Japan Airlines (JAL) officials realized there was a return on investment to be gained from using radio frequency identification to streamline maintenance operations. During a three-day demonstration last December in Tokyo, RFID tags were used to track the expiration dates on oxygen generators onboard a 777 commercial airliner. The demo showed that the inspection process that now requires two JAL mechanics to spend six and a half hours each unscrewing and removing ceiling panels in an airplane and visually checking generator dates could be cut to eight and a half minutes for one mechanic with a handheld RFID interrogator.
The RFID demonstration was orchestrated by Boeing for JAL and representatives from other airlines. Oxygen generators, which provide breathable air to passengers in the event an airplane cabin loses pressure, need to be monitored regularly; each has an expiration date, and airlines risk fines and violations if generators exceed those dates. The inspection process is repeated on each JAL airplane every 19 months. But because the task is so labor intensive, if the airplane is already undergoing heavy maintenance, oxygen generators are sometimes replaced early—with 20 percent of their life still remaining. RFID could change that. Handheld interrogators could be used at any airport at any time to inspect the generators, which would extend their life and allow JAL to lower inventory by some 80 percent, Boeing officials estimated.
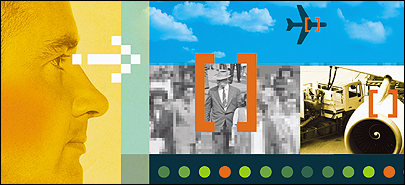
JAL officials were so impressed that they drew up plans to conduct an RFID pilot using oxygen generators, starting perhaps as soon as this summer. They also foresee other uses for RFID, such as ensuring enough life jackets are on overseas flights. “I think that’s one small step for Boeing and JAL,” says Kenichi Hayashi, a JAL engineering official who participated in the demonstration, “but I hope it will be one giant leap for both the aircraft and RFID industries someday.”
The potential to dramatically cut down on labor, inventory and other costs associated with maintenance, repair and overhaul (MRO) is one of the main reasons aerospace companies are testing and/or deploying RFID. Commercial airplanes have a quarter-century lifespan, and that means MRO operations can be a major expense, not to mention a logistical nightmare to coordinate. RFID tagging of parts is seen as a way to reduce flight delays and cancellations by ensuring the right parts are in the right location when needed. At the same time, RFID could help aerospace companies comply with an assortment of safety regulations that require data be kept to document repair histories of parts—a process now done largely on paper.
The world’s two dominant commercial airplane manufacturers—Boeing and Airbus—are working on standards to use RFID to mark individual parts and keep maintenance records on the RFID tags. But that’s just one RFID initiative. At virtually every level in the aerospace industry’s supply chain—which includes airplane manufacturers, suppliers, airlines, airports and government agencies—stakeholders are deploying or testing RFID to help eliminate waste, cut costs, gain visibility through the sharing of information and improve safety. While suppliers are working with airplane manufacturers and the U.S. Department of Defense, which has its own RFID requirements, they’re also using RFID internally to track assets and improve processes. At the same time, airports, airlines and airport management companies are looking to RFID to help them address growing consumer complaints about delayed flights and lost baggage (see sidebar on page 36).
But some suppliers have been hesitant to embrace RFID for parts marking, fearing that it will cost—rather than save—them money. The aerospace industry is also facing financial pressures, which has impacted investment in RFID due to infrastructure costs. In addition, some of these RFID applications require tags that have more memory and/or are more durable than those being used to tag cases and pallets in the retail industry, and aerospace companies are waiting for vendors to produce them in the quantities they need.
Still, RFID spending in the U.S. aerospace market is forecast to grow from $14.5 million in 2005 to $62 million in 2012, according to a recent Frost & Sullivan study. The company also looked at the European market and forecast that spending on aerospace-related RFID there would rise from $2.9 million in 2005 to $12.1 million by 2012.Manufacturers Entice Partners
Boeing conducted the RFID demonstration in Tokyo because the company is trying to encourage its supply-chain partners—both airlines and suppliers—to adopt the technology by illustrating what’s in it for them. “The biggest challenge is successfully communicating the value proposition,” says Boeing’s Phil Coop, manager of the 787 RFID Service Ready project, also known as the Dreamliner, for which Boeing is attempting to have 2,000 parts RFID-tagged by suppliers.
Airlines stand to benefit from dramatic cuts in labor required for some routine maintenance, greater turnaround in service schedules and a reduction in spare-parts inventory. “You have lots of capital tied up in inventory,” says Victor Prodonoff Jr., director of the Aerospace ID Technologies Program at the Auto-ID Lab at the University of Cambridge. “Anything you can do to reduce that inventory frees up a lot of cash.”
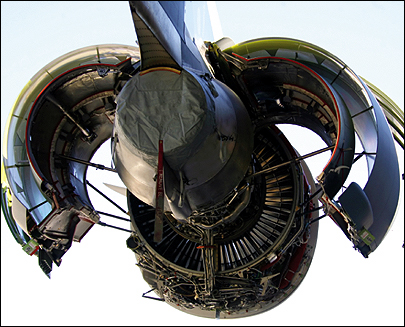
There is a value proposition for suppliers as well. Rivals Boeing and Airbus share an estimated 70 percent of suppliers in a complicated international supply chain that requires approximately 6 million parts for each airplane, according to ABI Research. Suppliers would prefer to see one coordinated standard for parts marking, rather than rival standards being adopted by different manufacturers. It’s also more efficient to have the maintenance history contained on the part rather than scattered across dozens of databases at several airlines or MRO facilities around the world.
“If the [supplier] repairs the part for the airline, it will get some direct feedback from the mechanic who took it off the airplane and get valuable data—’it was hot’—that it is not getting now,” says Jon Andresen, a former United Airlines executive who founded the Technology Solutions consulting firm and works with Boeing on RFID. “This information will help them to troubleshoot and/or design a better part.”
Rockwell Collins, an aerospace supplier, has become involved in the creation of data standards because it “sees a benefit in receiving a summary of maintenance and material-related events with their products when they return from years of service,” says Boeing’s Coop. Information about how parts wear could help the company build more resilient parts in the future.
RFID parts tracking could also help combat the 2 percent of all replacement parts that are counterfeit, according to estimates from the U.S. Federal Aviation Administration (FAA). Suppliers lose income when counterfeit products enter the supply chain, and inferior quality aircraft parts could jeopardize passengers and cargo. RFID could provide a data pedigree attesting to each part’s origin. In addition, RFID has the potential to track safety data required by agencies such as the FAA, the European Joint Aviation Authorities and Japan’s Civil Aviation Bureau.
The industry has tracked airplane parts using bar codes for years through an initiative promoted by the Air Transport Association (ATA) called Spec2000, but RFID has the potential to make that data more accurate and easier to collect. “One of the biggest problems we have now is with the reliability of data, essentially caused by typos,” Andresen says.
“We certainly are seeing a desire to track parts from manufacture all the way to receipt and on to final assembly on an airplane, but it’s equally as important to track parts for maintenance,” says Sue Hutchinson, director of industry adoption for EPCglobal, the standards body that has a working group on aerospace issues. “A host of regularly scheduled maintenance operations are done daily, done weekly, done monthly or after a set number of service visits. For each of those checks—or should something mechanically fail—you need to know you’ve got not only the appropriate part available, but that the part has been maintained and stored properly.”
To that end, Boeing is asking—not mandating—suppliers to RFID-tag some 2,000 parts that will be used in each of its upcoming Dreamliner passenger planes (see “Boeing’s RFID Plan: The Sky’s the Limit,” November/December 2006). The goal is to use RFID to track a part’s maintenance history throughout its life cycle. Boeing has already won approval from the FAA for the use of passive tags in flight. The company, which recently tested the use of active (battery-operated) RFID tags in cargo planes and found that the tags didn’t interfere with the operation of the aircraft, is waiting for the FAA to rule on whether active tags can be used onboard civil aircraft.
Boeing plans to give its suppliers (and customers) the software necessary to initialize and maintain data on the RFID tags. “Some of the 787 suppliers are very enthusiastic while others are less so,” says Coop. Boeing conducted informational forums last year in Japan, Germany and North America, which were designed to provide suppliers with implementation details, standards and possible ROI for their businesses.
Some aerospace suppliers—including Rockwell Collins and Honeywell—have been working to meet RFID tagging requests from both airplane manufacturers and the DOD. But while Boeing is interested in having certain suppliers RFID-tag individual parts, the DOD requirements have been quite different. Since 2005, the DOD has been contracting with a growing number of suppliers—including some in the aerospace field—to provide goods in RFID-tagged cases and pallets. The tagging requirements include the use of UHF RFID tags based on Electronic Product Code specifications.Suppliers Seek Internal Benefits
Some suppliers that became familiar with RFID through tagging initiatives have found their own uses for the technology in-house. Lockheed Martin, the giant defense contractor, is compliant with DOD RFID mandates for select suppliers and also tracks parts internally at several locations.
The company doesn’t require suppliers to tag deliveries, but once parts reach Lockheed Martin, it tags items and tracks them from receiving into inventory and through production, according to Denton Clark, the company’s auto-ID technology manager. Lockheed Martin has also been tracking IT assets, such as notebook computers, around facilities. But with more than 900 facilities worldwide—some, such as the Fort Worth, Texas, location, encompass more than 5 million square feet—one of the problems the company has encountered is the cost of infrastructure.
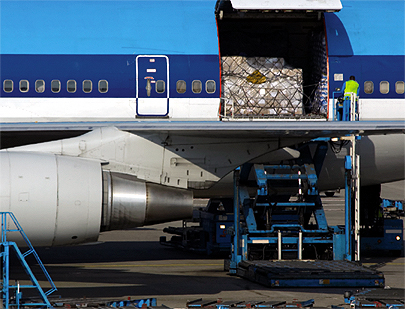
The Nordam Group, which is tagging window frames and other parts for Boeing’s Dreamliner and has contracts with the military, found its most successful use of RFID was in tracking tools within the company. Nordam has 900 molds used to make the fiberglass shell interiors of business jets. “Every morning, 50 people would show up for work and would have to go into the back room and go find the tool for their part,” says Michael Metcalf, Nordam’s program manager. That tied up each worker for 10 to 40 minutes. Last year, Nordam started applying passive RFID tags to those molds, making them easy to identify. RFID allows the company to “spend more time producing parts than searching for tools,” Metcalf says.
Unlike some industries with lower margins, some aerospace companies don’t mind the cost of RFID tags. Nordam is using tags that cost $100 apiece, but they are placed on tools that range in cost from $10,000 to $40,000 each.
Airlines and Airports Track Assets and People
Several airlines have been experimenting with closed-loop RFID systems to track valuable equipment. Air France-KLM started tagging unit load devices (ULDs)—the large containers that are filled with baggage and cargo and loaded onto planes. The pilot involves 100 of its fleet of more than 6,000 ULDs in use at Paris-Charles de Gaulle Airport. It was designed not only to track the ULDs around the airport but also to provide airline management with visibility into the loading and unloading processes.
American Airlines has conducted several pilots, including tools tracking for mechanics and a cargo-tracking initiative in conjunction with the U.S. Transportation Security Administration. American hasn’t yet decided to implement any of those solutions. “We’re kind of in a state of cautious study,” says Joyce Polkinghorne, a senior business technology analyst at American Airlines who chairs the ATA’s RFID Working Group.
One application that Polkinghorne says the company is considering on a more widespread basis involves the tracking of chemicals used in the repair process. The carrier has a patent pending for a secure chemical cabinet RFID application. Each item in the cabinet—solvents, adhesives and other materials—is issued an RFID tag containing such data as shelf life and disposal instructions. The system could make it easier for the airline to track the chemicals and know when to replenish supplies.
Manchester Airport, in the United Kingdom, has tested RFID to track passengers through security checks. The goal is to speed up that process so people can spend more time—and hopefully more money—in the airport’s retail area.
There’s also some interest in tracking travelers through the airport to reduce flight delays, providing privacy concerns can be addressed. In January, a consortium of European companies and University College London (UCL) tracked people inside a Hungarian airport with active 5.8 GHz RFID tags worn on cords around their necks. Paul Brennan, a professor of electronic and electrical engineering at UCL who coordinated the pilot, says that the use of this technology for passengers who have received their boarding cards could improve air travel security, help evacuate people in the event of an emergency and help reduce flight delays. “It’s possible to detect when people are a long way from the gate at the time they should be boarding,” Brennan says, “and it makes it easier to get those people to the slots and avoid delays.”The Flight Path Ahead
The lack of availability of the right technology and the development of data sharing and air-interface standards are slowing some RFID pilots and deployments. Technology providers have been focused on supplying low-memory passive tags for case and pallet tagging in the retail industry. The type of parts marking envisioned by Boeing requires higher-memory tags. Boeing has focused on a 64-kilobit chip from Intelleflex that can both lock in pedigree information about a part (such as country of origin, manufacturer and serial number) and provide read-write capabilities so that mechanics in Frankfurt can record maintenance notes on a tag that can be called up in New York the next time the plane is serviced. Some suppliers are holding off on pilots until the supply of those tags better meets demand.
The aerospace industry also requires RFID tags that can last a dozen years, endure extreme temperatures and perform in an environment with a high concentration of metals, which can interfere with RF readings. That requires more testing for various RFID applications and the development of RFID tags that are different from the tags being mass-produced today for retail applications.
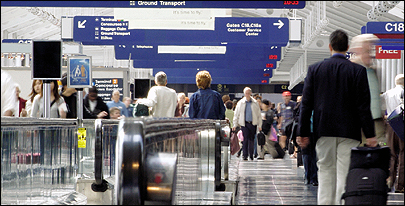
Parts suppliers currently face very different RFID requirements from Boeing and the DOD—and the suppliers are forced to bear the costs of the technology. The DOD has expressed interest in the Boeing RFID parts-marking project and has requested briefings from the company, raising the possibility that in the future suppliers would not have to meet two very different tagging mandates. While some suppliers have embraced RFID, others see the technology as an added cost burden and will need to look for internal uses, which will require significant changes in their business processes.
The aerospace industry also needs to synchronize on data collection and data sharing between supply-chain partners. “Data is the thing that’s going to save our business,” says Technology Solutions’ Andresen, “not technology.” Prodonoff, of the Aerospace ID Program, has been working with Afilias, a name registry services company, to develop a look-up service for parts in aerospace—what he calls a “Google for parts.” Before such systems can work, the industry needs to shift from decades of legacy systems and paper-based business processes to electronic data exchanges. These issues are still in discussion by industry groups.
The future promise of RFID is one that excites many aerospace leaders. RFID, in combination with sensors, could potentially be used in flight to communicate component or engine problems to not only flight crews but also maintenance workers at the destination airport so they could locate a duplicate part and prepare to replace it once the plane lands.
But change may not come overnight. “I think a 10-year horizon is a good one,” says EPCglobal’s Hutchinson. “That’s what we’re looking at in terms of the replacement life cycle for a lot of the equipment already in use. We’re going to start to see this coming in with the next cycle of airframes and as the next cycle of replacement parts makes its way into the bloodstream.”Found: A Solution to Lost Luggage
The U.S. Bureau of Transportation Statistics released some figures in February that would cause any air traveler alarm: U.S. airlines mishandled some four million bags in 2006, nearly 6.7 suitcases for every 1,000 passengers. It marked the industry’s worst performance since 1990. To stem the tide of customer complaints and comply with increasingly stringent security regulations, airlines and airports are using RFID to track luggage from check-in to the traveler’s destination.
In the past few years, there have been roughly two-dozen baggage-tracking pilots and deployments around the world, according to the International Air Transport Association. Starting with a pilot to track bags at Heathrow Airport in 1999, the interest in RFID for this purpose has grown. Hong Kong International Airport—one of the busiest airports in the world—started implementing an RFID baggage-tracking solution in 2005, and last fall, Air France-KLM began tracking bags between Paris-Charles de Gaulle and Amsterdam’s Schiphol airports. Other pilots have been joint projects conducted by airlines and government regulators, such as the U.S. Transportation Security Administration, and have included tracking bags through multi-destination international routes.
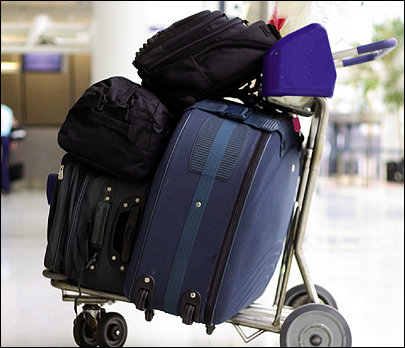
McCarran International Airport in Las Vegas started tracking all bags for all airlines on flights departing from the airport. McCarran now RFID-tags 20,000 to 40,000 checked bags per day. “We track every bag from the time a passenger checks it in, to the time it gets delivered to the carousel to when it is delivered to the aircraft,” says William Gibbs, senior mechanical engineer for Swanson Rink, which designed the RFID system used to track luggage at McCarran. The RFID system has an accuracy rate of 99.5 percent in reading bags, but statistics on improvements of lost luggage are unavailable because airlines previously handled their own baggage operations at the airport.
While the pilots demonstrate that RFID can be used successfully to track luggage, some airports and airlines question whether RFID is an affordable solution. Tags cost about 25 cents each, on top of the cost of installing the RFID infrastructure needed to track millions of bags per year. But some airport operators and airlines are beginning to see that the data gained through RFID tracking could provide enough insight into their business processes beyond just tracking luggage to enable them to achieve a return on investment.
Some airport management companies operate the baggage franchise themselves; at other airports, individual airlines each take care of the luggage on their own flights. Many believe that RFID tracking won’t be fully efficient unless all the players in airports around the world use the same technology.
“At this time, it’s still kind of in the early stages,” says Rob Foppiani, an analyst with ABI Research, who wrote a recent report on RFID baggage tracking. He predicts the market for RFID in baggage handling will grow from $11.8 million in 2006 to $27.5 million in 2011.
Illustration by Gordon Studer