Turkish Technic, the maintenance, repair and overhaul (MRO) arm of Turkish Airlines, has boosted the efficiency of personnel and tool usage, while reducing unused inventory stock, thanks to a complex network of automatic-identification technologies that includes passive EPC Gen 2 ultrahigh-frequency (UHF) tags. When the company first began seeking a technology-based solution that could improve overall worksite management, it found that its needs for better tracking of tools, inventory, technicians and work-in-progress (WIP) would require a hybrid approach.
The solution that Turkish Technic has developed and implemented, throughout the course of about three years, includes not only EPC Gen 2 RFID tags, but also active sensors based on the ZigBee protocol, along with Aircraft Communications Addressing and Reporting Systems (ACARS) and automatic dependent surveillance-broadcast (ADS-B) wireless technologies, which are used to transmit information regarding an aircraft’s location and its equipment’s status. Data culled from the network of sensors, tags, readers and navigation technology is managed on a single software platform, enabling the company to track individuals, assets and WIP at its MRO facilities. The company reports that the system boosts the level of productive work that employees carry out, as well as the use of resources, and enables just-in-time inventory ordering to reduce the cost of storing inventory onsite. Installation commenced in April 2012.
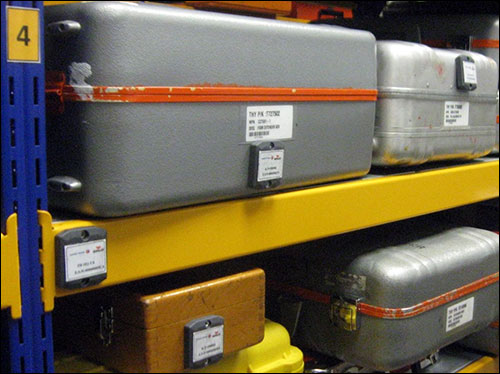
Turkish Technic operates MRO facilities at several locations at Istanbul Ataturk Airport, where its primary purpose is to provide maintenance services to its parent company’s fleet of planes. However, the firm also provides maintenance services to other major airlines and cargo planes operating in Eastern Europe and the Middle East. Services include the maintenance and repair of engines, auxiliary power units (APUs), landing gear and other components. The company employs 2,500 workers and has four hangars (with space for up to 22 aircraft altogether) in which planes are serviced.
The company has been developing the solution—which it calls Networked Maintenance Repair and Overhaul—to better manage its maintenance resources. These consist of technicians, tools, parts and inventory, small vehicles and other ground services equipment, individual hangars and the airplanes themselves. “The overall performance of the MRO operations depends on how efficiently we use the resources that are available to us,” says Orkun Hasekioglu, Turkish Technic’s research and development project manager, who will describe the installation in detail during a presentation at this year’s RFID Journal LIVE! conference and exhibition, being held in San Diego, Calif., on Apr. 15-17. However, he adds, without proper tracking, measurement and control of the resources, and their locations and status, effective resource management is impossible.
Inefficiency is among the main challenges that the system targets. Prior to launching the solution, the company found that a large percentage of a technician’s time was consumed by searching for parts and documents, as well as locating and retrieving ground services equipment. When it came to inventory management, Turkish Technic had an average overstock of parts valued at $2.5 million.
The company learned that there was no single technology it could use for monitoring all assets, inventory and personnel, and thus developed a network of sensors and other technologies to create what it describes as an Internet of Things solution. The firm created its own network to manage the location and status of each tool, part, person, vehicle and aircraft.
From the onset, Turkish Technic compiled a team of software developers, networking engineers, embedded systems developers, business analysts and business-process leads to develop optimal solutions. The team found that low-cost passive UHF RFID tags and handheld readers could track the locations of tools and inventory and flyable components. On the other hand, to manage the locations of moving individuals and vehicles in real time, it required active technology. Therefore, it chose to employ battery-powered sensors using the ZigBee protocol. “However,” Hasekioglu says, “customizations and additions have been made in the routing and network layer protocols and localization algorithms.”
ACARS and ADS-B radios are already built into each aircraft, which could be used to identify the locations and positions of airplanes onsite. This, the company explains, enables it to better manage its space, and to set up a servicing schedule around the planes’ locations.
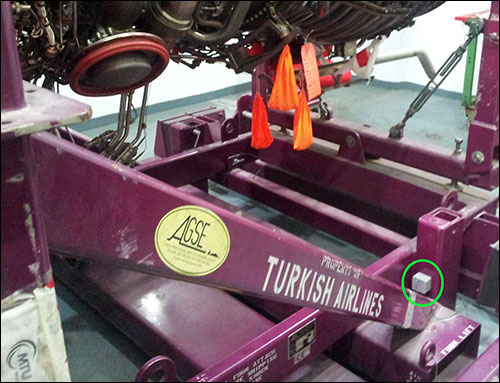
The individuals and assets that needed to be located could be outdoors, on aprons (paved areas, abutting the hangars and buildings, where planes are parked), or indoors, in maintenance hangars and shops.
For tools, the RFID technology needed to provide the company with data about the location and calibration of every item used for repairs. It also needed to know the location and maintenance history of each part it had onsite. To accomplish this goal, Turkish Technic has applied RFID tags from a variety of vendors in two memory levels—8 kilobytes and 64 kilobytes—to tools and emergency assets for use within plane cabins. The tags can store data written to them about servicing and maintenance, and that information is also stored in the back-end software. In addition, the company is using Maintag‘s Flytag to track aircraft components.
Altogether, Hasekioglu reports, approximately 5,000 tools and test equipment items have been fitted with passive UHF tags. Tools are stored in the company’s tool shop when not in use. The shelves on which they are stored also have RFID tags attached to them. When a staff member puts a tool away or provides any servicing, such as calibration, he or she uses an ATID handheld RFID reader to interrogate the tag ID number of the tool, as well as that of the shelf label, thereby linking the tool’s location to its own ID in the software. “The handhelds are used to update the inventory, typically at the end of each shift,” he states. To perform inventory counts, a worker simply carries the handheld past the shelves and thereby updates data regarding each tool’s location.
In a plane’s cabin interior, life vests, oxygen generators and other emergency devices are also tagged with RFID tags. Moreover, technicians can employ the ATID handhelds to view the locations of those tagged items within a plane, for inventory checks and other purposes.
Ground services equipment and staff are being tracked via about 350 active ZigBee sensors, complying with the IEEE 802.15.4 standard. Some sensors are attached to moving equipment, such as small ground vehicles, while others are worn by personnel in the form of badges.
Each sensor transmits its unique ID at set intervals, and receives and forwards the transmitted data via a mesh network formed by all of the ZigBee sensors that the company has deployed. That data is ultimately collected by access points that forward the information to the back-end software, so that management can view the locations of individuals and equipment in real time. Outdoors, location is identified by GPS technology built into each ZigBee sensor. For assets and personnel located indoors, the system employs a combination of received signal strength (RSSI) and signal time of arrival (TOA). Turkish Technic utilizes a network of mobile and fixed sensors for this purpose. About 50 stationary ZigBee sensors have been attached to the hangars’ walls. RSSI and TOA values for the transmissions of each mobile sensor are calculated based on the locations of the fixed sensors.
When it comes to the aircraft, the company needs to know each plane’s location and the health of its various systems, as well as the hangar’s availability. Currently, almost all Turkish Airlines aircraft are equipped with ACARS and ADS-B transponders, and Turkish Technic is thus using those technologies to feed location and system-health data into the system. To determine whether or not a particular hangar is already occupied, the solution uses video cameras.
Plans to further extend the project to various aircraft component maintenance shops within the organization are still underway, Hasekioglu says.
Since the system was installed in several phases throughout the past three years, Hasekioglu reports, the availability of and access to ground services equipment has improved twofold. This, he says, has enabled the company to reduce the amount of extra inventory that it previously kept onsite in case equipment could not be located.
The amount of time that technicians spend carrying out repairs has grown by 20 percent, the company notes, since the system has reduced the time they spend searching for tools or equipment, compared with in the past. What’s more, the firm is better able to provide real-time management, monitoring and scheduling of maintenance resources, including technicians, equipment, aircraft, tools and cabin interior emergency devices.
The project has received financial support from the Turkish Science and Technology Foundation.