Troy Design and Manufacturing Co. (TDM) is expanding an RFID-based solution that it installed with the opening of its new plant in Chicago, to further reduce the amount of labor time employees spend manually tracking work-in–progress (WIP) on paper. Three years after installing the system at the new plant—which converts various vehicles from Ford Motor Co. into Police Interceptor models—TDM’s management reports that the solution saves time, as well as enabling personnel to focus on the value-based work at hand.
When the plant opened in early 2011, it included a passive ultrahigh-frequency (UHF) RFID-based system provided by Lowry Solutions, using RFID readers and antennas from Motorola Solutions and RFID middleware supplied by Austrian company 7iD Technologies to make the identification of products through the assembly line a hands-free process. TDM’s Chicago Modification Center converts more than 150 Ford Explorer and Taurus vehicles daily into Police Interceptor versions for Ford Motor Co., its parent firm.
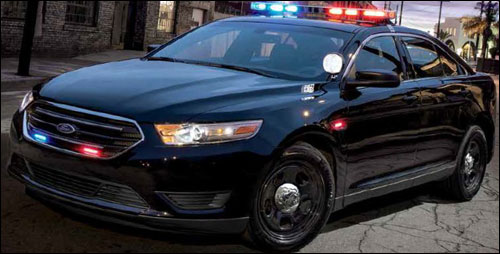
Until 2011, third-party factories modified Ford’s vehicles for police work. Ford launched TDM so that it could to keep the work in-house and opened the new plant, which is dedicated to converting vehicles produced by Ford’s Chicago car factory. TDM needs to track every car through four assembly lines, each containing approximately 10 workstations, where a variety of processes are carried out, such as bullet-proofing the doors, installing lights and incorporating other modifications specific to a customer’s particular needs.
Since each vehicle requires its own set of unique options based on its work order, workers need to know which processes should be provided for that vehicle as it enters their station. With a paper-based solution, an order sheet would travel with the vehicle, and workstation operators would have to look at that sheet, then manually access a book in which they could look up the specific processes being requested and ensure that they were appropriate for that specific vehicle and order. This system, which was tested before the plant opened, was extremely labor-intensive, says Lee Murray, TDM’s director of technology. The company also considered having workers scan a bar code on each vehicle, he adds, but tests showed that this, too, was inefficient, since it required staff members to stop what they were doing and scan the bar code before determining their next process step.
The RFID solution consists of Motorola’s FX9500 readers, each with up to four AN200 antennas installed around each of the 40 workstations, as well as several exit points at the end of the assembly lines. The collected read data is managed via Lowry Solutions’ WIP manufacturing software. Because the real-time vehicle-tracking system at Ford’s Cologne-Niehl plant is utilizing 7iD’s RFID middleware, TDM opted to deploy 7iD middleware as well for its own deployment.
First, TDM receives notification of vehicles en route to its plant, along with their respective work orders. As each vehicle arrives, a TDM worker uses a Zebra Technologies R110xi4 RFID printer to print and encode a 4- by 6-inch adhesive Intermec Kimdura RFID label containing an Avery Dennison AD-843 RFID inlay. The label is attached to the car’s back windshield, and the system links the tag’s unique ID to the vehicle’s work order, including instructions, a bill of materials and the vehicle identification number (VIN).
As the vehicle enters a workstation, its label’s passive EPC Gen 2 UHF RFID inlay is interrogated, and the work order data is then retrieved from the management software and displayed on a screen at the station. Operators then simply view that order and follow its instructions. “I really don’t want the operators thinking about doing non-value-added stuff,” Murray says. “I think that’s one of the key advantages to RFID—it just happens,” since employees can view data without having to look it up manually.
Management then has a record of how long a particular vehicle spends at each station, as well as its exact step along the assembly process at any given moment.
Once a vehicle reaches the end of the assembly line, its RFID tag is again read as the car leaves the plant floor, thereby updating its status in the software. The vehicle is moved through a leak booth to ensure that no breeches were created during the assembly process, and then to an inspection station, where another RFID reader captures the tag ID number as workers verify that all tasks have been properly completed. Once this is done, the car approaches the final read point, located at a barrier gate, where the tag is read once more. If the software confirms that the order is complete, the gate opens to permit exit to the yard outside. After the vehicle has been fully converted into a Police Interceptor unit, TDM can provide Ford Motor Co. with a vehicle receipt, production progress or shipping update.
By using the technology, Murray says, TDM found that it could eliminate five to seven seconds from each workstation process compared with the amount of time required to perform bar-code scans. As a result, he notes, the company has managed to outperform its expected production rates.
In the future, Troy Design and Manufacture hopes to add RFID to its off-line stations as well. For example, vehicles are vinyl-wrapped (an alternative to painting for changing a car body’s color and adding graphics) separately from the assembly lines, and operators at those locations scan bar-code labels attached to the vehicles in order to create a record of services provided. By the end of this year, Murray reports, RFID readers are expected to be installed at these locations as well.
Motorola is supplying its RFID readers for a growing number of work-in-progress applications in the automotive, electronics repair and consumer hard goods manufacturing sectors, according to Mark Wheeler, Motorola Solutions’ director of industry solutions, to provide WIP tracking and warehouse management in industrial applications. “We’re seeing a lot of interest in these kinds of solutions,” he says, to improve work-in-progress data accuracy, reduce labor times and increase production output rates.