, the goods are again moved past an RFID reader gate, and the items’ arrival is recorded in the SAP system. Tags are removed from the pouches and returned to the Lutherstadt Wittenberg facility the next time that a truck drives that route for the company. AL-KO currently has roughly 1,400 tags in circulation.
Prior to the system’s implementation, shipments between plants were tracked by hand on a spreadsheet. The staff manually recorded up to 200 notations daily that had to be input into the computer by an employee working overnight, when the goods are transported.
AL-KO spent €240,000 ($296,000) on the application for hardware, software, programming and consulting services. Lins reports that the system has benefitted his company, by providing it with a definitive accounting of which materials and load carriers are on the move. What’s more, the technology has reduced the amount of administrative work in the process.
In addition, all materials not loaded onto trucks can now be accounted for as well. Previously, a list of unshipped materials had to be compiled manually. Now, the system calculates what has been left behind, by comparing data regarding which parts were ordered and which were actually loaded. This information, Lins says, enables AL-KO to ensure that its inventory is kept up to date in real time. The company currently has no plans to expand the system.