The integration of different systems into a common IT or automation architecture can become a complicated task, because a variety of different interfaces and protocols exist in practice. RFID readers are no exception. But how must a communication architecture look that networks tens of thousands of devices in the digital factory? Industrial communication and the OPC Unified Architecture are the key elements of the necessary digital infrastructure.
The changes are obvious when taking a closer look at the application scenarios in the digital factory. These use cases can be divided into three areas (see Figure 1). The end-to-end engineering means that the data from the product design can also be utilized for the production engineering—to derive control programs, for instance. This allows different perspectives on a product to be recorded and developed in a standardized data model, which simplifies changes, helps to avoid serrors and significantly reduces engineering times, including the time to production launch.
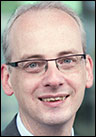
Flexible automation is aiming to resolve the apparent contradiction between flexibility and automation, so that a variety of different products can be produced by the same plant. New production processes, such as 3D printing, belong to this area. Finally, the collection and integration of data throughout the entire product lifecycle make possible new services—for example, for maintenance purposes.
The objective is to create a digital image of all relevant objects—and “relevant” is everything that needs to be tracked, checked, found or monitored—from the simple pallet to the actual product produced by the factory. In the Industrial Internet of Things (IIoT), ideally all objects with communication capabilities are thus integrated into a network. For this, however, RFID systems are indispensable—they synchronize the digital images in the IT systems with the objects in the factory and warehouse: Not every “thing” will have WLAN or Ethernet, but via RFID, a digital capture with location, time and identity is possible.

The digital factory pushes the vertical (that is, between components on the same level) and horizontal integration (communication between layers) of the communication levels. In the digital factory, the previously rigid cellular organization of a production is thus broken up (for example, through freely moving, autonomous robots). The integration of data as information source for analytical, data-based services then leads to a break-up of the horizontal layers. For example, to gain new insights for predictive maintenance, a high data density is necessary, which starts with the design and engineering, and includes quality data in the production, as well as sensors that—when using a machine—transmit their measured values to the IT systems (the cloud).
The communication infrastructure establishing the basis for the architecture outlined must satisfy a wide range of requirements. On the one hand, characteristics such as the use of open standards, availability, quality of service and, above all, security are demanded, which already distinguish today’s Industrial Ethernet networks. On the other hand, the connection to IT systems for data-based services, or for an increased transparency across all levels, is demanded—requiring a link between office and production networks.
Safeguards ensure the functioning in the industrial network, but still permit access to all layers, devices and components. As a network topology, different aggregation stages and the introduction of a factory backbone thus present themselves (see Figure 2 on page 2), which enable fast communication between the devices in the individual cells, as well as the efficient linking of the office network and the various sub-areas.
In order to meet the objectives and requirements of the digital factory, however, an end-to-end network topology is not enough. Required is a communication protocol that is open and standardized, provides sufficient semantic information and translation options, is easy to expand and maintain, offers maximum security in various forms, and also has low memory and processing requirements to allow implementation on small devices.
The answer to these requirements is the OPC Unified Architecture (OPC UA). The most important thing about the OPC UA is that it is not only a protocol, but a complete architecture that, in addition to the transmission definition, also provides suitable software stacks for device and software makers, as well as engineering tools for system integrators. The OPC UA thus brings important advantages. To begin with, the information model ensures that all data is transmitted on a type-safe basis. Even complex data types (structures) are possible.
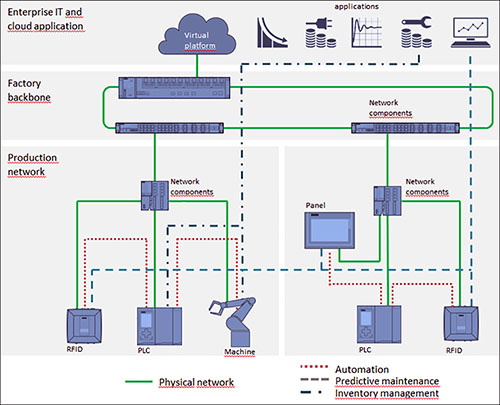
Besides the pure data values, the OPC UA also transports semantic information between communication partners. Since the architecture works object-oriented, the semantics are always interwoven into an object context—it consists of more than just a “speaking” identifier and always refers to the entire object with its properties and methods. Function calls over the network allow a certain control of the communication partner. Events are supported as ad-hoc communication or as message brokers for the connection to the cloud. The security of the system is likewise guaranteed by suitable mechanisms.
For the specific use in different applications, various industrial associations work with the OPC Foundation on so-called “Companion Specifications,” which supplement the basic specification of the OPC UA for a particular domain. One example is the AutoID Companion Specification, which was developed jointly by the RFID industrial association AIM and the OPC Foundation. This allows systems for the automatic identification, such as 2D code readers or RFID devices, to be embedded in modern communication architectures by means of the OPC UA. For users, the OPC UA makes it possible to employ devices from different manufacturers according to individual requirements.
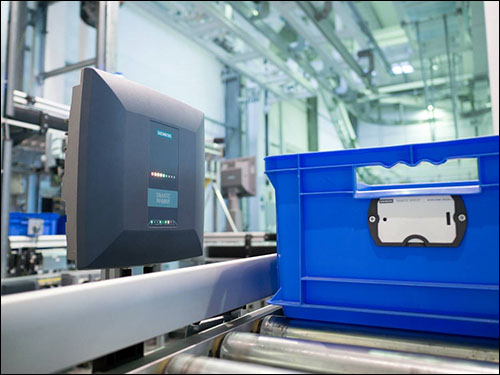
In addition, different identification technologies can be integrated in the same way. The importance of the OPC UA, though, goes far beyond this, because now RFID systems can be integrated, as well as different controllers, field devices, IT systems and much more. Different target systems (automation systems for the control of the field level, big-data applications for the information analysis in the cloud), too, can be operated similarly (see Figure 3).
However, until the OPC UA can be widely used as an end-to-end communication architecture, further standardization work is necessary, as some areas of the industrial communication are not yet fully covered. For instance, at the sensor level, only a few device families or technologies have been specified for OPC UA—RFID and auto-ID systems are among the pioneers. But aside from these future tasks, the OPC UA already represents a communication architecture that is unique in its range of functions, and will be indispensable as the basis for the vertical and horizontal integration in the digital factory.
Markus Weinländer is the head of product management for SIMATIC Net at Siemens AG. He previously managed marketing for RFID across all parts of the company, and held various research and development positions. During his career, Markus acquired considerable experience in software engineering and the architecture of automation systems. He studied business economics in Hamburg and Wismar, received a Master of Science degree, and obtained his technical background as an associate engineer at Siemens Technik Akademie in Erlangen, in the special field of data and automation technology.