ABB a global manufacturer of power and automation equipment for utility and industrial companies, is employing radio frequency identification at its factory in Helsinki, Finland, to better track outbound shipments of approximately 200,000 drives per year. The drives are frequency converters that control the rotational speed of alternating current (AC) electric motors.
ABB implemented the RFID system in order to reduce shipping errors, since such mistakes impact its invoicing process. Without a shipping receipt, the company cannot collect the funds it is owed. In addition, ABB faced a lack of floor space at its Helsinki facility, because production was rising at a rate of roughly 20 percent every year. ABB wanted to have a forwarding operator take over the task of logistics and warehousing, but was hesitant to do so because of its own unreliable, pen-and-paper-based method of manually tracking goods leaving the production area. The company believed that if it could improve its ability to track its goods shipments, it would then have reliable data to compare with that of a logistics partner—thereby reducing the risk involved in outsourcing some of its logistics and warehousing tasks.
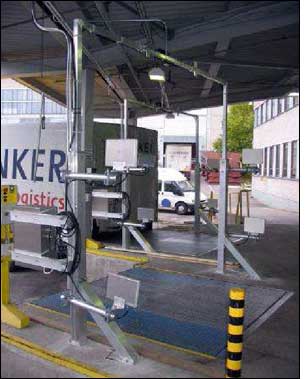
To meet this goal, ABB designed an RFID system to replace its manual shipping processes, enabling it to reduce outbound shipping errors. The company launched its RFID implementation in 2006, used the system in production by 2007 and completed the integration of the technology with its existing SAP system in mid-2009.
“By implementing RFID into SAP, we have reduced our manual work and have a more reliable way of inputting transaction data,” says an ABB spokesperson who requested not to be named, in compliance with his company’s policy. “Input time for transactions is only seconds, and we generate multiple readings at the same time with RFID—something that is impossible with the bar code.”
The SAP implementation was a lengthy process, because ABB had to simultaneously perform a general update of its SAP system. Now, the firm is working to increase the number of fixed readers it uses at its dock doors from three to seven.
The smallest drives that ABB manufactures weigh about 15 kilograms (33 pounds) and are shipped in boxes, while the largest drives weigh up to 400 kilograms (882 pounds) and are transported on pallets. As soon as a drive is manufactured, it is placed in a box or on a pallet, and a worker applies a printed adhesive label containing an EPC Gen 2 UHF inlay to that pallet or box. The drives are then loaded on trucks or trailers for short-term storage or immediate forwarding. RFID tags are interrogated as the goods are moved past fixed gate readers in the loading area near the dock doors. Information about specific goods is linked in the database to the ID number of the truck or trailer, which is entered manually so that ABB knows the loading progress of each vehicle, and has an exact description of the goods it contains.
The system produces a warning error at the gate if a worker attempts to load the wrong products onto a vehicle, and it also notifies employees when a truck’s consignment is incomplete. What’s more, by outsourcing some of its logistics and warehousing to a partner, ABB was able to free up space at its factory to expand its production capacity.
UPM Raflatac is supplying the tags for the implementation. Vilant Systems, which served as the systems integrator for ABB’s RFID deployment, provided the readers, which have a range of 3 meters (10 feet).
Later, ABB hopes its logistics partners will utilize the RFID tags on the pallets and boxes as well, in order to provide it with additional information regarding the status of goods, as well as improve its own services. The company plans to introduce item-level tracking for the components that make up the drives; a large drive may comprise thousands of parts.
In a separate application, ABB has been using RFID in a kanban process involving reusable plywood boxes since December 2005. Both the supplier and ABB read the boxes’ RFID tags. When a full box leaves the supplier, its tag is read and an electronic notice is created in SAP. Once an empty box leaves ABB’s factory, it triggers a material order from the supplier.
According to ABB, the system has decreased the manpower the company requires to process incoming packages. It has also reduced errors compared with the bar-code system previously used, the firm reports, and provided a return on investment within a few months. In December of this year, ABB plans to implement the same system at a factory in Estonia.