Mike Nicometo is a cool guy. He has to be. As global information systems director of Cool Chain Group, a third-party logistics provider located in Bremen, Germany, it’s Nicometo’s job to ensure that a variety of perishable goods stay nice and cool as they travel by road, sea, rail and air. “We’re building a global network of freight forwarders dedicated to temperature-sensitive products,” he says.
Temperature control is at the heart of Nicometo’s work, and RFID promises to become an important tool in his company’s mission to assure customers that their products will never be exposed to excessive heat or cold. Nicometo believes that sensor-equipped RFID tags—with their ability to continuously and seamlessly monitor an item’s temperature throughout its journey from grower to customer—mark a major improvement over existing temperature-monitoring technologies, such as digital data loggers, time temperature indicator (TTI) labels and chart recorders.
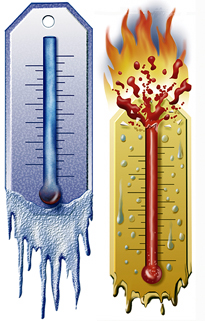
Specialized RFID monitoring tags promise to revolutionize the shipping and handling of a wide range of perishable products—from food to pharmaceuticals. By shifting environmental monitoring from trailer-, container- and warehouse-mounted devices to individual pallet tags, RFID will give suppliers and distributors continuous and accurate readings throughout the distribution process. “It will permit in-transit monitoring of goods at a level of granularity that’s much better than the single-point, whole-load environmental logging devices that are in common use today,” says Chris Hook, a cold chain technology analyst at Deloitte Consulting.
Precise, frequent and automated readings, interpreted by software and coordinated with existing and planned product inventories, should translate into more intelligent goods management and fewer rejected shipments, says Bill Hardgrave, director of the RFID Research Center at the University of Arkansas. “The benefit is the visibility it gives you all along the supply chain,” he says. “You can see, in regular time increments, what’s happening with the product, whether it’s temperature, humidity, shock or vibration.”
Cold Facts
Ensuring that shipments stay at or near a specified temperature is a priority for companies operating in the cold chain, where deviations of only a few degrees can lead to spoiled goods and thousands of dollars in damages. While most cold chain players strive to keep their products chilly, the market actually covers items requiring a variety of special environmental conditions. “Cold chain means anything requiring a controlled environment,” says Hardgrave. “It could also be something requiring hot temperatures or high humidity or low humidity—but it all gets lumped under the cold chain umbrella.”
While its name may be somewhat misleading, a growing number of businesses are beginning to view the cold chain as one of RFID’s most promising frontiers. Hardgrave says there’s a growing business case for cold chain RFID. “Fifty-six percent of all shrinkage in a supermarket is attributed to perishables, to the tune of about $35 billion a year,” he says. “If we can reduce that by 8 or 10 percent or so, that’s a huge benefit.” Also losing significant sums to harsh environmental conditions each year are firms that ship pharmaceuticals, fresh flowers, live animals and precision electronics.
With large amounts of money at stake, it’s not surprising that cold chain RFID has generated so much vendor interest (see “Who’s Who” box on page 29). Yet, despite the apparent benefits and vendors’ best efforts, getting RFID into the cold chain is proving to be a formidable task. That’s because early adopters face a variety of barriers, including high up-front costs, iffy reliability, poor interoperability and a lack of successful deployments to base models on. As a result, while most parties generally agree that cold chain RFID is a good idea in theory, real-world adoption has been sparse. “Companies aren’t exactly lining up to deploy a technology that currently doesn’t have a track record,” says Hook.Pilot Test
Although cold chain RFID has yet to establish much of a real-world footprint, the lure of potential benefits is proving too strong to resist, inspiring many potential adopters to give the technology a test drive. “Companies will do small trials, pilots, to demonstrate the return on investment and, hopefully, it will scale up from there,” says Raghu Das, CEO of IDTechEx, a technology consulting firm. “It’s almost a chicken and egg situation.”
Last September, Nicometo and Cool Chain Group launched its first cold chain RFID pilot. The project monitored food products transported inside refrigerated trucks operated by the company’s Rungis Express subsidiary, a carrier that specializes in luxury, high-end food products. “The test ran for about two months, and we got back some pretty surprising results,” Nicometo says. “We found out that even though we have state-of-the-art trucking and cooling equipment, we weren’t getting completely accurate information as to what was happening inside the three different chambers.”
As verified by the RFID technology, temperatures varied by several degrees at various locations within the truck. Temperatures also rose and fell as the vehicle’s door was opened and closed, and as the refrigeration system moved through its defrost cycle. “We saw temperature spikes that were a little more drastic than we thought we would see,” Nicometo says.
The pilot showed Rungis Express that placement position within a truck or container could either extend or shorten a perishable item’s life. “We were able to find that there are certain kinds of products that really shouldn’t be put into certain parts of the compartment,” Nicometo says. “Products, for example, that can’t take the full blast of the cooling fan.”
The project evaluated 13.56 MHz HF tags developed by KSW Microtec and enhanced by Sealed Air. The short-range devices, when pinged by handheld interrogators, allowed Rungis Express to monitor temperatures on a variety of time scales. “You can tell it to check the temperatures every 15 minutes or every 10 seconds,” Nicometo says. He adds that longer-range tags would allow fixed interrogators to instantly retrieve data without human intervention. “When a truck backs up to the dock, we would automatically know if there were any temperature problems in the truck.”
Although Nicometo is still evaluating the pilot’s results, he’s certain that cold chain RFID is destined to become a key technology for Rungis Express. “We’re going to be tagging a bunch of products, especially the higher-cost commodities with the most vulnerable shelf life,” he says. “We’re really going to tag that stuff to make sure that, as it comes in and is inspected, we know what temperatures they have been through.”Making the Business Case
While cold chain RFID has yet to work its way into the logistics mainstream, most observers believe that it’s only a matter of time—perhaps as little as a few months—before the technology begins to become more widely adopted. Hardgrave, who has advised several pilot projects, is encouraged by the progress he’s seen so far. “The companies are getting the insight they desire and are going to be well poised to adopt the technology,” he says. “I think that by the end of this year, we will see a lot of companies starting to get a tremendous payback from this technology.”
Cold chain RFID’s biggest drawing card is that it can help cut spoilage-related costs by making sure that only products that are truly spoiled, or subject to imminent spoilage, are rejected by customers. As Cool Chain’s pilot showed, environmental conditions can vary widely within a truck or other enclosed area. Pallet-level monitoring, enabled by cold chain RFID technology, allows small groups of products to be evaluated separately from their neighbors. Rather than rejecting an entire shipment outright, as might be the case with a single-point monitoring system, goods can be considered on a pallet-by-pallet basis.
Unlike TTI labels, data loggers and chart recorders, RFID also offers the possibility of hands-free operation. “RFID is painless, meaning I don’t need an employee taking measurements,” says Jean-Pierre Emond, co-director of the University of Florida’s Center for Food Distribution and Retailing. “Any time that my shipment passes by something, I can retrieve the data—I can always monitor it.”
With abundant, accurate data at their fingertips, many cold chain players plan to use RFID technology to take environmental monitoring to a new level, allowing product spoilage to not only be detected but also predicted. “If there were any temperature abuses, we can do ‘FEFO,’ which is First Expiring, First Out inventory rotation,” says Nicometo.
Using a FEFO strategy based on cold chain RFID data, a food distributor can direct shipments to the specific store, or store group, in the most advantageous location. “Let’s not ship this stuff that’s only got one or two days left on a three-day truck ride cross-country,” Nicometo says. “Let’s ship to that store that’s across the city and send the stuff with the longest shelf life to the farthest place.”
Deloitte’s Hook feels that FEFO may be cold chain RFID’s most innovative application. “It’s a wonderful and practical example of doing a better job of reducing spoilage by acting on new information shared between partners in the supply chain,” he says.
Hardgrave describes FEFO as a simple concept with a powerful impact. “It’s kind of a subtle, simple shift,” he says. “But it’s also a very profound one, because then we start looking at food quality as the indicator of when we take it out to the shelf, not the date when we received it.”Splashing Cold Water
While cold chain players eagerly anticipate RFID’s benefits, the emerging technology’s various deficits tend to slap them back to reality like a faceful of cold water. High up-front costs are a big concern for both vendors and customers. Simply put, cold chain RFID tags cost much more than ID-only counterparts. “It’s quite expensive because you’ve got to pay for the sensor and the battery if you want to monitor the temperature,” says IDTechEx’s Das.
RFID’s cost premium is not insignificant. “If I use a data logger, it’s only a few dollars per shipment,” Emond says. Temperature-sensing RFID tags can run anywhere from $10 to $60 apiece. And that doesn’t include the cost of interrogators, software, training and other required system elements. “Where is the ROI if I invest this kind of money?” Emond asks.
Nicometo estimates that a hypothetical cold chain company, spending $3.6 million yearly on 200,000 vehicle-mounted non-RFID temperature monitors, would have to spend an additional $4.2 million to switch over to RFID tags. That’s assuming a cost of only $15 per tag, and that each tag can be recycled 10 times. “It would be 26 monitors per truck rather than one,” Nicometo says. “They’re increasing their cost per load from $18 to $39.”
The good news is that cold chain RFID’s ability to reduce spoilage and help businesses distribute perishable goods more efficiently can more than compensate for its extra cost. “If you’re doing billions in monitored goods a year, and you’re able to save just an additional 1 percent with cold chain RFID, it’s probably more than worth the investment,” says Nicometo.
Cost issues aside, tag reliability is turning out to be one of the technology’s major headaches. Unlike conventional RFID tags, cold chain devices require precise adjustment before being placed into service. “We still have to go through a fairly elaborate process of calibrating these tags and making sure that the scales are set right and that they’re recording the right temperatures,” says Hardgrave. Tags that aren’t properly calibrated will deliver incorrect and potentially misleading data.
New tag designs could prove to be the key to more easily calibrated devices. Gentag, for example, reported last summer that it had successfully tested a low-power, single calibration point sensor circuit that can be directly integrated onto any RFID chip. The design could be used as a reference circuit to produce accurate, active sensor tags at a cost lower than today’s devices, says John Peeters, Gentag’s president. “When you test an RFID tag, you know the temperature of the room where the tag is tested,” he says. “If you plug that number into the tag, then you have a completely accurate temperature reference sensor technology.”
The technology will also allow the production of “very low-cost, essentially disposable sensors for RFID,” Peeters says. “We anticipate [that] probably toward the end of this year, or early next year, these sensors will be available.”A Matter of Time
A technical glitch plaguing some cold chain RFID tags is inaccurate time-keeping. “With the KSW tags, we found quite a bit of time variation,” Nicometo says. In an effort to cut cost, size and power consumption, many tag makers have opted to skip quartz crystal time regulation in favor of chip speed and other less reliable methods. Unfortunately, minor time inaccuracies can multiply quickly, particularly on lengthy journeys, leading to inaccurate and potentially misleading data records. “If there’s a temperature problem, and you’re off by seven or eight hours, you could assess the blame on the wrong party,” Nicometo says. He believes that tag vendors need to pay more attention to the problem and design products with more accurate timing systems. “Otherwise, they’re not going to be usable,” he says.
Tag durability, and the idea of devices failing either suddenly or gradually, is a prospect that worries many potential cold chain RFID adopters. While virtually all RFID tags need to function in rough settings, cold chain devices must handle the extra burden of extreme operating environments. Frozen foods, for example, are usually transported at sub-zero Fahrenheit temperatures.
But fears over cold chain tag failure may be mostly unwarranted. Hardgrave reports that the tags he’s tested in his lab, at temperatures as low as minus 10 degrees F, have proved to be remarkably durable. “We have had problems [with] the tags getting too brittle or the adhesive not holding,” he says. Yet Hardgrave believes that such relatively minor problems can be easily solved by switching to different, more durable materials. “For the most part, we’ve really been impressed with the technology,” Hardgrave says. “What we’ve worked with has been really good.”
While cold chain RFID tags are proving to be surprisingly durable, they still don’t play well with many retail RFID systems. In fact, many see interoperability as a critical obstacle that is hindering cold chain RFID adoption. Most current RFID cold chain systems are based on either LF or HF technology, meaning the systems aren’t compatible with the UHF RFID technology employed by major retailers, such as Wal-Mart.
The inherent mismatch between cold chain and retail RFID technologies currently limits a shipper’s ability to discover why a particular shipment went bad, since it can’t interact with the retailer’s UHF system to uncover key background data. “At this point, companies are not effectively sharing information,” says SensorLogic CEO Ray Hood. “In the future, [cold chain] RFID should allow retailers to engage in demand-pull replenishment.”
Hardgrave believes that cold chain RFID’s eventual switch to UHF is inevitable. “When we get to the point where there’s an EPC-compliant UHF system, then we can make real-time decisions and be proactive and not just react,” he says. “If the sensors are not UHF or compatible, then you’re asking a company to have dual infrastructures, and it’s very costly to do that.”
Nicometo is already planning to leverage UHF technology’s interoperability and usability features. “It will give us the opportunity to really automate the data-collection process,” he says. Nicometo wants, among other things, the ability to read pallets while they’re sitting inside a truck, as well as during offloading. “In practical terms,” he says, “you can’t gather the data from each pallet unless you’ve got automated data capture.”
UHF-empowered automated readings, taken at frequent intervals, will lead to better product analysis and insight, Nicometo says. “They say you don’t need line of sight [with 13.56 MHz]—which is true—but if you physically have to put [the interrogator] within six inches [of the pallet], it may as well be line of sight,” he says. “Using UHF tags, we will be able to build business intelligence into the software so that we’ll get consistent decision making based on specific data points.”
Cold chain players shouldn’t have to wait long for UHF products to arrive. “You’re going to see maybe four or five UHF products hitting the market in the next 12 months,” Nicometo says. He expects the new tags to come in at about the same price range as current LF and HF devices. “But prices will also fall very rapidly the minute there’s any competition,” he adds.Moving Forward
Despite the existing roadblocks, companies working within the cold chain shouldn’t feel discouraged, Hardgrave says. “The technology is fairly new—in its infancy—and it will continue to grow and adapt,” he says.
Deloitte’s Hook agrees. “I’m seeing very encouraging signs from the point of view of companies moving through the phases of business-case developments and pilots,” he says. “There’s no question that we’re getting a standardized infrastructure deployed.”
Cold chain RFID is not as far away from the business mainstream as many people currently think, says Hardgrave. “In a few years, companies will be viewing cold chain RFID as just another cost of doing business,” he predicts. “It will provide such a competitive advantage that it will kind of force everybody else to do it.”
For Nicometo and Cool Chain Group, the future is nearly here. “The issue right now is the timing,” he says. “We’re just waiting for all the pieces to fall into place.”
Who’s Who in Cold Chain RFID
Alien Technology
www.alientechnology.com
Bioett
www.bioett.com
Coronis
www.coronis.com
Dallas Semiconductor Maxim
www.maxim-ic.com
Evidencia
www.evidencia.biz
Franwell
www.franwell.com
Gentag
www.gentag.com
Identec Solutions
www.identecsolutions.com
Infratab
www.infratab.com
Intelleflex
www.intelleflex.com
KSW Microtec
www.ksw-microtec.de
Motorola
www.motorola.com
NXP Semiconductors
www.nxp.com
Savi
www.savi.com
Sealed Air
www.sealedair.com
SecureRF
www.securerf.com
Sensitech
www.sensitech.com
SensorLogic
www.sensorlogic.com
Syntax Commerce
www.syntaxcommerce.com
Temptime
www.lifelinestechnology.com
Illustrations by Chet Phillips