Second-hand luxury goods auction company Bang Master Group (BMG) is employing RFID as part of an automated process for collecting information regarding each item’s seller, appraisal and auction sale, as well as unsold inventory. Since the system was introduced in September 2015, the company reports, it has reduced inventory-counting time following auctions, and has ensured that no counterfeits are swapped for authentic goods at any time during the receiving, appraisal or sale process. The system, provided by EPC Solutions Taiwan, consists of passive EPC Gen 2 ultrahigh-frequency (UHF) RFID tags, fixed and handheld readers, and software to manage the collected RFID read data and forward it to BMG’s enterprise resource planning (ERP) system.
Historically, BMG was a traditional pawnshop in the southern Taiwanese city of Tainan. Over time, however, the company has grown to focus on running auctions for luxury and high-value goods, such as handbags, wallets, shoes and watches from Louis Vuitton, Chanel, Rolex and other brands. The company sells approximately 80 to 120 pieces daily at three- to five-day auctions that take place every three to five weeks at hotels throughout Taiwan and China. Higher-volume auctions are held in September and March.
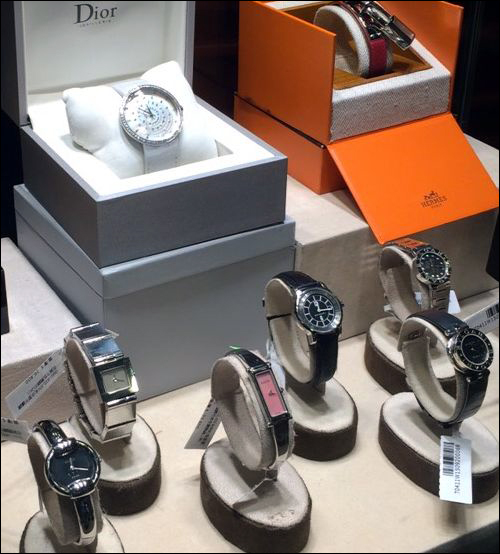
Recently, the company began working with EPC Solutions Taiwan, which developed and provided an RFID system with which it could track the purchasing, appraisal, auction and certification of its goods. The firm initially launched a pilot to test the technology prior to the September auction, and has since used the solution in that auction, as well as at a subsequent, smaller one.
When someone contacts BMG with the goal of selling their luxury goods, the company sends its employees to that individual’s home or office, to collect the items for auction and provide the seller with a receipt indicating those goods have been received. Once the products arrive at Bang Master’s location in the Taiwanese city of Taoyuan, appraisers examine the items and determine their value, and the starting auction prices are set according to that amount.
Following an auction sale, BMG reimburses the seller and provides the buyer with a certificate of authenticity.
The manual method had several shortcomings, Bang Master reports, which became a greater problem as the company expanded and began hosting a greater number of auctions featuring more products for sale. Time spent tracking unsold inventory was a problem for auction personnel, who were already tired from the event, and their labor—as well as the hotel rental during that post-auction—was expensive. In addition, buyers sometimes complained that counterfeit items had made their way into the auction. However, BMG could not determine at what point in its processes those fake goods had been introduced.
BMG wanted a system that would track inventory as soon as it was received from a seller, delivered to the appraiser and then sold at auction, and it sought to ensure that nothing was swapped out before it arrived at the appraiser. “We deployed RFID for inventory and ID authentication,” says Tory Yuan, Bang Master Group’s strategy manager.
With the RFID-based system, each item is assigned an EPC Solutions Taiwan RFID tag made with an Alien Technology Higgs-3 chip. If the seller, for instance, indicates he has four items, four tags are included in the paperwork that the workers take to the individual’s home or business. The company reads the four tags, linking each one to a specific product description already provided by the seller. At that location, a tag is attached to each item via a locking plastic zip-tie, and a worker provides a receipt to the seller indicating that the four items were picked up. Because the zip tie must be cut to remove it from an item, it would be difficult for the tag to be reapplied to another product, though not impossible—it could be done if a staff member were able to acquire the same type of zip tie and reapply it to another item.
The goods are next delivered to the appraiser, at which time the tags are read for the second time. The appraiser enters information about those items, and the seller then uses an Alien ALR-9640 fixed desktop reader to link the tag ID with that information, according to T.H. Liu, EPC Solutions Taiwan’s president. The appraisers then create an appraisal authentication indicating the product’s value, or return that item to the seller if it is deemed not worth selling.
The collected data is stored on software provided by EPC Solutions Taiwan, residing on BMG’s database. The company stores the unique ID number, along with the seller’s information, data about the item itself and the results of the appraisal. This data is then forwarded to BMG’s ERP and point-of-sale software.
Prior to the auction, Bang Master employees, with the help of EPC Solutions Taiwan personnel, temporarily install a moveable Alien ALR-9900+ RFID portal gate, through which every item is carried as it is brought out to the auction floor. At that time, the reader captures each tag’s ID and transmits that information to the software in order to update the item’s status as having been auctioned.
Buyers receive the certification of the goods matched to each tag’s unique ID number. Each tag can then be removed by cutting the zip-tie holding it in place, while buyers can show that document to BMG in the event that a repair is needed. BMG personnel can input the ID number on the certification and automatically access all data related to that product’s appraisal and auctioning.
If the item is not sold, auction workers use Atid 870 handheld readers to interrogate the tags so their ID numbers can be compared against the list of goods purchased. In this way, the company can make sure that every item not sold is still present.
“The process works fine,” Yuan states. “The greatest benefit is to shorten the inventory time after auction.”
While he says it previously took four individuals three hours to conduct the post-auction inventory count of unsold items, that task can now be accomplished in half an hour by two employees armed with the handhelds. The system also prevents errors, he adds. “Staff members are very tired after auction,” Yuan explains, “and that means mistakes happen often.” With the RFID solution, however, the reading of tags has eliminated such errors. In addition, he says, “the rental fee of the hotel is expensive. We hope to shorten the rental time as much as possible,” by reducing the amount of time workers spend counting inventory.
The technology also helps to foster credibility with the company’s buyers and sellers, by ensuring that no items are swapped with counterfeit versions.