The Internet of Things (IoT) is receiving a lot of attention lately. It is real and will endure for the long term. The IoT fuels relentless transformation, comprising a world of smart products, green initiatives, virtual reality, connectivity and convergence.
The challenge for technology and solution providers is to capitalize on the movement to connect everything using various personal, commercial and industrial wireless mesh networks (or what I term “MeshNets to the Cloud”). Frost & Sullivan estimates that 80 billion devices will be connected by 2020.
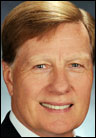
We are moving steadfastly toward an era in which we can sense, locate, identify, track, monitor, measure and analyze everything from consumer products to industrial assets, cargo and vehicles, as well as personnel (the IoP, perhaps).
For consumers, the new buzz is about personal, wearable hub networks with wireless sensors. And now, iBeacons are coming to their neighborhoods. For businesses, everything seems to be moving to the cloud. For everyone, it means being connected to nearly all things globally.
The RFID and automatic identification and data capture (AIDC) industries have all types of wireless devices, but the markets demand solutions. It is not enough merely to offer RFID tags, readers, antennas, cables and such. Everyone knows that, I hope. The challenge is to focus on what Mark Roberti emphasized in a recent article (Three Lessons the RFID Industry Can Learn From Apple) that discussed three major lessons from Apple for the RFID industry: (1) create a “whole product,” (2) make products easy to use and (3) market aggressively.
Customers do not want partial solutions or disconnected products. Bluetooth RFID tags are an interesting niche product, but so what? They must address a need or solve a problem. Customers also want to see that any planned solution is complete, with all the necessary devices, a minimally disruptive infrastructure, automated and mobile operation, and the ability to be used and integrated easily into existing customer software systems, and that it is supported by a service and support plan that will ensure the long-term delivery of the expected benefits.
Customers also do not care about RF frequencies and technology types. Why should they have to be educated about Bluetooth Low Energy (BLE), low-frequency (LF), high-frequency (HF), ultrahigh-frequency (UHF), Wi-Fi, ZigBee, ultra-wideband (UWB), microwave and other technologies? Then there are real-time location system (RTLS) solutions, the Global Positioning System (GPS), differential GPS (DGPS), indoor positioning systems (IPS) and Near Field Communication (NFC). More often, in the future, we will see multi-frequency and -technology products combined into a single device that automatically adapts to the required frequency for specific applications, and can be active, passive or both.
At present, active UHF RFID tags are gaining traction in the following high-profile applications for which suppliers have provided solutions: construction laydown yards and storage areas (materials management); container tracking at seaports (locationing and reefer monitoring); discrete manufacturing and finished goods (quality and inventory control); power distribution and greenhouse gas reduction (smart meters); apparel and retail (inventory management and procurement); oil, gas, mining and energy (security and personnel safety); transportation and cargo (distribution coordination); and pharmaceuticals (pedigree and authentication).
In each of these applications, the systems integrator—either by itself or, more typically, teamed with technology providers—supplies a solution in which software, hardware and services are integrated as a whole product that addresses a customer’s specific need or solves a particular problem.
For solution providers and their partners, the challenge is to manage a development team for the requisite wireless and wired hardware, as well as a so-called “agile” software-development organization that can adapt easily and quickly to customer changes. This is especially important as requirements evolve, since response time is critical as new competitor offerings become available.
No IoT application solution, in the near term, will be satisfactory right out of the box. All companies will expect to have the system customized to their specific needs, organizational requirements and language. The software-development team, working together with necessary wireless infrastructures, will need to be able to react in a matter of hours or days instead of weeks or months. Customers want to see the “solution in action,” accessible from the cloud, before making final decisions.
Software acts as the glue that ties the solution together. In an IoT wireless world of data capture, the information must be collected and managed via a rules-based engine that presents it in ways that bring clarity and actionable intelligence to what is happening.
Visibility for the IoT is made possible by empirical and statistical data analysis, using a variety of dashboard metrics, charts, graphs, maps and more, based upon proven formulas and real-time data capture. Answers to constantly changing questions are required: Where are my things? Where have they been? Where are they going? What is their condition? What decisions do I need to make about them? Such operational visibility allows for increased situational awareness to effect timely and intelligent decisions.
Vendors of active RFID tags and readers will have to complement their offerings with software that brings both automation and visualization to reality. One example of this is in the construction business, in which hundreds of thousands of high-value components need to be shipped and stored on or close to a construction site. Those items can be tagged at a fabricator, tracked throughout the supply chain and transported to the site, where they can be automatically identified and reported to the customer’s enterprise resource planning (ERP) software that submits entries for goods receipt, inventory control, accounts payable and other functions.
Then there is the use of sensor tags to determine the correct time for the curing of concrete. Data culled from the RFID tag, embedded in the concrete, measures the temperature and reports it automatically. In turn, the graphs and statistics will show, on user tablets, when the curing is completed and the next pour of concrete can take place safely, and at the right time to meet construction schedules.
Other proven solutions include tracking and monitoring shipping containers as they are moved off ships and are then stacked and stored at a port terminal. Temperature sensors provide real-time monitoring of reefers, as well as graphical status and alerts for perishable goods stored within certain containers. All of this will be coordinated with logistical requirements for transport and distribution.
In the oil and gas industry, personnel can be monitored. During crises, signage can automatically direct workers to safe zones or evacuation areas. The operations center on an oil rig or onshore can show in real time, on a map of the facilities, where personnel are located and problems are occurring, in order to facilitate an immediate and effective response. To make this goal achievable, personnel RFID badges, sensors (such as those for detecting flame, gas and temperature), and video and access control for the facility must be integrated with IT systems that display the real-time status of operations on computer screens. The future will include tagging other items, such as assets, tools, specialized equipment and supplies tied to workers and operations.
In each of these application success stories, future demands will increase to tie in other things for identification, tracking, tracing and status. In addition to knowing where an asset or container is located, so many other questions will need to be addressed as well: Where did it come from? What is inside? When and where is it supposed to go? On which truck is it being loaded? Who is the driver? What is the best route for transport? Is the cargo insured? What is its estimated time of arrival at its final destination? What maintenance needs to be conducted? What about spare parts?
This will force the continued development of RF-based sensors to track and record everything—temperature, humidity, vibration, motion, water, flame, smoke, light, speed, gas and more.
The entire Supply Chain of Things (SCoT) can be made visible to fabricators, suppliers, carriers, customers or users, and service providers.
RFID reader hardware will need to operate on smaller, mobile devices. Customers want to be able to use tablets, smartphones, and other handheld and wrist-carried and wearable devices in the field—all delivering data to the cloud that can be accessed easily from anywhere, and at any time.
This will require a great deal more flexibility in solution definition, technology application and development time for solution providers. Customers want to track all things important in their world, in order to affect safety, security and operational effectiveness—all while not interrupting existing processes or work methods.
Ultimately, those who can deal with this kind of rapid change in the Internet of Things world will emerge as the solution leaders of tomorrow.
John Shoemaker has spent the past 25 years in the AIDC industry and functioned at the C-Level for several technology companies with wireless and sensor solutions. Currently, he is the executive VP of Identec Solutions, a supplier of active UHF RFID technology designed to increase people safety, productivity and efficiency in harsh environments.