The United Arab Emirates (UAE) Ministry of Health (MOH) is deploying one million RFID tags across 147 facilities, in one of the Middle East’s largest RFID deployments to date. The system, provided by OgTech Technology Solutions, involves managing the locations of health-care, IT and mechanical assets throughout the ministry’s hospitals, health centers, clinics and administrative buildings across the UAE.
With the technology in place, hospitals and clinics have reported that they are conducting faster and more frequent audits of their assets, while nurses and health-care providers can locate the tools they need for patient care, and maintenance personnel can quickly identify any equipment that requires maintenance, cleaning or service. The ministry is applying a phased approach to the deployment, and has thus far taken the system live at 10 of its largest facilities, according to Khaled Mohamed Ezz El Din, OGTech’s regional manager. The goal, he says, is to roll out the technology to all 147 locations by the first quarter of 2020.
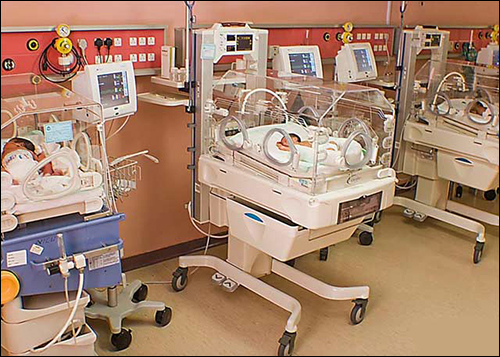
OgTech, an affiliate of the Osman Group, is a systems integrator specializing in RFID and security-based solutions. The company maintains four offices throughout the Middle East and the United States, with its headquarters in Egypt. The firm first approached the UAE MOH in 2017 to propose a UHF-based asset-tracking solution, Ezz El Din recalls, which led to the ministry’s widescale deployment.
Each of the MOH’s facilities is responsible for hundreds or thousands of assets, including wheelchairs, pumps and diagnostic equipment, some of which need to be located quickly for use on patients. In some cases, equipment is loaned between different facilities as well. To ensure that the necessary equipment was at each site, staff members conducted audits by scanning the barcodes of items within each area or room. This was a time-consuming process that didn’t happen as frequently as the ministry would have liked, however.
OgTech worked with the ministry to develop ways in which to optimize its operation. “We proposed a solution design,” says Ezz El Din, and the ministry initiated a subsequent tender, for which 10 companies competed. The OgTech solution was ultimately chosen. The system consists of passive handheld UHF RFID readers, which are used at each clinic or hospital. Because there are many kinds of assets, including different form factors and materials, the firm opted to provide a variety of RFID tag types—primarily from Smartrac Group—as well as Zebra printers to print and encode the labels prior to application. Metalcraft tags were selected for on-metal tagging.
The scope of the solution has grown beyond managing health-care equipment—such as pumps, wheelchairs and patient beds—to also include office furniture, IT equipment, and mechanical and electric components used for the operation of each facility. In that way, staff members could identify fixed items like generators and surveillance cameras for maintenance purposes. Some equipment, in fact, is located outdoors, including air-conditioning units, in temperatures that can peak above 50 degrees Celsius (122 degrees Fahrenheit). Therefore, Ezz El Din says, the most rugged tags are used for those applications.
For all applications, OgTech wanted the system to require little effort by hospital or clinic personnel outside of their existing tasks. For that reason, the software that captures and manages read data is integrated with each facility’s existing management software. Thus, every tag read links to the asset data stored in that software. “We were very keen to make the system quite convenient and friendly to all the business users,” Ezz El Din states. The system was integrated with MOH’s Microsoft enterprise resource planning (ERP) system. “We worked closely with their ERP team to integrate our devices directly with their ERP, to avoid any double work between interfaces.”
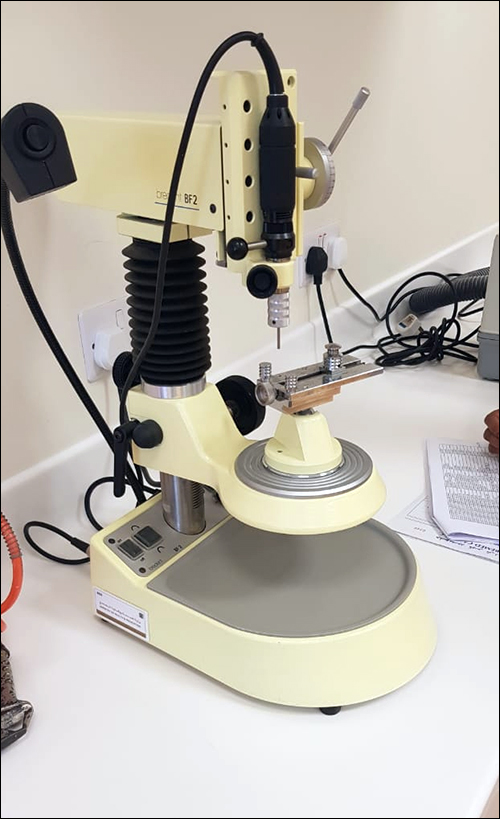
Software integration was completed at the end of 2018, then tagging began to take place across the ministry’s properties this year. OgTech is providing training on how to use the technology at each facility. Every new deployment consists of confirming and updating the physical inventory for each property, then migrating the facility’s asset register to the RFID system. Next, workers begin tagging all assets and carry out inventory counts using a handheld.
“We hold a workshop for their business users to get familiar with the technology,” Ezz El Din explains, as well as training them to apply the RFID tags. This includes selecting the right tag for each asset and the proper location on that item where the tag should be applied. In most cases, employees apply tags in a discreet or invisible location so that they are unlikely to be damaged or removed, but they can still provide a read range of about 5 meters (16.4 feet) when interrogated.
Staff members can now carry an ATID handheld UHF RFID reader that captures the tag ID of every tagged asset within a range of about 5 meters. Since each tag is linked to an asset’s own description and ID, the tag read updates the facility’s digital record of each item and its location. The firm can conduct audits within a shorter period of time than it previously could with non-RFID-based counting, by simply having a worker carry the reader around the facility from room to room, capturing information about what is stored or in use at each location.
The handheld unit can also locate missing items or identify a specific piece of equipment. Personnel can input the item they seek in the ATID handheld, then walk around the facility or room until the reader detects that asset’s tag. Users can follow the closest route to that item, based on the sound notification from the reader. “Sometimes,” Ezz El Din says, “they simply need to do an audit, and they can do this easily at any time. The process is quite dynamic.”
The second phase of the project includes fixed readers. UHF RFID portals from Feig Electronic are being installed at pilot locations at hospital entrances and exits. The system will automatically capture the unique ID of every asset that leaves or returns to the facility. In that way, if an item is being moved in an unauthorized manner, the OgTech software will provide a notification to management or trigger an alarm.
Those deploying the system first are mostly larger hospitals, which health centers and remote clinics—some with only 100 or 150 assets—are following. With a deployment of this size, Ezz El Din notes, “One of the challenges we are dealing with is big data. To do the data migration in their system has been very challenging,” he adds, as the technology company built the solution to make the integration process easy.
While the initial project is isolated to asset management, the next application the ministry is discussing with OgTech involves tracking medications. Many of the medicines used at the facilities are stored in warehouses before being shipped out. By applying an RFID tag to each bottle, vial or package of pharmaceuticals and installing a combination of fixed and handheld readers, the ministry hopes to have a better understanding of where drugs are located, when they are due to expire, when they require replenishment and under what circumstance they might end up missing. Since the system was taken live, the MOH reports that it has made inventory data more reliable, and audits faster and less labor-intensive.