Global aircraft company Airbus has moved forward with multiple radio frequency identification projects aimed at increasing the visibility of its parts worldwide, as well as tools and containers, both internally and externally. Last week, the firm announced the use of hybrid RFID Integrated Nameplates to supplement its standard, non-RFID nameplates. When attached to a part, the RFID version provides identifying information not only in text and bar-code form, but also by means of its passive EPC Gen 2 tag.
The company has also developed an RFID-based system that it calls the Smart Factory, for tracking tools, logistics media and wing-production processes. Currently, two Airbus plants—one in the United Kingdom, the other in France—are using the Smart Factory solution.
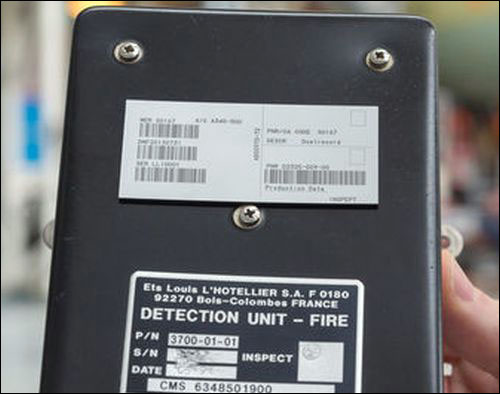
In addition, eight assembly sites for Airbus’ A380 aircraft are slated to employ an RFID-based real-time automation system for tracking work-in-progress. The solution is expected to be taken live throughout this year, plant by plant. Carlo K. Nizam, Airbus’ head of value chain visibility and RFID, described the rollout during a keynote address at the RFID Journal LIVE! 2014 conference and exhibition, held last month in Orlando, Fla. (see RFID Takes Airbus to New Heights of Efficiency, Part 1 and Part 2). The RFID system, known as Visibility of Industrial Processes (A380 VIP), was initially piloted at assembly plants in Hamburg, Germany; St. Nazauire, France; and Broughton, England. The second stage, now underway, involves the solution’s installation at all eight sites.
Airbus’ aircraft division (commercial and military) reported €42 billion ($58.2 billion) in revenue last year, with 18 worldwide sites for the design, manufacture and assembly of its aircraft. The company is developing and building multiple new aircraft models, including the A380, A350 XWB, A320 NEO, A400M and MRTT. Production-rate demands have been increasing for all aircraft, Nizam reports, and there is constant pressure for improvement and innovation in production. These demands—as well as the overall complexity of offering different products at multiple sites, within multiple countries—has led the company to research and test RFID solutions that might help it to increase visibility.
“Savings can come only from doing something different,” Nizam told the audience at LIVE!, but to improve a process, the company needs to be able to identify where parts, tools and other assets are located, and when, and thus know what is happening at each assembly site. Therefore, he said, the firm has been using RFID to gain the visibility required to identify which steps in the process require improvement. Utilizing the technology in combination with software, Nizam explained, affords Airbus a potent continuous-improvement tool. Thanks to its use of RFID and bar-code technology, the company can now move away from a paper-based view of the supply chain to a digital view.
Airbus has established what it calls the Value Chain Visibility and Auto ID Program for nonflyable and flyable parts. As part of this program, Nizam said, the aircraft company has built a portfolio of next-generation RFID-enabled systems that the firm calls “Lighthouse” processes. Each Lighthouse process represents an application in which RFID is piloted, with a goal of developing a system deployable across multiple sites. “That’s what we’ve been doing over years—developing a series of process modules, and copying and pasting them across the company,” he stated, adding, “There is no one-size-fits-all solution. You need different tags on different objects for different processes.”
One new Lighthouse project, the Smart Factory, was first deployed on an A400M wing assembly line in Filton, England, using a combination of active and passive RFID tags to track tools and parts in real time. The factory began by tagging tools, and then started tagging the wings themselves and their parts, as well as collecting work-in-progress data. The company later opted to use the technology to monitor logistics containers and safety equipment.
Airbus realized that the RFID data it was collecting was beginning to provide a large integrated picture of what was occurring on the assembly floor. “We call it Smart Factory,” Nizam said. “It’s a culmination of different capabilities.” With RFID, the company can know if a tool is not where it should be located, maintain a record of which tools were used on a particular wing, and track each wing’s assembly progress. “We can represent all info in 2 and 3D, create zones, know if tool is left behind and set up a proactive alert. It becomes a very powerful system.” Since the Smart Factory concept’s introduction to the A400M assembly line in Filton, it has been expanded to the company’s A330 and A350 final assembly lines in Toulouse, France.
Building on that success, Airbus is just finishing a project consisting of tracking parts via RFID tags at eight manufacturing sites for A380 aircraft, involving 10 buildings in four countries. The A380 VIP project is designed to provide a centralized, global, real-time automated view into the build progress across all assembly plants. Every month, the company’s executive VP of operations meets with all plant managers to review any potential problems related to the A380’s production. Prior to the RFID system’s implementation, information was not always ready in time for the meeting, since it took several weeks to gather data from all plants. To resolve this problem, Airbus put tags on aircraft sections, installed a reader network within each factory and began tracking those sections, collecting data instantly, every 30 seconds that it was refreshed.
The company realized it could thereby collect a great deal of information for every assembly station and each A380 passing through that station. Airbus can then attribute financial values to different portions of the assembly process, based on each component’s movement through production.
Airbus’ nameplate program for internal parts is the result of an effort to improve on the traditional part-marking process, which amounts to attaching a yellow paper label to each part. The papers are then used at various steps throughout assembly, though they do not travel to the airline. However, Nizam noted, there are various steps during which airline and maintenance operators can also benefit from the marking. If a part is then sent back to Airbus or another company for repair, he said, there is a tremendous opportunity to use that marking data as well.
Traditionally, tracing parts requires a great deal of paper. The yellow label attached to each component usually includes handwritten data, and is utilized at various steps along the manufacturing process. When the part is installed, its label is removed and placed temporarily into a box located near the bottom of the plane. A worker then takes that box to an office and types information into the computer. “Every part has a yellow label,” Nizam explained, “but as it goes through the system, we add more paper, until we get to a point where we have lots of paper.” The process has not changed much throughout the past three or four decades, he added. What’s more, the number of parts being manufactured is increasing, which puts even more pressure on the tracking process. “We are going to have a data issue, and need to move toward a paperless system—remove that paperwork so our suppliers no longer have to provide that paperwork,” he said. “We believe very strongly the part-mark capability can improve how we trace things, not just for us but the whole value chain.”
In 2010, Airbus began attaching passive EPC Gen 2 passive RFID tags, including those supplied by MAINtag, to 3,000 parts per plane, with 700 different part numbers—all parts that were repairable—for its A350 XWB aircraft (see Airbus Signs Contract for High-Memory RFID Tags), and those tagged parts have been flying for quite some time. That part-marking system is designed to benefit everybody, Nizam said, particularly the airlines and Airbus.
Last year, the firm expanded its parts-tagging program beyond the A350 XWB, to seats and life vests across other aircraft, for a total of 160,000 tags annually (see Airbus Expands RFID Part Marking Across All of Its Aircraft Families). This enabled the company to save time and money, by reducing inventory count time and increasing accuracy. It would typically take employees 18 hours to conduct inventory counts of life vests and seats for an aircraft, whereas that process now takes only 26 minutes to complete. That system is fully deployed on the A340 and A350 planes, and is slated to be expanded to the company’s Chinese assembly line in mid-2014, and then to an assembly line in Mobile, Ala., by the end of the year. The third phase of this project will involve the tagging of other parts beyond seats and life vests, and across Airbus’ entire product family. Other plans with supply chain partners are still in the works, Nizam said.
As part of its RFID expansion efforts, Airbus is adopting RFID Integrated Nameplates to enhance the traceability of aircraft parts that it produces and uses internally. The RFID Integrated Nameplates combine the functionality of a conventional nameplate with printed text and an RFID tag, into what the firm describes as a single “compact, durable and lightweight hybrid device.” Brady Corp. and Tego Inc. jointly developed a version of the RFID Integrated Nameplate—a flexible RFID label made with Tego’s TegoChip tag. Designed for attachment to both metal and non-metal parts, the Brady-Tego nameplate is capable of being printed and encoded with ATA-compliant data records and bar codes at the time of use. In addition, Airbus announced it had also picked Fujitsu to supply RFID nameplates. Airbus now intends to expand its tagging efforts for all parts produced internally, Nizam said, and expects to be fully live with that effort by the end of this year. He declined to indicate how many tags would be used. Airbus will also utilize the nameplates on certain parts made and supplied by outside companies.
Regarding external parts, some suppliers are already using RFID technology to enable the tracking of goods through logistics and distribution to Airbus’ manufacturing sites, through assembly lines and to the airlines operating those aircraft. “We’re part of a bigger industry—it is no longer just Airbus,” Nizam stated. “We have colleagues with dedicated RFID teams. Many airlines are proactively involved in RFID.”
Ultimately, Nizam said, the use of RFID reduces the cost of aircraft production and maintenance, by speeding up processes and improving productivity. “It helps us reduce the cost of producing our aircraft,” he said.
What’s more, Nizam noted, the technology allows Airbus to set alert parameters in the event of exceptions in a product’s processing, and to monitor actual performance against targeted performance levels during manufacturing, thereby leading to a more competitive business process. “That’s the real business case,” he said.