Berliner Wasserbetriebe, the utility company that provides the city of Berlin and its surrounding areas drinking water and sewage services, is tagging 62,000 pieces of machinery, equipment and other valuables with RFID tags. Later this year, the company plans to begin using the tags to speed up and simplify its yearly inventory of capital goods.
Angelika Neumann, head of the firm’s inventory process, dreamed up the RFID application to make her job easier. Her team and the company’s subsidiary, Berlinwasser Services, developed a detailed plan for the RFID project, then presented it to the four-person management board, gaining its approval. The company has since attached RFID tags to 12,000 of the 17,000 specific locations at which tagged machinery and other assets will be inventoried. These location tags are attached to such items as doorframes and control boxes in the facilities where items are stored. The tagging of individual pieces of equipment and assets will begin later this year. In total, Berliner Wasserbetriebe will use almost 80,000 Smart-tec 13.56 MHz passive tags that comply with the ISO 15693 standard.
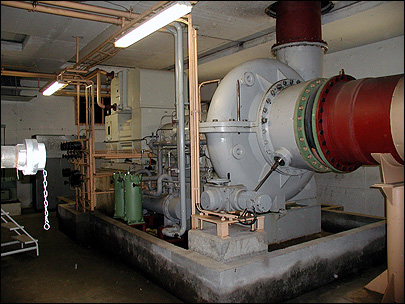
Berliner Wasserbetriebe serves 3.8 million people, has around 5,000 employees and reported sales of about 1.12 billion euros ($1.48 billion) in 2006. The company operates nine treatment plants, a 7,857-kilometer network of fresh-water canals, a 9,360-kilometer network of sewage canals and 2,300 water-testing sites. Each year, Berliner Wasserbetriebe must account for its capital goods so it can write off the depreciation for each piece of equipment. It takes a team of about 140 people the entire year to manage the inventory and perform such related tasks, including controlling, purchasing and bookkeeping. The company considered tagging items with bar codes but decided against it, since much of the machinery is outdoors and exposed to dirt and mud, which can negatively impact the ability to read bar codes.
Neumann analyzed the inventory process to locate its weak points—that is, those steps in which errors were frequently made or that needed a particularly long time to complete. In the soon-to-be retired process, workers take lists generated by an SAP R/3 system and inventory each piece of equipment by hand. They then create other forms that document which items need to be transferred to different departments or replaced. Results of the inventory are submitted to a manager, who approves them with a signature. Eventually, the information is entered back into the SAP system. The entire procedure’s potential for manual errors is high. “This does not lead to an optimal process,” Neumann says.
The new system aims to shorten and simplify the inventory process, while providing Berliner Wasserbetriebe a better overview of the condition and location of its capital goods. The list of items to be inventoried will be transferred from SAP R/3 to a database workers will use to conduct inventory. With a faster inventory process, items can be put to use in other divisions more quickly, and the overall facilities management process can be performed more efficiently.
Berliner Wasserbetriebe chose two types of RFID interrogators: one for areas in which explosions have the potential to occur, and one for non-dangerous sites. For the latter, the company bought 80 Workabout Pro readers from Psion Teklogix that run on Windows CE and can read bar codes. It also purchased 30 ecom i.roc handheld readers from SAT, which conform to the European Commission’s ATEX directive, which stipulates requirements for equipment used in explosive areas.
Workers in all departments will be responsible for tagging and inventorying the items in their own divisions after receiving training on where and how to tag, and how to interrogate the tags with the handhelds. If problems arise, personnel will be able to call on the inventory team for assistance.
In the first step of the reading process, a worker will interrogate the location tag to identify the site of an item being inventoried. This is required because, for instance, there are many identical items without serial numbers in use at the utility desks—and the company wants to be able to match the particular class of item to its location. In the second step, the worker will read the tag on the desk, the computer or the machinery at that location. Once the data is collected on the handhelds, the computer will be taken to a docking station. Data will be transferred and sent to the database and SAP system. Managers will sign off on the work electronically, and the database will be updated.
Smart-TEC developed three different tags, as per the company’s specifications, then tested them with various adhesives and in different environments (including dirty environments and areas with strong ultraviolet light). Each tag carries a bar code that matches its unique ID and contains information about the serial number, if appropriate. The standard tag measures 35 by 20 millimeters. The second tag, measuring 45 by 25 millimeters and covered in protective plastic, is designed to work in a dirty environment. The third tag, also covered in plastic, measures 45 by 25 millimeters and is designed to work on metal items.
The company’s IT subsidiary managed the technical side of the application and only brought in outside experts when it needed special tests performed on the different RFID tags. Neumann declined to give any figures about the company’s planned return on its investment, but says an ROI has been calculated and submitted with the original plan.