Eskimo Cold Storage, a frozen foods storage company based in Gainesville, Ga., has already saved $100,000 since installing RFID readers about four months ago, and forecasts an annual savings of $233,000. The company installed an RFID reader at the end of 20 aisles within its warehouse, so that it could confirm where its thousands of pallets are located as they are put away or removed. The solution, says Karen Reece, Eskimo Cold Storage’s VP, ensures that loaded pallets can be quickly located when required for outgoing shipments—thereby reducing the amount of labor required to search for missing goods, while also preventing the need to pay a customer for something that is missing. The RFID technology, which captures read data collected from tagged pallets and forwards that information to the company’s warehouse-management system (WMS), was provided by Jamison RFID.
The company provides cooling and storage for food producers. The vast majority of the products consists of chicken, but also includes seafood. Businesses bring the meat to Eskimo Cold Storage to be flash-frozen and then stored in freezers until purchased by customers within the United States or overseas. Eskimo focuses on making the product available 24 hours a day, seven days a week, as needed. Its facility spans 10.9 million cubic feet and has 32,000 pallet positions that rise seven levels high in the cold-storage area, in about 50 different aisles (each with 600 pallet positions), while 480 pallets are received and shipped daily by approximately 20 trucks.
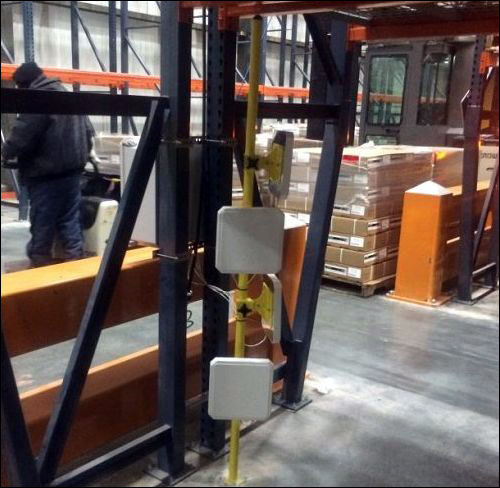
When a customer’s palletized products arrive by truck, they must be frozen and stored, and another truck might pick up those same products only a day or two later. Two of Eskimo’s largest customers require especially fast turnaround times (with goods available at the dock doors at a very specific time), and the palletized products must be reloaded on a truck in the identical configuration they were in when delivered to Eskimo.
To meet these demands, Eskimo Cold Storage employs a Datex WMS that tracks which pallets are onsite and where they are located, based on their shelf and aisle locations within the cold storage area. Operators feed information to the warehouse-management software by using a handheld device to scan a bar code on the pallet label and then inputting the shelf and aisle ID numbers while moving each pallet into storage.
This works well about 97 to 98 percent of the time, Reece says. However, she notes, there are occasions when the operator might fail to complete that step, or when a pallet may be moved and its new location not entered into the system. When this occurs, the company has no choice but to dispatch two to six staff members equipped with bar-code scanners into the warehouse on foot, or in forklifts, to search for that pallet among the 32,000 that could be in storage. Searching for a missing pallet can takes days, she notes. If the team fails to locate the specific pallet, Eskimo must then pay the amount that a retailer would have been charged for the goods, as well as cover shipping costs.
Because the accuracy of its pallet location data was still fairly high, Eskimo did not want to disrupt its existing system. Rather, it opted to improve on it. The firm was especially concerned about products for the two companies that had the most stringent requirements regarding shipping times and also represent about 60 percent of Eskimo’s total sales, Reece says.
Jamison RFID installed a Motorola Solutions FX7400 fixed RFID reader with four Motorola AN480 antennas at the entrance to each of the 20 aisles in which the two customers’ product are stored, says Monte Lucas, Jamison RFID’s president, with 10 readers installed in summer 2013 and 10 more added this spring. Each reader, with a cable connection to Eskimo Cold Storage’s back-end server, captures the ID number of the EPC Gen 2 ultrahigh-frequency (UHF) RFID label attached to each pallet. The 4-by-6-inch label itself, which contains an embedded Alien Technology Squiggle inlay, is provided by Mid South RFID, which prints and encodes the labels prior to shipping them to Eskimo Cold Storage.
According to Lucas, Jamison RFID selected the Mid South RFID labels due to their ability to withstand very low temperatures. “The performance of the tags has been fine,” he reports, even in the subzero temperatures.
When Eskimo Cold Storage receives a shipment from one those two major customers, a worker applies an RFID label to each pallet. The ID number, along with related customer and product information, are inputted into the Datex WMS. The pallet is typically moved through the flash-freezing process and is then taken to the warehouse. As the forklift driver enters the aisle where the palletized goods will be stored, the RFID reader captures the ID number. The operator is then expected to scan the bar-coded ID printed on the pallet label, and to input the pallet’s aisle and shelf storage location, just as was done before the RFID system’s installation. If the driver forgets to do this, the system will still know the aisle in which the pallet was stored. When the pallet is later removed, the reader again captures its RFID inlay’s ID number and the WMS software is updated to indicate it has been removed from storage.
If a pallet ends up missing, employees still use a bar-code scanner to locate it—but instead of checking tens of thousands of pallet locations, they now need only search 600 spots. The company continues to use bar-code technology rather than a UHF RFID handheld reader, Reece says, because each aisle’s narrow width (about 72 inches) makes it difficult to pinpoint where an RFID signal is coming from.
Since the system was fully installed four months ago, Reece says, it has saved the firm approximately $100,000 (the cost of the solution). The technology is projected to save $233,000 annually, she adds, based on the number of labor hours personnel previously spent searching for missing pallets and the cost of paying for pallets not located in time. “We’ve been extremely happy with it,” she states. “It’s helped tremendously with incidents of missing pallets.”