It’s one thing to develop a cool new RFID product. It’s another to make it useful, easy to deploy and inexpensive enough to adopt. Both Phase IV Engineering and Smartrac sensed a need and did just that.
Phase IV’s RFID Sensor Reader addresses a challenge manufacturers have faced: how to integrate an RFID reader into an assembly plant’s machinery, a conveyor system, or an industrial computer known as a programmable logic controller (PLC) that a factory typically uses to automate processes on an assembly line.
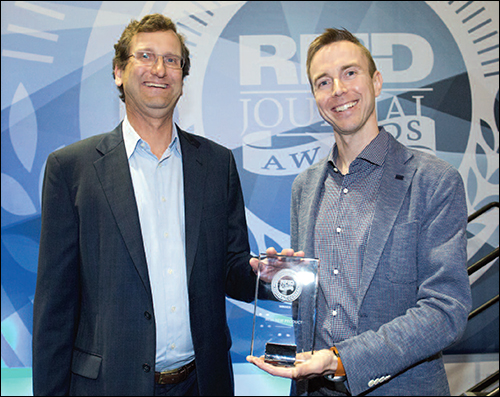
“I had about six projects last year where we had a client that wanted to use RFID in a control system, and every one of them walked away because of the problems of implementing an RFID reader,” says Phase IV’s CEO Scott Dalgleish. The trouble, he explains, is that RFID readers aren’t designed to communicate with the PLC input modules that accept signals from sensors or other devices and convert them into a form that can be used by the PLC’s CPU.
A common type of PLC input module, Dalgleish says, is an Allen Bradley analog input card that accepts a signal in a format that varies from 0 to 5 volts. Say, for example, a factory wants to install a passive RFID temperature sensor tag at four different locations on its assembly line. The analog input card has multiple terminals for accepting signals, and the data from each of the four sensor tags must be routed to its own dedicated terminal on the card. So an RFID reader first needs to read each tag to capture the sensor’s temperature measurement and, based on the temperature reading, convert that measurement into voltage of 0 to 5. The reader must then route that voltage signal to the PLC input module terminal assigned to that particular sensor.
“And there are user-configuration issues,” Dalgleish says. “How often do you want the reader to read the temperature sensor and feed it to the PLC? Is it once a second? Is it once an hour? What happens in an error condition? So those are all problems that need to be solved to bring RFID sensing into the industrial environment.”
To achieve this goal, Phase IV developed the RFID Sensor Reader, an EPC Gen 2 RFID reader with eight terminals for analog output. “Inside the black box is a computer with every I/O you can think of—4 to 20 milliamps, 0 to 5 volts, USB, Ethernet, a cellular modem,” Dalgleish says. “There are a lot of problems that only RFID sensors can solve once you get the data to the control system in an efficient manner. And that’s what we’ve done here.”
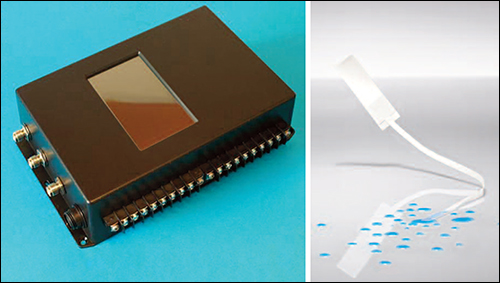
Smartrac’s Sensor Tadpole, an on-metal passive ultrahigh-frequency RFID tag that can detect the presence of moisture, also solves an intractable problem: how to easily and cost-effectively identify water leaks in hidden places, such as within weatherproof electrical boxes, sealed packages and cabinets, behind walls, or inside a car’s electronics bays, cabin and trunk (see Water Leaks in Cars Can’t Hide From RFID). The Sensor Tadpole communicates with off-the-shelf EPC Gen 2 readers and requires no custom commands.
“Sensor Tadpole has really opened a whole new application for RFID,” says Lauri Hyytinen, head of Smartrac’s automotive segment. “For the first time, we have reliable water detection at a really reasonable cost for automotive and similar applications.”