Xerafy has announced its most rugged tag, the Roswell. The new tag is made with a passive EPC Gen 2 RFID chip, fully encased in stainless steel and capable of being welded directly onto a metal item. While Xerafy initially developed the Roswell tag as a solution for those seeking to track metal items used during surgery, such as tool trays, the product also works on gas cylinders or valves. Sample versions are currently being tested by companies in both the health-care and oil and gas industries.
At present, the Roswell tags are only being offered as samples for testing; however, they are expected to be made commercially available for orders in large quantities in April 2014, coinciding with this year’s RFID Journal LIVE! conference and exhibition, being held on Apr. 8-10. The new tag is also part of a solution being launched by RFID company OATSystems (a division of Checkpoint Systems) for tracking surgical instruments to automate such supply room processes as cleaning and sterilization, and to reduce preventable incidents—such as the loss of a tool during a surgical procedure—as well as improve patient care.
The Roswell is Xerafy’s most rugged tag, the company reports, with an IP69K rating for withstanding high pressure and extreme temperatures. “We’ve never had a product like this one,” says Evelyn Ong, Xerafy’s sales director. The entire tag is made of stainless steel, which it employs to act as an antenna, thereby requiring nothing more than an EPC Gen 2 ultrahigh-frequency (UHF) RFID chip in the center of the tag.
Xerafy has been developing the solution for approximately nine to 12 months, in an effort to create a tag that can sustain the harshest environments while providing a consistent read range. The requirements expressed by its customers had included not only that the tag survive harsh conditions—sterilization processes, for instance—but also that it not come loose from an item to which it is attached. With the use of adhesives, there is always the risk that a tag, no matter how tough, could still be knocked loose. When it comes to health-care applications and tools used around patients during surgery, Xerafy indicates, it is especially critical that a tag never be detached from something like a surgical tool.
“Metal is still the best way to connect a tag to metal,” Ong states. Since the tag is entirely composed of metal, she says, the Roswell tag could be welded to another metal object, thereby providing a very durable connection.
Although the use of metal as an antenna is not new (see The Object Is the Antenna and RFID License Plates: A Successful In-Metal RFID Application), Ong says previous versions of metal tag antennas have had variable read results. “We wanted to try to make a tag that could be consistent,” she explains. The result, the company reports, is a tag with a 5-meter (16.4-foot) read range over a 180-degree orientation. In addition to being attachable via welding or soldering, the tag could also be fastened by bolts, tie loops or adhesive.
The 1.1-inch-wide circular tag is still too large to be applied to smaller surgical tools, Ong notes. However, she says, the company is currently developing a smaller version of the Roswell that she expects will be released sometime in the future.
“The health-care industry has a very harsh environment,” Ong says. Surgical tools, trays and kits pass through cleaning processes and autoclaves at very high temperatures throughout hundreds of cycles. Since the tag can sustain such an environment, Xerafy claims, it is also suited for the oil and gas industry, in which high and low temperature and pressure levels, as well as the presence of chemicals, can destroy tags that are not sufficiently robust.
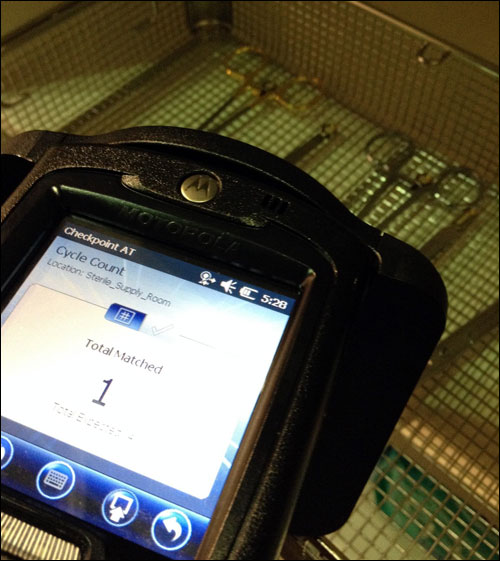
Currently, sample versions of the Roswell tag are being tested by several hospitals, as well as at laboratories for the oil and gas industry. According to Ong, Xerafy has been contacted not only by health-care companies looking to track surgical trays at medical facilities, but also by device manufacturers that produce surgical tools and would like to sell them with tags already attached.
In addition, Ong says, oil and gas firms have contacted Xerafy about the possibility of using the tags to track valves, as well as gas cylinders that have a lifespan of 10 years or more, and thus require a very durable tag that can last just as long. “The response [to the testing of samples] so far has been very good,” she states.
The Roswell tag is anticipated to be more expensive than standard Xerafy tags, due to the stainless-steel material of which it is made, though Ong declines to specify a price. The cost will be comparable to that of Xerafy’s other specialty tags, she notes.
This month, Xerafy also announced that it has teamed up with OATSystems and Motorola to provide a solution for tracking surgical tools, trays and kits within operating rooms and supply areas. The system consists of OATSystems software and integration services, as well as Xerafy tags and Motorola readers.
“We developed this solution based on customer requests,” says Chris Forgione, OATSystems’ senior director of asset tracking, “and plan to release it as a packaged solution, along with other asset-tracking applications, in the first half of 2014.”
According to Forgione, OATSystems developed the solution, using hardware and expertise from Xerafy and Motorola, based on a trend that all three companies had identified regarding RFID and real-time location system (RTLS) health-care applications during the past few months. “Although many hospitals are using RFID RTLS for tracking the location [and/or] condition of capital assets,” he says, “they are also looking to automate critical hospital processes, such as instrument sterilization and kitting, and dispensing medical supplies.”
By automating surgical supply room processes with RFID, Forgione explains, “a primary care provider can ensure only sterile, maintained instruments are used in surgery, helping to reduce preventable incidents and improve patient care.”
Customers will be able to utilize the solution to confirm that all of the correct instruments and supplies are in a surgical kit, they they are sterile, and that all of them have been properly maintained (sharpened and within duty cycle). The software will also monitor whether all items are still within their useful lifespan, such as ensuring that medications have not expired. “This improves the quality of patient care and also optimizes surgical procedures, since no time is wasted replacing tools or looking for new ones,” Forgione says. “We have heard from hospitals that the more efficient they are in preparing for individual surgeries, the more surgeries they can perform, so efficiency not only leads to reduced waste, but increased profit as well.”