Commercial laundry and textiles rental company Fishers Services has equipped its latest “super laundry” in Glasgow with RFID readers to interrogate tags attached to the linens it provides to its customers, as well as on all bags and roll cages that it uses to ship those linens, so that the firm can view when goods are received, laundered and shipped to customers. By using the RFID system, provided by UBI Solutions, the laundry company can not only better manage its inventory of linens to prevent losses, but also provide its customers with access to the data.
Since 1900, Fishers has provided workwear and linen laundry services across Scotland, where it is headquartered, and in the North of England. At present, the company leases its own linen products—such as sheets, duvets and towels—to restaurants and hotels that use those linens and then send them back to the nearest Fishers laundry to be washed, dried, folded and returned for reuse.
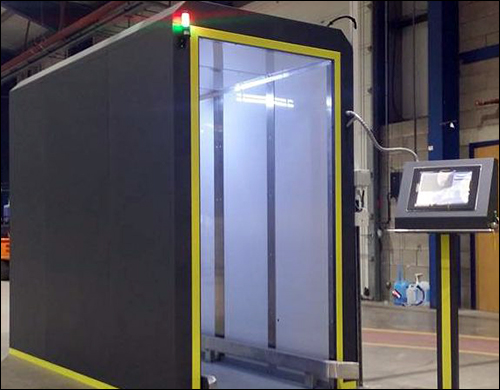
Fishers Services has been growing, the company reports. It now washes, irons and delivers more than two million items every week, and it opened what it calls a “super laundry” near Glasgow in March 2016. The company serves a total of 2,000 hotels, according to Michael Jones, Fishers’ managing director, and the new Glasgow laundry services 300 of those customers, all within a 50-mile radius of its facility. The firm now has twice the capacity as the facility it replaced.
With a large volume of linens moving to and from customers, Fishers experiences a loss of some items that simply cannot be accounted for. The company, which has an annual revenue of approximately £36 million ($52.7 million), loses about £1 million ($1.5 million) worth of product each year across all of its facilities. Fishers sought a solution that would make it easier to track stock moving into and out of its laundry facilities, and to be able to identify when and where any items went missing.
In addition, the company recently released its new ZHEN product. Fishers calls the 200- and 400-thread count range of sheets and towels its “laundry with intelligence,” since it comes with a built-in RFID tag.
In past years, Jones says, the laundry company had been interested in RFID solutions to track inventory, but until recently, RFID tags were not robust enough to survive the rigors of multiple laundering. When sturdy laundry tags became more available during the past few years, the firm tested a software application to manage the RFID data residing on its own server. The software was fraught with difficulties, Jones reports. For one thing, he says, the RFID system had to remain open 24 hours a day so that the read data could be collected and accessed, but that meant the rest of the laundry’s software needed to be running as well. In addition, the company wanted to enable its customers to view data from the system regarding the linens they were using, or were having laundered—but that required Fishers to grant those customers access to its IT system, he says, “and that raised security issues.”
UBI Solutions offered a better alternative, Jones says, since its system came with hardware including touchscreens to access software on a cloud-based server. “It was much simpler for us,” he states.
Fishers operates from a total of seven sites. For the new facility in Glasgow, the company saw the opportunity to launch an automated system to track the new ZHEN products, as well as the bags and metal roll cages it uses to deliver all of its linens—both tagged and untagged. The firm signed a contract with UBI Solutions in mid-December 2015, and the system was taken live in March with the opening of the new laundry, says Renaud Munier, UBI Solutions’ business development director.
Fishers opted to tag the Glasgow laundry’s 4,000 roll cages and approximately 7,000 bags. Nearly 200,000 ZHEN linens have been tagged as well by the linens’ supplier, Pegasus Textiles. The bags and metal cages are fitted with tags supplied by Inotec. (Munier declines to provide the specific make and model of the tags or reader antennas used.)
Fishers installed a portal for receiving soiled linens with an Impinj Speedway Revolution R420 reader and four circular-polarization antennas. Two additional Impinj readers are installed on the two soiled linen conveyors.
After being cleaned and sorted through a manual process, the linens are placed in cages or bags destined for delivery to specific customers. On the way to the delivery dock, employees move the loaded bags and cages through a tunnel reader in the form of a cabin with a built-in Impinj reader and a UBI solutions multiplexer and antennas. Munier declines to reveal how many antennas were installed there. At that location, personnel use a touchscreen to select the customer to whom the items are being delivered, along with details related to what is being sent—for instance, the quantity of towels, sheets or tablecloths. That information is then recorded, along with the unique ID number encoded to the tag of the bag or container in which those items are packed.
In addition, if ZHEN linens are being sent, the unique ID number of each item’s RFID tag is captured and linked with the customer data, so that Fishers knows not only the quantities and types of items shipped, but also the exact identity of each item. UBI Manager middleware captures read data and forwards that information to its software on the hosted server.
When soiled linens are returned from the customer, they are moved to the washing area via conveyor. The Impinj reader installed at that conveyor captures the tag ID numbers of the containers and ZHEN linens, updating the details in the software to indicate what has been returned. Once those items are then received in the washing area, the tags are read one more time for the purpose of redundancy, and to create a record of the actual washing of those linens.
The UBI Solutions software tracks a variety of details regarding the inventory and its movement, Munier says. It monitors the return rates (the number of days it takes for an individual customer to return items), the percentage of items that have been returned (based on the number of bags or roll cages received) and the time required to process every item in the laundry. Because the technology tracks individual ZHEN linens, it can also count how many wash cycles those linens can sustain before they need to be replaced.
The software also provides 30-day stock-level alerts indicating when a customer has kept linens on their own premises for an extended period of time. This enables the company to contact that customer and make sure that those items have not gone missing.
A customer can use a password to log into UBI Solutions’ software and view details about the linens. “Customers, through a standard Web interface, can see, in real time, the flow of linens they receive and then ship back,” Munier states. Customers have full visibility into their level of stock per category as well.
“Our system,” Munier says, “is based on an application engine we have been developing over the last eight years and have been using for over 300 installations—not only in the laundry market, but also in logistics, tool-management and planning applications.”
Jones says his goal was to understand where linens are located. If the technology continues to work well, he expects Fishers to install RFID readers at some of its customers’ hotels, or to provide those customers with handheld readers for even greater visibility. The return on investment, he notes, will be centered around the ability to confirm what has been shipped to a hotel and then returned, thereby preventing the need to ship out additional linens to replace items that might not, in fact, be missing.
In the long run, Jones expects intelligence in the system could help him make decisions about Fishers’ products, such as which items require replacement more frequently. It could also reveal which of Fishers’ customers are experiencing a higher frequency of losses, or damage to their products, enabling the company to then speak with those customers about finding solutions.
Fishers may opt to install the RFID technology in at least four of its laundries during the coming years, Jones says. The company will tag other linens, though it has no plan at present to tag anything for which the tag would represent more than 20 percent of the item’s value.