Manufacturing facilities have evolved to the extent that a factory worker from 50 years ago would scarcely recognize them in this age of Industry 4.0. However, in the interim, automation, safety breakthroughs and technology solutions have made factories safer, more efficient and more cost effective.
While Industry 3.0 revolved around the computerization of factories, Industry 4.0 seeks to add artificial intelligence, machine learning and augmented reality to a growing wave of technical integration. Each technology has a place on the factory floor, and a contribution to make toward revolutionizing manufacturing practices and processes. If Industry 4.0 seems like smoke and mirrors, consider that in 2019 we witnessed a growth of 400% in the number of digital transformation initiatives across industries, including manufacturing.
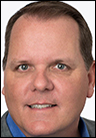
Industry is moving quickly from rollout to continuous process improvement. A recent Rockwell Automation study showed that 30% of digital transformation initiatives are moving through the post-implementation stage, up 7% from 2018.
Coordinating and Integrating IT and OT
Operational technology (OT) and information technology (IT) have proven to be much less effective when placed into silos. When the left hand doesn’t know what the right hand is doing, too often you end up tangled in a knot. The free flow of data between OT and IT in the form of data and analytics sharing frees up resources and provides insights to power rapid, scalable and secure connectivity.
It’s tempting to say that next-generation technologies like AI, machine learning and AR don’t really belong on the factory floor. Just remember, someone was saying the same thing about computerization in Industry 3.0.
AI can sift through the mountains of data generated by the Industrial Internet of Things (IIoT), isolating and analyzing trends to create efficiencies, improve safety and reduce production time—which enables the return of maximum value. Machine learning can train your AI to provide precisely the information that is most valuable to your organization, eliminating the need to sift through reams of unimportant data before getting to the “good stuff.”
Augmented reality (AR) must seem like the biggest stretch of all. However, imagine a scenario in which you could use AR to visualize new production prototypes, products and more. In addition, AR can interface with AI to provide a look into the guts of your factory floor in search of process improvement and safety enhancement. With a growing skills shortage and the need for employee cross-training, AR becomes a valuable asset. The technology can help novice workers and experienced staff alike train in a digital environment to learn how to handle problems—all with high precision.
The Benefits Are Clear When You Integrate IT and OT
First, you must accept the inevitability of the alliance between OT and IT. Tighter integration between them will be essential as more OT infrastructures like plants, devices and production lines are tied into digital transformation initiatives.
Enhance Workforce Productivity
You have a workforce made up of two kinds of employees: skilled workers who are old hands at manufacturing and new hires who require training. Often, the learning curve can be steep and turnover can be high, but technologies like AR can help upskill both experienced and inexperienced personnel.
However, you can’t forget that even experienced and tech-savvy workers will need time to ramp up to Industry 4.0. Just because you can drive a car doesn’t mean you can drive a semi-truck. When you encourage collaboration between IT and OT, you’ll see overall improvements in productivity and time to market.
Improve the Performance of Your Enterprise
Integrating OT and IT can have a direct impact on whether you remain or become more competitive in the global manufacturing landscape. IDC predicted that global spending on the IIoT in discrete and process manufacturing would top $197 billion in 2019. While it’s still too early to test the veracity of that prediction, it’s clear that spending and adoption will continue to grow.
It’s easy to fall into the trap of thinking that if that you have smart RFID tags or other smart sensors, you’re “doing” Industry 4.0. While there’s no doubt that RFID ushered in a whole new era in manufacturing, the IIoT is about so much more. Incorporating data from RFID feeds the IIoT engine, providing mountains of raw data that AI can decipher, and that machine learning can understand. The integration of OT and IT provide context to the data, enabling analytics that help you understand—and improve—your factory operations. For example, it’s now possible to use RFID data to implement food chain safety practices, or compliance and quality records.
In fact, comprehensive analytics gathered from data transmitted by RFID, insights from sensors, inventory systems, automation systems, robots and safety equipment provide you with a complete, 360-degree view of your manufacturing operations. Introduce enterprise operational intelligence, including floor-wide monitoring, predictive maintenance, and management in real time. Then it’s easier to identify opportunities to continuously iterate and improve automation and service delivery methods.
Optimize What You Already Have
Don’t throw out the baby with the bathwater—despite rising complexity and cost reductions, you have an impressive infrastructure to leverage. When you improve predictive modeling to anticipate and visually assess issues, you can address them before they lead to unplanned and expensive downtime.
There’s also a case to be made for getting sophisticated with your existing infrastructure. Introduce new technologies—AR, AI and machine learning—to monitor and manage performance and maintenance.
Beat Production Deadlines and Deliver Quality Products
As with most things, the solution for rigidity is dynamism—stay moving, keep information flowing across the factory floor and expand capabilities. Create dynamism by employing next-generation technologies and having easy access to visualizing the data. Process integration then leads to asset and system auto-discovery, data model sharing and re-use, along with integrated analytics. Prediction is power; everyone knows that the person with vision has an edge, and predictive technologies will help identify trends and decide where or if they fit into your organization.
Industry 4.0 is here, and experts are predicting even more groundbreaking developments to build rapidly. One thing is certain in this time of blindingly fast change: integrating IT and OT and employing those connections to fuel a whole new take on the factory floor is an idea whose time has come.
Keith Higgins is the VP of marketing, digital transformation and IIoT at Rockwell Automation. He previously served as the VP of marketing at FogHorn and the CMO at RiskVision, until its acquisition in 2017. Higgins was also CMO at Symphony Teleca Corp., an IoT and connected services company, where he played an integral role in doubling the company’s revenue, leading to a nearly $1 billion acquisition by Harman.