When Volkswagen drivers in and around Mexico City require replacement parts for their vehicles, they rely on a network of VW dealerships. And those dealers rely on a Volkswagen plant in Puebla, located approximately 75 miles outside the city, from which they order these parts.
As part of a larger effort initiated by Volkswagen de México in order to improve its spare parts distribution process, cardboard boxes used for shipping spare parts to dealers are being replaced with reusable plastic containers fitted with RFID tags. The application has enabled the Puebla plant to lower its yearly expenses associated with parts distribution by 30 percent, through reduced packaging costs and an automated shipment-verification process, according to Juan Manuel Rodríguez Flores, sales manager of Grupo Hasar, the RFID systems integrator that deployed the solution for the plant.
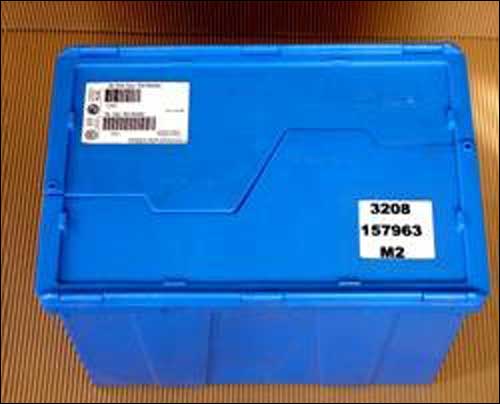
In late 2007, VW de México enlisted Grupo Hasar to help devise a means by which it could reduce some of the manual steps required to track parts shipments headed to its network of dealers. After carrying out a pilot project to test a solution, the company rolled it out permanently in June 2008. Now, VW de México and Grupo Hasar are working to expand the system to additional factories throughout Mexico.
When a dealership submits a parts order with the Puebla plant, the SAP enterprise platform planning software used by VW captures and forwards the request to the factory’s warehouse management system (WMS). Employees at the plant take the orders and a forklift truck into the warehouse in order to collect all of the parts needed to fulfill them. They utilize handheld scanners to read the bar code attached to each part, then bring the selected parts to a packing table. (At present, Flores says, RFID tags are too costly to replace the bar-code labels used by VW de México to identify the individual parts. But if tag costs drop significantly in the future, the Puebla plant would likely move to RFID tags in order to further automate parts identification.)
At the packing table, another employee uses a handheld bar-code scanner to read the bar code on a label attached to a reusable container. That label also contains an embedded RFID tag—an Alien Technology Squiggle passive UHF EPC Gen 2 tag. The same unique ID number is encoded to both the bar code and the tag. After collecting this ID with his handheld scanner, the worker scans the bar codes on each part he places in the container. Once he finishes, the handheld computer associates the parts with the container ID, then forwards this data to the WMS.
In the warehouse management software, the order status is updated to reflect that the order has been packed. Then, a Motorola XR440 RFID reader, mounted at the loading dock, captures the ID encoded to the RFID tag as each container is loaded onto a truck bound for the dealers that placed the order. This information is also forwarded to the WMS, which marks each order complete and shipped, noting the date, time and dock location from which it was sent. When the truck delivers an order, the dealer reads the bar-code label on each container, which is logged in the Web-based WMS, so that the Puebla plant knows when each container was received.
Today, only 30 percent of the VW dealers that order parts from Puebla are receiving the plastic containers—the others still receive orders in cardboard boxes that do not carry RFID tags. The participating dealers receive two shipments of parts from the Puebla plant per week, making the return process simple: When a new shipment arrives at each location, that dealership swaps the full containers for the empty ones.
As the empty containers are brought back to the Puebla warehouse, they are moved through a portal RFID reader, then each is checked back into the plant’s stock of containers. If records show that a dealer has failed to return a tagged container within 10 days of delivery, it is charged a late fee.
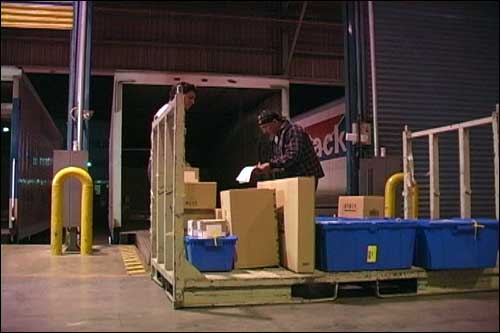
The remaining 70 percent of the dealers receive parts shipments less regularly, and from trucks that are not used solely for runs between the Puebla plant and the dealerships. According to Flores, the factory is currently seeking a third-party logistics provider that will be able to pick up empty containers from these remaining dealers in a manner that is cost-effective.
To date, the plant has deployed 16,000 RFID-tagged reusable containers. In addition, it has 350 metal carts to which RFID tags had been attached during the pilot period, which are still being utilized. The carts are used for transporting very large or oddly shaped parts that do not fit into the containers. Mounted on the carts are Intermec passive EPC Gen 2 tags embedded in a protective housing—one that provides a buffer space between the tag and the cart’s metal surface, because the latter could otherwise interfere with the RF signal, thus making the tag difficult to read.
Aside from saving the Puebla plant from paying the ongoing costs of cardboard containers to ship parts, Flores says, utilizing the reusable containers has significantly reduced the amount of waste packaging among the VW dealers receiving them. These dealers, he notes, sometimes reuse the cardboard boxes for internal purposes at their locations; otherwise, they would be trashed because most sites lack established recycling systems.
Based on the benefits of the new tracking system—reduced packaging costs, as well as a faster shipment verification system (capturing the RFID container tag, versus manually scanning its bar code as each container is loaded onto trucks)—Volkswagen de México wants to replicate the system at its parts distribution plants in Guadalajara and Monterrey, starting later this year. Eventually, Flores says, VW’s U.S. parts distributors may also employ this RFID-based system for tracking parts shipments.