Several Miami-based restaurants and bars are employing a radio frequency identification solution that identifies and weighs liquor bottles, and then transmits that information to a server where it can be linked to point-of-sale (POS) data. In this way, management can know how much of each type of liquor is being poured, how customers are then being charged at the register, and when any discrepancies might occur, such as an over- or under-pour, a missing bottle or unbilled pours.
The company providing the solution, BarMaxx, is a spin-off of Maxx Technologies, which is partly owned by Suxessbar Systems, an Austrian provider of RFID-based bar solutions. Several U.S. companies were already utilizing Suxessbar Systems’ RFID technology during the past three years, and BarMaxx was launched in October 2012 to provide American bars and restaurants with a full system designed to go one step further than Suxessbar Systems’ prior offerings. The BarMaxx version provides RFID tracking not only within a bar setting, but also within a storage room. What’s more, says John Zevgolis, BarMaxx’s CEO, the solution has cameras integrated into it, enabling users to view video footage of what was occurring at the time of an exception report—such as a bottle’s unaccounted-for removal from the storeroom.
According to BarMaxx, its system has been successfully installed at multiple restaurants and bars throughout South Florida, including The Forge, which has been using the solution since 2010, as well as City Hall Restaurant and Wood Tavern. BarMaxx provides passive high-frequency (HF) RFID tags (for competitive reasons, the company declines to disclose its tag supplier’s identity, or with which RFID standard the tags comply) for tracking liquor bottles. A tag is first attached to the bottom of each bottle upon its receipt. The tagged bottle can then be placed on BarMaxx’s RFID reader, with its own proprietary built-in reader hardware wired to a bar-code scanner. As the reader captures the tag’s unique ID number, it links that ID with data from the bottle’s bar-code scan, and sends the collected information to software residing on BarMaxx’s server, which stores that data for the end user.
The bar staff can then place the bottle on a shelf within the storeroom. BarMaxx provides Feig Electronic RFID readers wired to its own antennas, which are installed on shelves. The antennas interrogate each bottle’s tag ID, periodically forwarding that data back to the software via a wired connection. In the event that a bottle is removed, the system detects that action and allots a specific amount of time for the bottle’s unique ID to be read by an interrogator located at the bar itself. If none of the bar’s readers detect that tag within the designated time span, the software notifies the bar manager that a bottle has been removed from the storage room and is now missing.
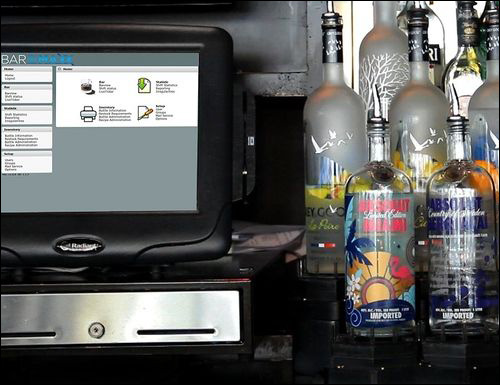
The bar has readers built into scales in which a bottle can be placed. Some bottles are on display on shelves behind the bartending area, while others are located at the “speed rail” at the front of the bar, where bartenders can quickly access them. Each bottle is placed on an electronic scale fitted with an RFID reader antenna wired to one of BarMaxx’s proprietary readers. The ID number and the bottle’s weight—calculated to 4/1,000th of an ounce—is stored in the BarMaxx software. Every time a bottle is poured, the weight is reduced, and the software can then calculate the exact amount of that pour, based on the reduced weight.
Recipe data for the drinks that the company sells is stored in the BarMaxx software, which is integrated with the bar’s POS data. When a staff member rings up a particular drink, such as a cosmopolitan, the software knows exactly which liquors are included in that drink and what the quantity should be. If the pour, prior to that sale, was higher or lower than the expected amount, a discrepancy is stored in the software. In addition, if cameras are in use, BarMaxx software stores the video recorded at the exact time that the pour occurred, which bar managers can then view, along with data regarding the pour discrepancy.
The software can also issue an alert indicating when inventory needs to be restocked. In addition, bar managers can use the software’s business analytics, such as tracking how fast a certain product—Grey Goose, for example—is selling, the times at which sales are greatest, or how profitable a wedding or other special event was. It can also determine how much revenue was earned from a single bottle of liquor, and compare that information against the product’s cost.
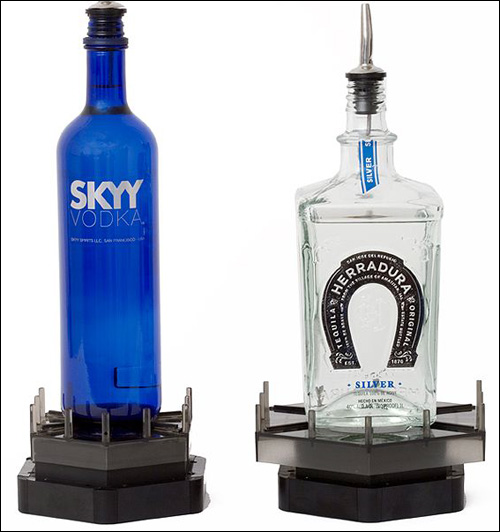
Managers can view inventory levels in real time, by accessing the software and selecting the “Bar View” option. This view indicates the exact level of liquor within each bottle in use at the bar, as well as quantities stocked in the storeroom.
The primary benefits, Zevgolis says, are assurance that every drink is poured correctly, and that liquor is not wasted. Shrinkage costs bars more than 15 percent of their revenue on average, he estimates, adding that restaurants using the system have lowered their shrinkage level down to approximately 3 percent. Moreover, he says, using the system allows bars to cease assigning workers to manually conduct storeroom inventory counts in an effort to avoid the risk of running out of a particular product.
Steve Haas, City Hall Restaurant’s owner, says he has been using the BarMaxx system since opening the establishment in mid-2011. The software provides him with data related to expected liquor consumption, based on POS reports, in addition to actual liquor consumption, based on weight data culled from the RFID readers. In the event of a discrepancy, he says, he can review the details, determine who was on shift at the time, and discuss the matter with those employees. In that way, Haas explains, the system not only catches errors, but also acts as a deterrent, since the staff knows the technology is monitoring their liquor pours.