Timber used to be harvested by clear-cutting trees in a forest until environmentalists called attention to the potential ecological damage to wildlife and the impact of deforestation on global warming. That ushered in a movement in the 1990s toward more environmentally sound logging, and over the years, some timber companies have committed to planting seedlings in equal or greater numbers to the trees they fell. Now, radio frequency identification has the potential not only to support sustainable forest management but also to provide visibility into the timber supply chain. The technology can be used to identify each tree and track it from forest to sawmill and onto its manufacture into wood products, which can reduce waste of a vital natural resource.
Unlike many industries that have gained efficiencies and cost savings from information technology, the forestry industry has been left largely in the woods. “How can you track a tree with a bar code, unless you tattoo [the code] or burn it into the tree?” says Michael Liard, RFID practice director for ABI Research. That’s changed in the past few years, with development of specialized RFID tags that can be embedded into trees, manually or by machine. Some of these tags are made of biodegradable materials, so they can be ground with wood products to make pulp and paper.
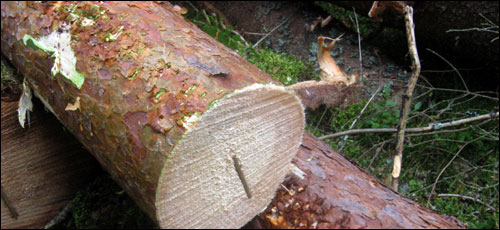
“The forestry industry hasn’t had to think about automatic identification until now that we have tags that can be embedded into trees,” Liard says. “RFID can bring value by tracking timber through the whole logging operation, through shipment, monitoring for deliveries and such.”
In pilots and deployments worldwide, governments, research institutes, forestry and sawmill companies, and wood products manufacturers are employing RFID to optimize forest production and improve the quality of wood products, as well as to minimize environmental damage and enable companies to comply with U.S. and European rules barring import of illegal or endangered timber products. But before RFID-tagging becomes common practice in the forestry industry, tag prices must come down and more solid business cases must be demonstrated. Meanwhile, RFID shows promise as a tool to help control wildfires.
Planting Visibility
A 2002 study of total sawn wood production in Europe found that each year, an estimated 25 million cubic meters (883 million cubic feet) of raw material, worth some €5 billion ($6.6 billion), goes to waste. Improving production, thus minimizing environmental damage, was the impetus behind Indisputable Key—a three-year, European Commission-funded research project completed in 2010, involving businesses and researchers in Estonia, Finland, France, Norway and Sweden. The project included a number of studies that used RFID to bring visibility to the forestry supply chain.
Overall, Indisputable Key found that individually identifying felled logs with ultrahigh-frequency RFID transponders and tracking them through the supply chain leads to myriad environmental and economic benefits. RFID can reduce waste by improving the use of raw materials and the efficiency of timber-production processes. Information about the wood can be gathered and made available throughout the supply chain. “Wood is a natural product, but by using RFID, we can learn what to really make of a certain kind of species or quality of wood,” says Ville Puntanen, a service development manager at Tieto, a Finnish IT service provider that developed traceability solutions for Indisputable Key pilots. “Timber companies will learn more about their supply chain from using RFID, and get the quality information they haven’t been able to get before.”
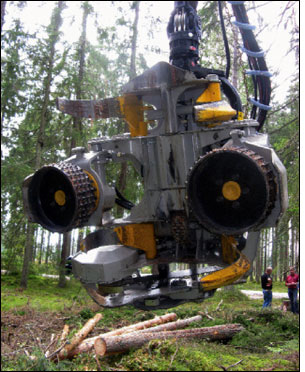
A Swedish forestry and wood supply-chain study, for example, found that identifying logs with RFID tags could help manufacturers determine which woods to purchase for their products. Every forest tree is unique—no two trees have the same knots, moisture level or trunk thickness. Some may be best suited for telephone poles, others for fine wood flooring and still others for pulp. And some wood manufacturers will pay premium prices for certain qualities, such as hardness, durability, size and color.
The study involved marking logs after they were harvested with biodegradable UHF Gen 2 RFID tags from Confidex, using either an automatic or manual applicator. Information about each log—including length, diameter, curvature, place of origin and harvest date—was tied in a database to the unique RFID tag number, and the tags were read at various points as they were sorted into groups and transported to sawmills and on to secondary manufacturers. The RFID solution was developed by VTT, and participants included Sveaskog, the largest forest owner in Sweden, and the Setra Group’s Malå sawmill.
“The main reason we did this is we need to have feedback in order to make a better product,” says Richard Uusijärvi, project coordinator from the SP Technical Research Institute of Sweden. “This allows us to pick the better tree for certain products.” The team had tried other methods of identification, including stamping a mark on logs and printing codes during cross-cut sawing, Uusijärvi says, but RFID was preferable because it was the only way to record data from each of the world’s almost innumerable logs and tie that information to wood products as they traveled throughout the supply chain.
RFID also could be used to optimize logistics processes when it’s not cost-effective to tag individual logs. The Fraunhofer Institute for Factory Operation and Automation IFF, in Magdeburg, Germany, has undertaken a government-funded project that started in 2008 and continues through February 2011, to track shipments of logs for the production of pulp, paper and fiberboard. The pilot is using a newly developed RFID transponder made of paper and lignin (a part of plant cells) that can be processed along with wood into pulp without contaminating the final product. That saves the time and money it would take to extract tags made of plastic or metal. The paper-pulp industry has low margins, and it would be cost-prohibitive to RFID-tag each tree, says trial coordinator Mike Wäsche. But by tagging every 10 or 20 logs in a shipment, the location and timing of timber supplies and shipments could be tracked by supply-chain partners, and invoicing processes could be automated and expedited.
Promoting Sustainable Forestry
Forests cover nearly a third of Earth’s land area, but each year, an estimated 13 million hectares (32 million acres) of forest are harvested, destroyed by arson fires or natural causes, or converted to agricultural use in developing nations, according to the United Nations. Wood from these forests becomes more precious and valuable each day. That’s one reason global efforts are under way to use RFID to provide track-and-trace visibility that can help reduce illegal logging and ease compliance with European and U.S. laws requiring validation that imported wood products are from sustainable timber sources.
Up to 40 percent of wood products entering European and U.S. markets may consist of illegally harvested products, including mahogany, ramin and teak. In 2008, the United States banned imports of plants or timber products that were illegally taken or traded, and now requires importers to declare the species and country of origin. The United States is also pushing developing nations to crack down on illegal logging through free-trade agreements. Peru, for example, recently signed a treaty pledging to develop a system to track endangered tree species from harvesting through transport, processing and export. The European Union, meanwhile, adopted the Forest Law Enforcement, Governance and Trade (FLEGT) plan to address illegal logging by seeking voluntary certifications on timber products imported from Ghana, Indonesia, the Republic of Congo and other trading partners. The E.U. has set a 2016 deadline for all countries to certify their timber products are legal.
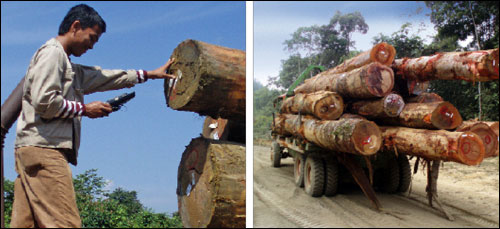
To comply with these rules, Bolivia, Malaysia, Peru and other developing nations are seeking ways to verify the legality of timber. Some of these countries are getting their feet wet with bar-code tracking of trees and logs, but RFID has more potential because tags can withstand rugged forest conditions, and they can be read automatically, without line of site.
“We’re dealing with a sector that’s just catching up with computing,” says Patrick Newton, CEO of Helveta, an Oxford, U.K.-based software maker that has developed a timber-tracking product that uses data gleaned from RFID-tag or bar-code readings. “Primarily, they’ve been using paper-based systems supported by physical audits. Where we have come into the contest is to help replace the legacy of paper and inefficient paper-based auditing and move to more of a computer-driven mode of verification.”
Malaysia is one of the world’s largest timber exporters. In 2009, the Forestry Department of Peninsular Malaysia (FDPM) undertook an RFID trial to staple or nail UHF Gen 2 tags to 242 trees on a 319-acre swath in Terengganu state and track the 62 trees that were felled, processed into logs and transported. FDPM used Helveta’s CI World platform as a central database to host the data, and reports based on the information gathered were made available online to stakeholders, providing visibility on the flow of wood and wood products moving through the supply chain.
Now, Helveta officials are working with the Malaysian government to design an RFID implementation to track and protect trees in the ramin forests. Ramin refers to about 30 species of tropical Asian hardwood that is used for a variety of products, from picture frames to billiard cues. The ramin forests are the main habitat for endangered animal species, such as orangutans and Malayan tigers.
Breeding a Healthier Crop of Trees
In Hawaii, the only U.S. state capable of growing a wide variety of tropical rainforest hardwoods, hundreds of thousands of acres of forest have been cleared for sugar cane and pineapple fields over the past century. Hawaiian Legacy Hardwoods (HLH) has been trying to replenish stocks of the indigenous koa tree by using UHF RFID tags from Confidex that are planted alongside saplings, to track the trees’ care and eventual harvesting. On 2,700 acres on Mauna Kea, an inactive volcano on the island of Hawaii, the company is planting trees and recording data about each tree, such as lineage—from which “mother” tree the seed originated—to try to ensure healthier trees.
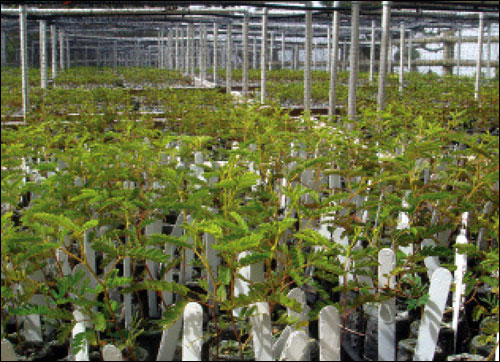
While the koa isn’t listed as an endangered species, 90 percent of the native Hawaiian tree has been harvested. The remaining trees are harvested through a process known as “koa mining,” and there is very little replanting on the islands, according to Jeff Dunster, CEO of HLH.
The company plants trees for both investors (companies that plan to harvest the hardwood eventually) and ecosystem restorers (folks concerned about reforestation and species preservation). For $60 per sapling, HLH will plant a koa and nurture the tree for the next 50 years, marking it with RFID and GPS coordinates so people can look up the location on Google Earth and can even visit the tree, Dunster says.
In addition to the charitable cause, HLH is using RFID to monitor the lineage of the trees and track growth rates. “We may have a group of trees that have been in the ground 10 months, and some will be 2 feet tall and as big in diameter as a pencil, and some may be 5 feet tall and have the diameter of a silver dollar,” Dunster says. “That tag will lead us to information about where the mother tree is located, and we can use that information to fight disease and promote stronger growth.”
Seeing the Forest Through the Trees
The early successes using RFID in the forest ultimately may allow the timber industry to track this natural resource from sapling to sawmill, on to its manufacture into wood products and back to the source. But first, the RFID industry must develop business use cases that make the technology more economical for the forestry industry and developing countries.
There are business benefits to RFID in the forestry supply chain, such as analyzing data about performance of wood products to determine which type of trees are best for, say, ceiling beams or window frames. But the price of RFID tags must come down in order for companies to invest. “It’s still a price issue,” says Uusijärvi, of the Indisputable Key project. “There needs to be some kind of push and also further development before this happens on a bigger scale.”
The key to encouraging RFID timber tracking in developing countries is creating ways to leverage the data to minimize costs, maximize production and deliver a return on investment. One potential source of ROI is use of RFID to track trees and forests for validation information to apply for carbon offset credits, which allow reduction of emissions of carbon or greenhouse gases to be monetized on a growing number of international carbon-trading markets, says Helveta’s Newton.
Consumers also may play a role in encouraging the use of RFID to prevent illegal logging and help maintain the biodiversity of our ecosystem. “We can provide consumers with more information about the life cycle of the product they’re buying—for example, chain of custody and the origin of the wood,” says Tieto’s Puntanen. “We believe they will buy more wood products when they know more about it and see how sustainable wood products really are.”
Where There’s Smoke, Firefighters Want RFID
Flames fueled by high winds and dry brush spread quickly in the forested areas of Southern California, and it takes one hour on average for most fires to be reported. But a pilot conducted last July in Castaic, a rural part of Los Angeles County, found that using RFID-enabled sensors can allow news of a blaze to spread faster than wildfire.
For the trial, 15 RFID-enabled heat sensors, which communicate their locations over a wireless network, were placed throughout a two-acre area. Representatives of the U.S. Forest Service, the agency’s San Dimas Technology Development Center and the Los Angeles County Fire Department set a controlled burn to see how quickly the sensors would alert firefighters. The fire was reported in minutes.
“The sensors were deployed at 50-yard intervals throughout the test area, and they lit the test fire about 50 yards from the first sensor,” says Brent Chapel, former CEO of ProximaRF, which provided the ProxFire Detection System. “It took about four minutes for the fire to burn up to the sensor and set it off.” The sensors go off when the temperature reaches 170 degrees Fahrenheit (77 degrees Celsius).
“If you get to the fire in an hour, you’re probably only going to have $80,000 worth of damage,” Chapel says. “The problem is, if it gets past an hour, then the fire is normally a wildfire and it’s out of control; even with a lot of resources to put it out, it’s still likely to go on for five or six hours.” A six-hour burn, he says, can cost more than $2 million.
Interest in RFID-sensor networks is growing in fire-prone areas, says Chapel, who has founded IntelliRF Systems Holding, which is working with IT logistics firm Naniq Systems to develop a solution for the U.S. Forest Service in the Big Bear Lake region of the San Bernardino Mountains. In 2007, a fast-moving forest fire near Big Bear Lake scorched more than 18,000 acres and forced some 500 residents to evacuate. The previous year, five members of the Alandale Forest Fire Station perished in the nearby Esperanza Fire, a wind-fueled arson fire that devastated 40,000 acres before firefighters contained it.
Homeowners associations in Southern California regions plagued by blazes are discussing privately financing an RFID early-warning system, Chapel says. The cost to install 200,000 sensors over a 100-square-mile region is about $3 million, he adds.
IntelliRF Systems plans to test a sensor encased in a carbon shell designed to withstand high temperatures and continue reporting, as opposed to the current paper-covered sensors, which burn in a fire’s flames. “The concept we have today is that the sensors warn of the fire and burn out,” Chapel says. “The new sensors will warn about the fire, but stay in the fire and transmit information concerning wind speed and flame height.” Firefighters could use the data to better understand the characteristics of a blaze, so they could mobilize their resources to put it out faster.