Disasters are inevitable, no matter the industry—whether it’s unexpected equipment failure, a major weather event, a security hack or some other crisis that affects business continuity, the unexpected happens every day. While we can’t predict every disaster before it happens, we can be proactive in maintaining equipment health. Technology enhancements around the Internet of Things (IoT) and data analytics enable service companies to preemptively get ahead of problems, minimizing—or even averting—the impact felt by customers when disaster does eventually strike.
While it may sound simple, monitoring thousands or even millions of pieces of equipment and identifying errors before they occur is a complex science that can quickly become overwhelming. To help simplify the process, I’ve broken it up into two distinct phases: data collection and data analysis.
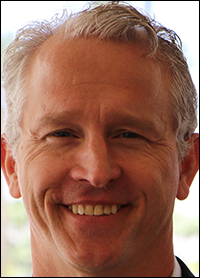
Data Collection: Understanding Which Information Matters
IoT sensors allow for large volumes of data to be collected and stored, providing companies with insight into equipment health, performance and failures. Every unit can generate hundreds of thousands of data points every minute. The challenge at this stage is to figure out how to organize and prioritize all this data. Performing data analytics on all this information is not feasible, nor is it an efficient use of resources since some of the data being collected holds little value in determining asset health.
Companies need to consider what data to prioritize so that they can more quickly identify maintenance needs. For instance, a telecommunications provider monitoring a cell tower may be tracking the volume of calls being picked up through that specific tower, but call volume is not indicative of how well that tower is performing. However, if the telco is alerted to an increase in dropped calls associated with that tower before the problem swells, they may have an opportunity to pinpoint and rectify the issue early. Now consider a massive storm that is expected to hit where this cell tower is located—being able to repair and address tower issues in advance of the storm minimizes maintenance efforts in the face of this weather disaster.
Data Analysis: Establishing Maintenance Indicators
Once data is collected and the key monitoring metrics are defined, analytics are applied in order to convert the data into actionable, useful information. Analyzing historical data, particularly around equipment failures and past service activities, allows service companies to identify patterns that might indicate a future error.
For instance, for a utilities company, temperature is one of the most widely measured parameters in a power plant because overheating can cause serious damage to equipment and can pose dangers to service professionals working to repair the equipment. By looking at past maintenance activities and patterns in temperature changes, companies have the insight needed to schedule preemptive maintenance when temperatures rise to levels that have led to failures in the past.
We’re seeing more and more applications of IoT technology in the service industry with sensors connecting devices and equipment. Even fitness centers have started connecting its equipment to avoid broken machines and disappointed members. But with greater connectivity comes greater responsibility; organizations must leverage these enhanced capabilities to transition from reactive to proactive service programs to address breakdowns before they occur—ultimately maintaining customer satisfaction, today’s number-one business priority.
Steve Smith is the VP of strategic industries at ClickSoftware. He has more than 15 years of experience defining and delivering mobile workforce-management solutions covering vertical markets that include telecommunications, utilities, insurance, home services, medical equipment, capital equipment, and oil and gas operations. He aids service organizations to optimize the use of their field resources, improve operational awareness, streamline process and establish controls, while ensuring flexibility and variability are enabled within their operations. Prior to his current role, Steve managed ClickSoftware’s global solution consulting team, exposing the benefits of mobile workforce management to new users and helping increase the benefits of existing users across the globe.