At its plant in Roding, Germany, automotive supplier Continental AG has replaced its card-based kanban system with RFID. The company is using the RFID system to track components from the time they are removed from shelves in its warehouse until they are assembled in a clean room.
Before the automotive supplier assembles high-pressure pumps and other mechanical parts, many components must be cleaned in industrial washing machines since every fleck of dust can cause problems in an engine. For quality purposes, Continental Mechanical Components (CMC) Germany—the Continental subsidiary that operates the plant—must be able to identify all components in each batch and recount the production steps.
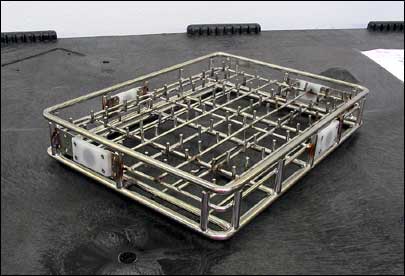
A high percentage of the components used in production at the plant must be washed; a smaller percentage, on the other hand, may not be washed under any circumstances. Workers previously used a kanban system to track and plan the pre-production steps for components, given detailed cleaning instructions for individual lots, the variety of metal cage-like bins used to carry the parts and the variety of wash settings for the washing machines. However, says Juergen Bauer, CMC’s RFID project manager, this led to mistakes and reams of handwritten lists and notes.
At the end of 2005, CMC (then known as Siemens VDO Mechanical Components GmbH) implemented the RFID system, which became operational about one year later. The company sought to speed the flow of production by cutting down on manual tracking, while also simplifying the process of assembling components for custom-ordered batches and improving production monitoring and quality. RFID software developer NoFilis served as the integrator for the project, supplying much of the software, including CrossTalk 2.0, an RFID device manager to which all of the stationary readers and PDAs in the application are connected.
Before the system was implemented, workers picked components from warehouse shelves based on a printed list, then placed the components through the specified wash programs, using plastic boxes to move the parts to the washing machines. They then placed the goods into metal carriers designed for the washing machines, which move these bins through the machines on belts much like a carwash propels cars through its facility.
When it came time to put components through the washing machines, employees had to check lists carefully to make sure they set the washing machine to the correct program. They also had to take notes about each step they made, because some components required different wash settings.
In addition, the staff did not know which components needed to be delivered to which of the four clean rooms without consulting yet another piece of paper. Once a bin left a clean room, workers placed a kanban card in a sleeve on the carrier, then sent it back to the washing area. During this process, some cards were lost or damaged, and in some cases, employees at the wash plant did not know which material to send to the clean rooms.
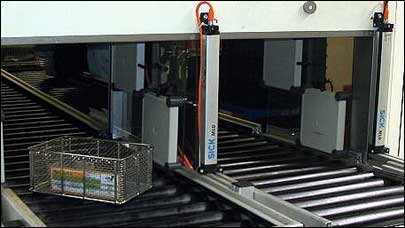
The company considered placing bar-coded labels on the metal carriers, but it quickly became obvious that these labels could not survive the washing machines. It opted instead to test RFID, and chose tags that function at 13.56 MHz and comply with the ISO 15693 standard, because of the tags’ good read ranges and anticollision properties. Workers sometimes carry stacks of bins past readers, and all tags must be read simultaneously.
CMC tagged 6,000 metal carriers. Each received four transponders—one on each side. The transponders are encased between two pieces of plastic that keep out water, and then screwed or welded onto the bins.
As part of the new process, a worker using one of the application’s 20 Datalogic PDAs connected to the company’s manufacturing execution system (MES) is prompted regarding which parts to pick from the warehouse shelves and deliver to the washing machines. Each PDA is outfitted with a bar-code scanner and an RFID interrogator. The employee scans the bar code on the carrier in the warehouse, and enters basic information about product amounts and lot numbers by scanning bar codes on a sheet of paper.
The worker then moves the components to the staging area in front of the washing machines, places them in the proper type of RFID-tagged metal carrier and uses the PDA to interrogate the bin’s RFID tag. The system matches the tag’s unique ID number with the information about the batch that was just picked. A stationary reader installed at the belt’s entrance to the washing machine then reads the carrier’s tag and, with the help of CrossTalk, programs the washing machine with the appropriate wash cycle.
The system uses a total of 38 stationary interrogators at various points—usually at separation or turning points along conveyor belts, or at small portals through which workers pass bins manually. At each juncture, two readers, one on each side, interrogate the tags on the carriers before they move toward their destination. CrossTalk 2.0 activates the readers and coordinates the information they collect. If a carrier is moved to the wrong place, a red light warns staff members to refer back to the PDA for additional information.
NoFilis and CMC set up and tested the entire system before switching over to it. “We decided to go for the big bang since all the processes are linked,” Bauer says, adding that it took a month of continuous training for workers to feel comfortable with the new system.
On the hardware side, CMC spent roughly €2,100 ($3,300) on each stationary reader, €2,000 ($3,100) on each PDA, €1 ($1.60) on each tag and encasement, and about €20,000 ($31,300) on server hardware to run the system. CMC says it has not yet calculated an ROI since the focus of the application is on process improvement and automation of the washing process, but Bauer estimates that the company has benefited by transferring four people to different jobs.
Since the system has been up and running, operators have only faced minor problems such as inoperable tags on carriers that were dropped, or short system outages due to a sudden lack of electricity. CMC says it and its customers are convinced of this RFID application. “Some of our customers were surprised by the system-integration level,” Bauer says, “and quite pleased with the system.”