On Apr. 19, 2010, RFID Journal presented the fourth annual RFID Journal Awards for outstanding achievement in radio frequency identification technology to four companies at RFID Journal LIVE! 2010, our eighth annual conference and exhibition. This year’s winner for Best Use of RFID in a Product or Service was Almacafé.
More than 500,000 of the small coffee farms, many family-owned, that dot the mountainous regions of Colombia sell their beans to the National Federation of Coffee Growers of Colombia. The nonprofit organization is dedicated to boosting the farmers’ standard of living, with programs that minimize production costs and improve coffee quality and sales. It also runs Almacafé, a subsidiary that handles the warehousing, quality control and logistics of the coffee the Federation sells around the world. By providing more value to Federation customers, Almacafé reps say, the coffee growers also benefit.
One Federation initiative: a specialty coffee program to identify and market high-quality coffee beans, which have exceptional characteristics and/or originate from unique regions. Roughly 27 percent of the Colombian coffee exported in 2009 was specialty coffee, and the Federation handled about 43 percent of that. Customers pay up to 200 percent more for specialty coffee, and the premium is transferred in its entirety to the coffee growers themselves.
Specialty clients demand more services for the extra expense, according to Gonzalo Rivera, Almacafé´s general manager. They expect to be able to “follow the trail” back to the regions and conditions that produced a notable sack of beans, for instance, and quick access to order status. To compete more effectively in the global market, Almacafé deployed a radio frequency identification system in 2007 to monitor specialty coffee throughout its internal supply chain—from the farms to the warehouses, and during processing and bagging for export to roasting and trading facilities.
“It is certainly very important for our customers, since they are able to access the information of their coffee—including the origin, the coffee grower and the farm where it was cultivated,” Rivera says. “They also can access information about where the coffee is in the Almacafé facilities, and about the milling and warehousing conditions.”
Brewing a Solution
Almacafé first considered tracking beans in 2004, at which time it thought bar-code technology could provide transparency along the supply chain. But it discovered that reading bar-code labels on coffee sacks is unwieldy and time-consuming, and when bags weighing more than 40 kilograms (88 pounds) are hauled around, their battered labels sometimes become unreadable. So in 2006, Almacafé turned to RFID technology.
The customized solution developed by Almacafé requires that each Gen 2 RFID tag be encased in a wear-resistant plastic capsule. The Federation pays for the tags, which cost about 25 cents each. “The National Federation of Coffee Growers has an amazing database that includes all the coffee growers and the production capacity of each of the farms,” Rivera says. “Based on this information, the Federation gets the necessary quantity of capsules with the RFID tags.”
Before the tags are distributed to the farmers, each tag is assigned a coffee grower identification number, which is associated in Almacafé’s RFIDTrack database with the ID number of the farm and the specialty coffee program code. As soon as the growers fill the coffee sacks, they tag the bags.
The growers sell the coffee to any of the Federation’s 35 cooperatives, and from there the bags are transported to one of Almacafé’s 15 warehouses, all of which became fully RFID-enabled in March 2009, with fixed and mobile interrogators. The tags are first read as soon as the coffee arrives at a warehouse. Two RFID antennas on each side of the conveyor belt ensure 99.99 percent read accuracy, Rivera says. The tag data and delivery time are stored in the RFIDTrack database. SysTrack, a Web-based application, manages the RFID information.
Before the beans can be exported, they must be processed, first in the threshing machine and then in the milling plant. The tags are read at each step in the process and associated with specific orders. If, at any point, a bag of coffee is rejected because it doesn’t meet quality standards, a SysTrack module records that the associated tag will not be part of the final delivery. “When the coffee analysis reports that the coffee does not meet the quality required for a specialty coffee customer, the coffee is rejected and the system is updated,” Rivera says.
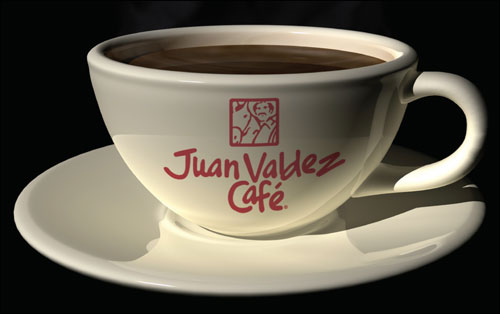
Almacafé does not use RFID beyond its warehouses—after milling, the coffee is packed in bags without RFID tags for shipping to destination ports and on to client facilities—but customers can log onto BeanTrack, another Web-based application, to track their orders. That includes the coffee lots assigned to them, information about the coffee growers and farm soil quality, and photos of the locations each sack of beans passed through on its way to the warehouse.
The Sweet Aroma of Success
Some 25,000 coffee growers participate in the RFID program. “The most important benefit for the Federation is to provide added value for its specialty coffee customers and differentiate itself among coffee exporters worldwide,” Rivera says. “It´s the assurance that coffee doesn´t get mixed and the quality produced at each farm is maintained throughout the processing chain. Also, it gives us the option to replicate qualities for our customers by going back to the farms and regions where coffee was procured.”
The RFID project is a jumping-off point to another business opportunity for Almacafé: sourcing its solution to others in the java business. The Federation authorized Almacafé to promote the use of its traceability model to the coffee industry outside Colombia.
“During one of the yearly exhibitions organized by the Specialty Coffee Association of America, we made contact with an American roaster who trades with Colombia and other origins, like Tanzania,” Rivera says. “We signed a pilot project with them in order to adapt our traceability model to the Tanzanian coffee market, which has logistical and operational characteristics very different from those we have in Colombia.” The project, conceived in 2008, has progressed to the point where the technology has been installed.
The RFID system also helps promote Colombian-grown coffee to consumers, Rivera says. The Juan Valdez Café is a coffeehouse chain in Colombia—with coffee shops in the United States, Chile, Ecuador and Spain as well—that promotes and retails Colombian coffee. At these shops, customers can log onto a kiosk, enter the code from a bag of coffee they’ve purchased—which has been affiliated with the RFID tag from the original sack of coffee used by the grower—and learn about the farm and region their beans came from. Similarly, coffee connoisseurs can confirm that the morning cup of Joe they’re sipping at home is special, by visiting the Juan Valdez Café Web site and clicking on the Expert Corner interactive tool.
Overall, the RFID project is “a case of success” not only in its use of the technology but in its addressing “the socio-economic aspects of the coffee community,” Rivera says. It inspires confidence in the quality of the product among the businesses that source Colombian coffee while making the coffee growers an active part of the process. RFID technology creates for them an awareness of the value of the product they produce, while enabling the Federation to stay informed about which growers will be paid a premium for their specialty coffee.