After proving the benefits of RFID technology in tracking inventory of training uniforms and related items as they are issued to recruits at the Lackland Air Force Base‘s recruit training center, the Defense Supply Center Philadelphia (DSCP)—a branch of the U.S. Defense Logistics Agency—plans to expand the system to include the vendors that manufacture higher-value personal supplies, such as helmets, and the warehouses at which the products are received and shipped to the recruit center. DSCP’s RFID initiative is intended to increase the visibility of products as they pass through the supply chain and are received by new recruits, thereby reducing errors and increasing inventory accuracy. DSCP supplies food, clothing, and medical items or equipment, as well as construction and equipment supplies, to U.S. military personnel and dependents worldwide.
Each month, DSCP purchases and ships hundreds of thousands of uniforms and related items to armed services members at nine U.S. recruit training areas. The supply chain is complex; as many as 400 vendors and subcontractors in the United States provide the products, which are sent either to commercial third-party-logistics companies or to DLA warehouses, and then on to a recruiting center when they are ordered. The center tries to provide a 45-day advance of inventory to each recruit training center, at which new recruits receive their basic training prior to military service.
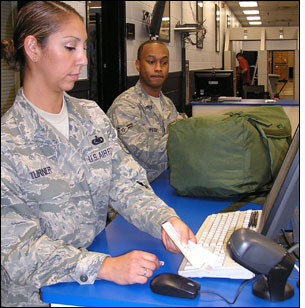
By installing an RFID system, DSCP hoped to determine a specific product’s location in the supply chain, as well as when it was shipped or received. Shipping or warehouse personnel would be more likely to input accurate data into DSCP’s management system—which, in turn, would lessen the need to track missing inventory.
Because DSCP pays a vendor only after it verifies the correct order has been shipped by that vendor and received by a third-party-logistics provider or DLA warehouse, an RFID system could also speed the payment process. In addition, it hoped the technology would eliminate inaccuracies that can lead to double orders or missing items. Finally, DSCP gets reimbursed by the recruiting center for the items it supplies as soon as those items are individually issued to recruits, so if items remain monitored by RFID, it would be paid and the inventory replenished once the transactions are recorded.
Another inefficiency in the system that DSCP intended to address occurs at the point at which equipment is acquired by recruits at the training centers. There, a recruit is assigned a series of clothing and other wearable items, which he or recruit center personnel must pick off the shelf and place in a duffel bag, which is then examined by personnel. Typically, the staff must count the items, look at labels, and ensure no mistakes were made—for example, taking too many pairs of socks, forgetting a piece of clothing, or taking inconsistent sizes (one large and one small pair of pants, for instance). As an individual examines the items, other recruits or orders line up, waiting their turn, resulting in delays of up to three hours per person.
DSCP decided to initially address this last challenge, using RFID, says Angela Richwine, a DSCP business process analyst for the clothing and textiles supply chain. In October 2007, workers at the Lackland recruiting center in San Antonio, Texas, began placing passive ultrahigh-frequency (UHF) EPC Gen 2 RFID tags on garments after they arrived from DSCP. The item-level tags are printed and encoded with a unique ID number, as well as a stock number, nomenclature and size. That information is then stored in DSCP’s RFID-based software, which pushes the item’s identification and location onto the organization’s existing inventory-management system.
The items are stored in an inventory room. As recruits’ personal items are located (either by the recruit, or by Lackland personnel), they are selected from a list, and placed in duffel bags—there can be as many as 60 items for one recruit, including his or her helmet, cap, boots and T-shirts. (The weekly volume at the Air Force’s Lackland recruit training center often exceeds 100,000 items issued.) Once the clothing has been selected, it is taken to an adjacent area and placed on one of the desktop RFID readers installed by AdvanTech, a systems integrator based in Annapolis, Md. The reader captures all of the unique ID numbers on the RFID tags, which link to data regarding the items in the back-end system. A screen attached to the reader displays an alert if any necessary items are missing, or if an incorrect or extra item has been placed in the duffel bag. If all is present and correct, a green light is illuminated, and the recruit can then take the duffel bag. By using RFID, the average time a recruit spends collecting and verifying his or her order was reduced from four hours to 45 minutes.
Based on that success, DSCP is installing a set of RFID portals this month—three altogether—through which each recruit will pass with his or her filled duffel bag. In this case, there is no need for the recruits to stop or place the items on a reader. As they pass through the portal, it captures all ID tags and either displays an alert or approves the purchase of those garments. At that point, Lackland Air Force Base buys the items. If the portals prove to be affective, Richwine says, DSCP will phase out the desktop readers.
With an eye to the supply chain, DSCP has now begun testing RFID to track products from vendors through three third-party-logistics warehouses—Lion Vallen, Travis and Peckham—or one of DSCP’s 22 warehouses, prior to shipping to recruit centers, says Army Col. Kevin Stoddard, the director of plans and integration for DSCP’s Clothing & Textiles Supply Chain division.
In summer 2008, one vendor, Warmkraft, based in Taylorsville, Miss., began tagging uniform items, the cartons in which they are packed, and the pallets on which they are loaded, using UHF EPC Gen 2 passive tags. Once the items are packed and readied for shipping, Warmkraft staff members read the tag, carton and pallet IDs, and then enter data into the DSCP software via an Internet link developed under a DLA research and development initiative by Modulant, of Long Beach, Ca.. The items are then shipped to DSCP and on to the recruitment centers. Five more vendors followed Warmkraft in applying RFID tags directly to their products, and several more are currently in the process.
One of the third-party-logistics providers—Travis—is also reading tagged items as they arrive from RFID-enabled vendors, as well as applying RFID tags to some items that had not previously been tagged, which it then reads and inputs into the DSCP system, and again reads as the goods are shipped out. With this improved data, DSCP now knows when an item has left one of the participating vendors, and when it was received at the warehouse of one its third-party logistics providers.
Eventually, DSCP expects more of its approximately 400 suppliers and subcontractors will be using RFID technology to tag and track the product shipments. “Experience with the technology at recruit training centers has indicated that a hybrid approach, wherein some vendors will apply RFID item-level tags prior to shipment to DSCP, and some tags will be placed on the items at the third-party-logistics providers prior to shipment to the recruit training centers, is more cost-effective,” Stoddard states. For some of the smaller manufacturers, he says, the installation of RFID would be inappropriate. Those that sell individual, relative-high-dollar-value items, such as cold-weather gear, chemical protective suits and ballistics-protective garments, may be required to add item-level RFID tracking in the future. These, Stoddard says, “should utilize RFID technology when we can do so cost-effectively, in order to aid in the tracking of expensive items, improve inventory accuracy and other logistics considerations.”
To date, Stoddard says, DSCP is employing hundreds of thousands of tags per month. The organization is using the data to improve inventory accuracy, knowing when a product was shipped from a vendor, as well as when it was received, and is thereby paying vendors more quickly for shipments as they arrive, and spending less time trying to resolve clerical discrepancies. “We’re getting very good data,” Stoddard says. “Our inventory accuracy is improved. It’s head and shoulders above the manual system.”
Thus far, Stoddard notes, the greatest benefit has been time savings on reconciling physical and computer inventory levels. “We know there is a time savings, but have yet to acquire a good measure,” he states. The agency has reduced the time spent on inventory tracking by about two-thirds, he says.
The passive RFID systems, once installed at all nine recruit training centers across the United States, are expected to save more than $8 million during the 10-year period from the first implementation at Lackland, in 2007.