When a food-production company’s safety inspectors examine production lines each day to ensure they have been thoroughly cleaned of any potentially pathological microbes, they randomly select a few representative areas to test. Neogen Corp., based in Lansing, Mich., markets and sells a device that enables the testing of cleaned production-line tools and components. In July 2013, the firm added a radio frequency identification option to its AccuPoint2 hygiene-monitoring system, automatically providing a random sampling of which sections of the production line to test. The system consists of RFID transponders embedded in signage mounted throughout a production facility, as well as an RFID reader built into the AccuPoint2 testing unit that interrogates those transponders. It also comes with software in the reader that randomly selects an area for an inspector to test, indicating that spot on the device’s screen. In addition, Neogen provides software that resides on a user’s back-end system to manage the collected AccuPoint2 data.
After each daily production cycle, food companies must clean their conveyors, slicers, hoppers, grinders and other equipment used to manufacture food products, and then dispatch inspectors to perform sample testing to confirm that no pathogens, allergens or other potentially harmful matter is left behind. According to Neogen, these inspections are intended to be conducted on random areas using tools such as Neogen’s handheld AccuPoint2 device, which tests for adenosine triphosphate (ATP)—found in all organic matter—making it an efficient method for tracking sanitation.
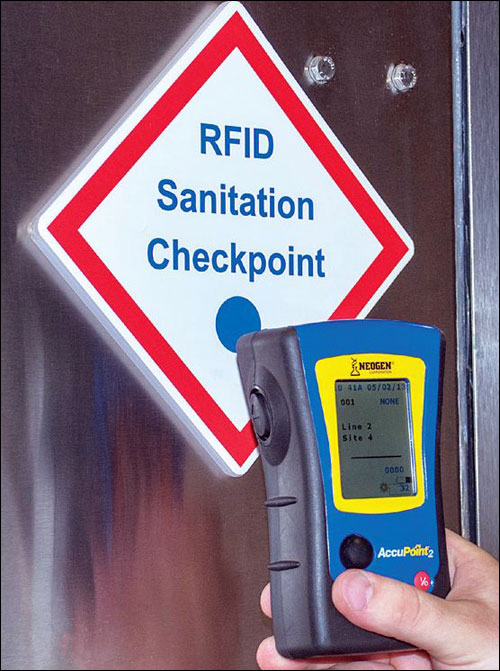
With the AccuPoint2 system, an inspector first wipes a swab across the surface of an item being tested, placing the swab (attached to a plunger) into a cartridge containing a material known as luciferin or luciferase, which glows slightly when exposed to ATP. The cartridge is then inserted into the AccuPoint2 device, which measures the amount of light produced and displays the results on the device’s screen. The AccuPoint2 unit stores that ATP reading, along with the inspector’s name, the date and time, and the test’s location, which a user would need to select on the device by toggling to that site (such as “site 1”) on the screen. Once the inspections are completed, the device is plugged into a computer’s USB port, and the AccuPoint2 software then manages and stores that test data for use by the company’s management. Areas that fail the test must be re-cleaned and re-tested.
The system’s shortcoming, says James Topper, Neogen’s market development manager, is that inspectors or managers must make choices regarding which sites to inspect each day, since not all sites are inspected after every production shift. This can require management to determine which sites have not been tested for some time, and to direct inspectors to those sites—or it can require the inspector to make a selection at the time the process is carried out, which defeats the concept of a random test.
Therefore, Topper says, he and Robert Soule, Neogen’s product manager for the AccuPoint line, began considering ways in which RFID could help improve the process. Since 2012, the company has been offering an RFID option for users of its AccuPoint HC testing equipment for the health-care market. In this case, a worker utilizes the handheld AccuPoint HC device to measure the ATP level within a hospital room after a patient has been released, but would use high-frequency (HF) 13.56 MHz passive RFID tags and readers and Neogen’s software to determine which surface to test. Tags are affixed outside of patient room doors. A user taps the RFID-enabled version of the AccuPoint HC device against the tag, and the device’s built-in RFID reader captures that tag’s ID number. The device’s firmware identifies the room and pinpoints which surfaces had been recently inspected, then lists instructions indicating which surface (such as a bed rail or a door knob) to test.
“We wrestled with the idea of RFID and how it could be used in food safety,” Topper states. Neogen began building RFID readers (designed by Neogen and made with a Texas Instruments TRF 7960 reader chip) into its AccuPoint2 devices to be used for food safety. The RFID-enabled version of the AccuPoint2 was released in July 2013, and is presently being used by companies that make a variety of food products.
The transponders, consisting of Texas Instruments’ RF-HDT-DVBE encapsulated 13.56 MHz RFID tags complying with the ISO 15693 and 18000-3 standards, are embedded in signs measuring 4 inches by 4 inches. These signs are mounted at various sites throughout the production line, posted on pillars or walls with instructions printed on the front for users to tap the reader at that sign. Topper says that the RF-HDT-DVBE tag—about the size of a U.S. quarter—was selected due to its rugged form factor, which makes it impervious to such conditions as the presence of water or heat.
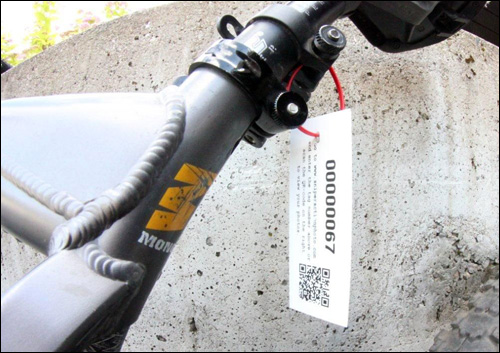
Each tag’s unique ID number is stored in Neogen’s software residing on a user’s back-end server, as well as on the AccuPoint2 device. Once the unit reads the tag ID, which is associated in the software with a group number, the software assigns a test site within that group and instructs the user to inspect it. The system can also be configured to list hot spots—sites that must be inspected daily, for example—which can be displayed in red, along with any random suggested sites.
For customers, Topper says, the RFID technology ensures that users have a full sample of all sites being tested on a regular basis, which can then be collected and analyzed, or be presented to customers or government inspectors. Analysis can include monthly averages, or production lines that have a higher percentage of failed tests, as well as when those failures occurred. Neogen, however, continues to offer a non-RFID version of the AccuPoint2 system as well.