In an effort to eliminate the paperwork that follows products through the assembly process in the manufacturing industry, RFID technology company Omni-ID has released View 10, an 8-inch by 11-inch battery-powered, multiprotocol, multifrequency RFID tag that combines a 10.1-inch electronic-paper display screen with an active 433 MHz RFID tag (compliant with the ISO 18000-7 standard), a passive ultrahigh-frequency (UHF) RFID tag (compliant with the EPC Gen 2 and ISO 18000-6C standards), a sensor for receiving data via infrared (IR) signals and a Wi-Fi transceiver. The View 10 can be attached to an automotive engine or other product on an assembly line, enabling management to not only locate that item within a facility based on Wi-Fi-based location data, but also track its status based on RFID or IR reads performed at assembly stations. At the same time, operators providing the assembly can automatically view instructions related to the work they should perform on each specific piece displayed on that tag’s screen, sparing them from having to flip through pages of a “build book” that historically follows an object being assembled.
The View 10 tag was designed during the past 18 months for automotive manufacturers or other large capital goods manufacturing companies. One of its first customers, Detroit Diesel Corp. (a division of Daimler Trucks North America), has been piloting the technology during the past year, and is now proceeding to deploy the solution throughout its facility. At the same time, says Ed Nabrotzky, Omni-ID’s CTO, the technology is being piloted by another unnamed automotive manufacturer, and Omni-ID is in discussion with a pharmaceutical company interested in using the tag to monitor drug manufacturing.
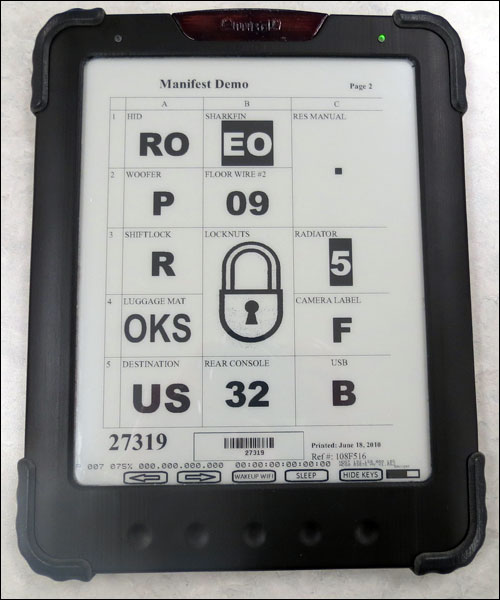
The View 10 is the largest member of Omni-ID’s ProVIEW product line (the currently available View 2, View 3 and View 4 models were launched in early 2013), but Nabrotzky says customers had suggested they would benefit from a tag with a large enough screen to replace the sheets of paper or booklets that typically follow an item through production, to instruct operators regarding what they should do.
The new tag features 25 megabytes of memory (upgradeable upon request), which is sufficient for approximately 168 visual pages of text. The device can be mounted via a hook or magnet, or follow an item without being physically attached to it. Its black-and-white bistable screen draws no power as it displays data, enabling the device’s batteries to last for about two weeks before requiring a recharge.
The problem with paper documents is not only the cost, Nabrotzky says, but also their inability to be easily modified in the event that assembly specifications change. For example, in the case of Detroit Diesel, the books that list instructions related to the assembly of very specific products are printed by a third party 48 hours ahead of planned assembly. An engine could move through as many as 60 stations of assembly and work, guided by the build book. When copies of the book arrive in crates, personnel must take them out and match each book to the corresponding engine, according to serial numbers on those engines, and then use a marker pen to make any changes (if there have been any) to the instructions. During assembly, operators at each station must flip to a certain page to read the appropriate instructions. The books are then discarded at the end of the assembly process, resulting in unnecessary waste as well.
The View 10 is designed to act as a real-time location system (RTLS) tag for tracking and tracing an item through the assembly process. In addition, it serves as an electronic book that automatically displays pertinent information to operators, and enables them to indicate any changes or problems.
Encased in rugged plastic, the View 10 is intended to be much tougher than a tablet—with a Wi-Fi transmitter to send and receive location or other data via a user’s Wi-Fi network. At Detroit Diesel, an EPC Gen 2 RFID reader is installed at each workstation that transmits a unique ID number to the tag. Nabrotzky says any UHF EPC RFID reader can operate with the View 10. The tag then forwards that data to the ProVIEW software, residing on Detroit Diesel’s server, which determines—based on the station ID associated with that particular reader, as well as the engine’s tag ID—what page of instructions will be needed, and automatically displays that information on the tag screen. At the same time, the software stores the tag’s location data, based on the location of the reader that interrogated that tag. If the employee is wearing a badge containing an EPC Gen 2 RFID tag, the reader could also send the badge’s ID to the ProVIEW software.
This solution could also utilize IR emitters instead of EPC Gen 2 UHF RFID readers to accomplish the same process of location identification and the opening of an appropriate text page for each station, Nabrotzky says. The View 10 includes a 38 kHz IR receiver designed for long-burst codes, he adds, and is adaptable to other IR frequencies. Omni-ID will supply a custom IR emitter for initial installations. However, he notes, the company can configure the View 10 for other IR emitters, as demand requires.
If an operator experiences a problem or has a request while working on a tagged item, such as “I need more blue paint” or “I need welding rods,” he or she could press one of the five buttons built into the View 10’s plastic case, each of which is linked to a specific request based on that station’s instruction. Once a button is pressed, the ProVIEW software can then forward an alert to the appropriate individual to replenish that operator’s materials. The View 10 can also display alerts to the assembly workers. For example, if the item being manufactured ends up at the wrong station—for instance, if it is delivered to a painting area before assembly is complete—an alert would be displayed on the tag’s screen.
Once the item is assembled, it can be removed and reused on another product, while a history of the assembly, along with the operators who worked on it, is stored in the ProVIEW software.
If a user opted against employing the Wi-Fi network at its facility, it could instead rely on the View 10’s active 433 MHz RFID tag, with 433 MHz readers transmitting the tag’s location or other data to the back-end server, without overloading the Wi-Fi network.
There are several advantages that the View 10 offers over a simple tablet, Nabrotzky reports. Not only is it more rugged than a tablet, but it provides location-based data, which a tablet would not be able to do unless the user had also installed specific indoor-positioning software. The View 10 is more expensive than a basic tablet, he adds, but Omni-ID has calculated that companies like Detroit Diesel could expect a return on investment within nine to 14 months, based on the elimination of paper costs alone. In addition, it provides further benefit by saving labor time and storing data regarding each assembly.
The View 10 tag is a candidate for the Best in Show category of the 2014 RFID Journal Awards, which will take place at this week’s RFID Journal LIVE! conference and exhibition, being held on Apr. 8-10, in Orlando, Fla. The company will demonstrate the technology at the event, in its booth (436). What’s more, Detroit Diesel will discuss its experiences with the technology at the conference, during a breakout session.