Following more than five months of research conducted last year using a closed-loop conveyor at their laboratory, researchers at the University of South Florida Polytechnic were able to boost item-level RFID tag read-write accuracy from approximately 80 percent to 99.5 percent during a pilot of the technology being carried out by Cephalon Pharmaceuticals. At the lab, the research team was able to create a more effective RFID system by adjusting the settings within the reader software, repositioning the reader antennas and testing the effectiveness of various makes and models of tags and reader antennas.
After deploying the solution at the manufacturing plant operated by Cephalon (which has since been purchased by Teva Pharmaceuticals), the researchers determined that laboratory-testing an RFID solution, prior to its installation in a real-world setting, can increase that system’s effectiveness, according to Ismail Uysal, an assistant professor at USF Polytechnic and the director of the school’s RFID Center for Applied Research.
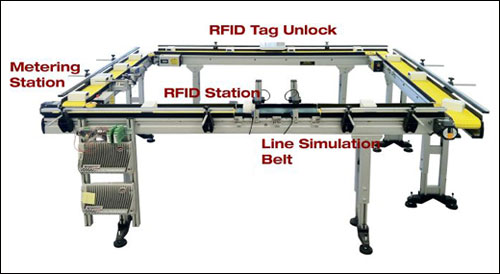
Before the USF Polytechnic researchers began working with the pharmaceutical company, Cephalon had already begun piloting EPC Gen 2 passive ultrahigh-frequency (UHF) RFID tags to be encoded, encrypted and then read as the firm packaged one of its pharmaceutical products, Fentora (a painkiller for cancer patients). Fentora was selected for the pilot due to its high price tag, which makes it a target for counterfeiting. With an RFID tag embedded in each container’s packaging, retailers or health-care facilities could verify a product’s authenticity before a patient consumed it. For the Fentora RFID project, the packaging provider embedded a tag in the interior of each product’s carton, and RFID readers and antennas were mounted along the Cephalon assembly conveyor belt, in order to first encode and encrypt the tags as the goods were packaged in the item-level cartons, and to then provide a verification read of the tag before the products were packed into boxes for shipment to customers. In 2007, Cephalon had begun tagging cases and pallets of Fentora at its Salt Lake City manufacturing facility (see Cephalon Moves Ahead with its E-pedigree Plans).
Many pharmaceutical manufacturers are either piloting or installing RFID systems in preparation for the electronic pedigree (e-pedigree) requirements expected to be enacted in the State of California in 2015. An e-pedigree is an electronic record that documents the movement of every pharmaceutical item throughout the supply chain, in order to reduce the incidence of drug theft or counterfeiting. RFID technology offers an automated method for collecting that data.
For Cephalon, with its item-level tracking of Fentora, the problem was that the company was achieving only about an 80 percent read rate as the items were packaged and then passed the two RFID interrogators. Any goods not properly encoded and subsequently read needed to be moved through the conveyor system again, so that they could be encoded and read a second time. These results made the use of RFID inefficient. One challenge that the RFID system faced involved encoding and reading the tags in the presence of the aluminum blister packaging used for this product. This difficulty holds true for many other pharmaceutical products as well
Uysal says his lab and Cephalon’s team began discussing testing the system at the USFP RFID Center for Applied Research in spring 2011. In March of last year, the researchers constructed a rectangular conveyor measuring approximately 8 feet by 10 feet, intended to serve as a model of the Cephalon conveyor, on which item-level products revolved repeatedly in a closed loop, thereby enabling researchers to collect an unlimited number of RFID reads from tags repeatedly passing readers, 24 hours a day, seven days a week.
The researchers first gathered baseline information confirming that they, like Cephalon, were attaining about an 80 percent read rate, using the same tags, readers and reader antennas utilized during Cephalon’s Fentora item-level pilot, and in the same configuration. The team then began making adjustments to the interrogators’ read zones, as well as trying different antennas and tags, and repositioning those tags and antennas to various locations and angles. Turkish RFID company Borda Technology provided RFID software used by each reader to adjust the settings related to the devices’ read zones, such as changing the power output or coding algorithm. The software not only instructed the two readers to adjust their operational parameters at preset intervals, but also collected read data as the parameters changed, thus enabling the researchers to review the results on an Excel spreadsheet.
The research team found that an EPC Gen 2 tag attached to the elongated side of the product carton, facing the reader antenna and parallel to that antenna’s orientation, achieved the highest read rate. By adjusting the location and model of antennas and tags, and by setting the reader software to the optimal parameters, the researchers accomplished a 99.5 percent item-level read rate. They then made the same modifications to the RFID system at the Cephalon manufacturing site, and experienced the same high read rate.
The greatest takeaway from the experience, Uysal says, is that the lab was able to demonstrate that a problematic RFID installation can be resolved via appropriate research and testing. “A lot of people say RFID is cool, but when they have it installed, it may not work the way they need it to,” he states. “What we take away from this is that this kind of study will save a lot of trouble.” Those first installing a system should be prepared to conduct such field trials, he notes, or to visit the type of research institutes that can test the system for them, prior to installation.
Once the Florida researchers reconfigured the Fentora manufacturing plant’s RFID solution in August 2011, Uysal says, Cephalon’s staff were satisfied with the results. “We went in there on maintenance day,” he says, while the conveyor was temporarily deactivated. The team installed new antennas in the same orientation that had been the most effective at the lab, while applying tags at the same location within the pills’ packaging that had been used during testing. “It was impressive to see the same accuracy,” he says, noting that thanks to the high read rate, “they were happy to see the results.”
At the time of this writing, it is unclear whether the drug company will opt to continue with the pilot, or to permanently adopt the use of item-level RFID tagging for Fentora.
Uysal will describe the tests, as well as the takeaways that his research team gained, on Apr. 5, at RFID Journal LIVE! 2012, taking place next week in Orlando, Fla.