One question I am frequently asked when I speak about radio frequency identification is this: “If there are 100 tagged items in an area, how do I know I have read them all with RFID?” The answer, of course, is “You don’t.” But I always ask the questioner—typically someone who has not used an RFID system before and, therefore, has questions about its reliability and accuracy—”How do you know that a person has manually counted all 100 items correctly? The answer is, you don’t.”
The truth is that manual counts of a large number of items are always wrong. Time and motion studies conducted by the University of Arkansas‘ RFID Research Center (which has since been moved to Auburn University and is now called the RFID Lab), found that a manual inventory count of a large retail store was only 85 percent accurate. Worse, accuracy begins to degrade immediately and, within a few weeks, falls to roughly 65 percent accurate.
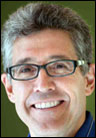
Yet, many retailers believe their inventory systems are 95 percent or 97 percent accurate. Dr. Bill Hardgrave, the dean of Auburn University’s Harbert College of Business and the head of the RFID Lab, says retailers often look at inventory in the aggregate. “If a retailer’s system says there are 12,000 items in stock and they count 11,500, they believe they are 96 percent accurate,” he says. “But that’s wrong.” The system, for example, might say a store has five green paisley ties and five red paisley ties when, in fact, there are 10 red paisley ties and no green ties, he explains.
Other industries have similar issues. I’ve spoken to CEOs of large manufacturing companies who say their warehouse inventory accuracy is 99 percent. That’s doubtful. There is a saying among warehouse guys: “Don’t trust SAP.” This doesn’t mean don’t trust the software company, but rather whatever the inventory system (often SAP) tells you is often wrong. Moreover, if employees can’t find items they need to pick to ship to customers, then it doesn’t matter that your system says you have those products in the warehouse. Additionally, if you are carrying extra stock to ensure that workers can find the items, you are tying up capital that could be better used elsewhere to grow your business.
Given that inventory systems are woefully inaccurate, it’s curious that so many people obsess over the fact that one tagged item might not be captured out of 100. It seems businesspeople trust their current system even though it is wrong, while distrusting RFID solutions because they’re new and unproven. But companies have begun to address this concern.
I’ve heard of a number of retailers that turned off RFID systems after running a pilot and measured the change in key performance indicators (KPIs). Since manual counts are so inaccurate, it’s not useful to take inventory manually and then with RFID. In addition, if not all items are tagged in the store properly (some goods will inevitably not have tags, while others will have two or even three tags), it’s impossible to compare the manual counts to RFID results.
To obtain a more realistic picture of the accuracy of their RFID data, some retailers now carry out a pilot and perform inventory counts daily so they can measure replenishment. They measure the on-shelf availability of certain items or all items (depending on whether they are tagging all departments). And they measure shrinkage (employee theft and shoplifting) and other key metrics. Then, by turning off the system, they can measure how these KPIs degraded without RFID after a few months.
I’ve also heard of manufacturers who tell staff members to manually count items every day in order to satisfy some managers who question whether the RFID system is accurate. Invariably, the employees come back after a few days and say there’s no point in doing this daily since the RFID solution is always accurate.
Some hospitals use their real-time location system (RTLS) for several months before providing personnel with access to the system. The idea is to get benchmark data regarding the asset-utilization rates for mobile medical equipment. (I wish there were a way to track employees to determine how much time they spend searching for equipment.) To my knowledge, no hospital has published any results yet, perhaps because asset-utilization rates are so low. But when they turn on the system, they can show workers that it accurately monitors the locations of assets, and can thus put credible numbers behind their claims that the RTLS improves inventory accuracy.
This is not to say RFID systems are prefect. No technology is perfect. But a solution that is installed and configured properly usually provides highly accurate and reliable data. And at some point, everyone will trust the technology enough to believe in the information it provides. But right now, it’s good to see businesses building credibility for the technology by showing the data is highly accurate.
Mark Roberti is the founder and editor of RFID Journal. If you would like to comment on this article, click on the link below. To read more of Mark’s opinions, visit the RFID Journal Blog, the Editor’s Note archive or RFID Connect.