As I write this column, we at RFID Journal are making final arrangements for our RFID in Energy, Mining and Construction event, and I’m preparing for the long trip to Perth, Australia. The conference and exhibition will feature case studies by Bechtel, Petrobras, Weatherford, Woodside and other companies. This will be followed by an RFID standards workshop hosted by the Global RFID Committee for Oil & Gas.
The event will show that the energy and construction sectors are beginning to get serious about the adoption of radio frequency identification technologies. Large construction projects are mind-numbingly complex, with materials needing to show up at a job site in precise sequence. At RFID Journal LIVE! 2014, held in April, Bechtel was a co-winner of the RFID Journal Award for Best Implementation, for the project that the company will present at the event (see RFID Helps Bechtel Manage a Megaproject).
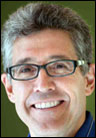
Bechtel is using RFID technology to track materials as they move through a complex local supply chain to arrive on Curtis Island, off the coast of Queensland, Australia, where three liquified natural gas (LNG) plants are being built. An active RFID system has helped Bechtel shorten cycle times, reduce costs and achieve transactional benefits during material-handling activities.
The three LNG projects sit side by side, with three separate owners, and all construction materials for these projects must be loaded onto transport ferries and moved across a harbor before reaching their intended final installation location. The RFID system helped the company track all the materials and kept the production on schedule. It’s a massive project, and it showed how RFID could help companies manage such large-scale undertakings.
This year, BP was a runner-up for the RFID Journal Award for Best Implementation, for a $10 billion project in which it tracked every component that it shipped from its European warehouses to South Korea for the construction of a giant oil rig, using RFID and GPS technologies (see RFID, GPS Bring Visibility to Construction of BP Oil Platform). BP has been buying components from suppliers around the world, which are shipped to one of two consolidation centers in Europe. The parts are tagged and are then shipped to BP’s warehouse near the manufacturing site in South Korea, for staging until each part is required for construction. The components amount to billions of dollars’ worth of equipment from hundreds of vendors, and BP wanted to ensure that materials were delivered as needed, on time, to Hyundai Heavy Industries (HHI), the company building the top side of the platform.
In the past, I have heard oil industry executives say that saving a few million dollars annually is not worth the effort of deploying RFID—not when a firm can make billions per quarter. But I think that attitude is changing. First, profits have been under some pressure. Income for the big five oil producers fell by 27 percent last year, from 2012. More important, industry executives are beginning to understand that RFID can help companies manage complex projects, improve safety (see BP Refinery Uses RFID for Evacuation System), manage the inspection of pipes and other components (see BP Uses RFID Sensors to Track Pipe Corrosion) and even manage the closing of plants for regular maintenance.
The standards workshop is an important first step toward harmonizing the use of RFID across the industry. If one company is using ultrahigh-frequency (UHF) RFID tags to track drill pipes and another is using high-frequency (HF) tags, then companies making or supplying drill pipes will need to manage the complex process of installing one type of technology for one company and another type for a different customer, and oil services firms will need to support both types of RFID technology to service clients. The industry now recognizes that agreeing on which technologies to use for specific components or particular applications will enhance efficiencies and lower costs for everyone.
Widespread adoption in the energy sector will not occur overnight. It will take time for companies to agree on ways to use RFID upstream, mid-stream and downstream. RFID companies will need to introduce more intrinsically safe products—something they have been reluctant to do because the demand was not great enough to justify the cost of getting products certified—and use cases will need to be solidified. But those things are happening, and oil and gas companies now seem energized about using RFID.
Mark Roberti is the founder and editor of RFID Journal. If you would like to comment on this article, click on the link below. To read more of Mark’s opinions, visit the RFID Journal Blog, the Editor’s Note archive or RFID Connect.