Engineers in Microsoft‘s research division> have developed an automatic-identification technology known as InfraStruct, using passive tags operating in the terahertz (THz) band. Instead of encoding data onto a silicon chip, as is typically the case for passive RFID tags operating in the low-frequency (LF), high-frequency (HF) or ultrahigh-frequency (UHF) radio frequency (RF) bands, the InfraStruct system involves building a unique shape or hollowed section directly into a structure, with an ID number or other data physically represented in that shape or section.
The term terahertz refers to electromagnetic radiation falling between microwaves and infrared—that is, between 300 GHz and 3,000 GHz (0.3 THz to 3 THz), with wavelengths ranging from 0.03 millimeter to 3.0 millimeters (0.001 inch to 0.1 inch). The UHF band, meanwhile, ranges from 300 MHz to 3 GHz, with wavelengths from 10 centimeters to 1 meter (3.9 inches to 3.3 feet).
The InfraStruct concept, still in the prototype stage only, includes a unique method of building a tag into a three-dimensional printed plastic object, as well as a terahertz scanner that transmits an optical-like radiation into the item that is reflected back to the scanner. Software then measures the response of the reflection received, thereby identifying the unique item based on that measurement.
Karl D.D. Willis, formerly a research intern at Microsoft Research while a Ph.D. candidate at Carnegie Mellon University, and Andrew D. Wilson, a principal researcher at Microsoft, developed the technology throughout the past several months, hoping to enable a unique identification method as an alternative to bar codes and radio frequency identification. Bar codes, they explain, must be placed outside an item, and thus create an aesthetic problem. Adding an RFID tag (with a silicon chip and antenna) to a molded object made only of polymer, on the other hand, would disrupt the manufacturing process used to form that item.
With InfraStruct, a 3D printer could be used to create objects based on computer-controlled digital fabrication. Those items could differ slightly from one another, due to slight changes in the digital design, creating an opportunity for the unique identification of each of otherwise seemingly identical objects. Such identification can be useful during inventory tracking, logistics or gaming applications, but could be used in the future to help a robot recognize specific objects it seeks.
With InfraStruct (the word, derived from Latin, means “below structures”), users create an identifier (or tag) inside an object digitally by, for example, generating a pattern of bubbles in a layer of material used to fabricate the object itself. That shape or pattern is then stored in software to indicate that item.
The THz transmissions can penetrate plastics, papers and textiles. THz signals are transmitted and received optically (like light and infrared), using imaging technology similar to the complementary metal-oxide-semiconductor (CMOS) chips commonly found in digital cameras.
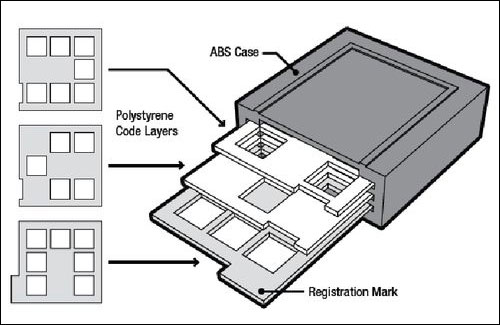
Historically, the THz band’s most common application has been the detection of imperfections in a material, such as the foam used on a spacecraft, since it reflects the presence of flaws—voids and cracks, for instance—back to a user.
InfraStruct takes advantage of this concept in a different way. As a THz emission passes through a material, some of that radiation is reflected back, first as it passes through the enclosure material and again upon entering the variation, based on the specific tag built into that object. In this way, it can reflect information back to the user, not about a defect, but about a shape or design deliberately embedded in an object. Varying the material structures within that item can create reflections encoded with unique binary information that the InfraStruct software could use to identify that object.
Willis and Wilson have created five prototype tag designs, each scanned with a different imaging configuration. The designs include unique tag locations within an object, differing tag geometries—how it is positioned and oriented inside the object—or the manufacture of a series of layers with shapes and patterns that can be identified via the THz scan. The two men also developed a variety of manufacturing methods by which the identifiers could be embedded in the object, including the use of additive fabrication with InfraStruct tags added to hollow internal areas of the item, or a subtractive method in which laser or vinyl cutters are used to remove raw material from the form in order to create a particular shape.
The researchers employed several off-the-shelf THz emitter-receivers, including Picometrix‘s T-Ray 4000 model. The team has also developed the software that analyzes the transmissions reflected from a scan of each item, and then links the results to a specific object.
However, Willis says, commercial use of the technology may take some time to begin. Most current fabrication techniques would not easily accommodate the tag creation processes, he notes, adding that scanners are currently expensive, but that prices would drop if they were used in large volumes. “I could see this going to market in a basic form very quickly,” he states, “but it is going to be sometime before the price point drops to a level that is accessible for a larger market.”
Willis and Wilson presented their findings this week at SIGGRAPH 2013, an international conference and exhibition focused on computer graphics and interactive techniques, in Anaheim, Calif. According to Willis, the audience consisted primarily of individuals in the graphics technology community.
Uses cases could simply involve the tracking of goods moving through the plant where they are manufactured, Willis says, or at a warehouse or store. The technology could also be used in customized game accessories, allowing a gaming console to identify a particular accessory, thereby personalizing the user experience. In the future, he adds, robots could utilize the technology to recognize specific objects.