AeroScout Industrial, a provider of active radio frequency identification solutions, has installed an “Internet of Everything” system at a power tools plant owned by its parent company, Stanley Black & Decker, located in Reynosa, Mexico. The solution has enabled the firm to improve product throughput and labor efficiency, and to reduce the quantity of inventory stored onsite for assembly-line replenishment.
Thanks to the W-Fi-based active RFID technology, plant floor supervisors and facility managers now know, in real time, the throughput of each of five assembly lines that produce DeWalt power tools. The appropriate personnel or management can also receive alerts via SMS text message or e-mail in the event of any problems on the line, such as a need to replenish materials, a failed inspection of a finished product, or a mechanical error.
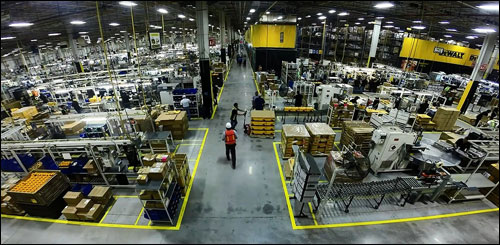
AeroScout Industrial has dubbed the solution—which includes its MobileView software, AeroScout tags and Cisco Wi-Fi nodes—the Connected Factory. According to Janet Chaffin, AeroScout Industrial’s president, the company intends not only to expand the way in which the technology is being used at the Reynosa plant, but also to sell similar solutions to other businesses. This “Internet of Everything” solution is different from AeroScout’s basic real-time location solution (RTLS), Chaffin explains, because it expands on simple location-based data.
Stanley Black & Decker’s Reynosa plant manufactures routers, planers, cordless drills, floodlights, screwdrivers and other power tools under the DeWalt brand, as well as numerous other products and professional tool brands. More than a million of these power tools are manufactured at the 500,000-square-foot facility annually. The site’s management began working with AeroScout Industrial in 2013 to develop a system for inventory control and replenishment. The factory required an automated system to ensure that materials reached the assembly line as needed, and that excess inventory did not need to be stocked, in order to ensure that no out-of-stocks occurred, says Patrick Gilbert, AeroScout Industrial’s director of product marketing.
“In the beginning, we weren’t really sure what this technology could do for us, [but] it was highly recommended by our CIO [of industrial and automotive repair (IAR)], Gary Frederick,” says Nick DeSimone, Stanley Black & Decker’s VP of operations for DeWalt professional power tools (PPT). However, he says, “As we learned about and begun to understand the technology, and the ease of use [and] adaptability to our existing infrastructure, the application became apparent.”
Once onsite, DeSimone says, AeroScout Industrial found that the technology could provide other benefits as well, such as measuring throughput at the end of an assembly line, where quality control was conducted, as well as enabling inspectors at that location to immediately alert management if a flaw was discovered in an assembled tool, via text or e-mail message. Without an automated system in place, Gilbert explains, operators had to record every time that a product error was found (based on its weight), but that data remained unavailable until a line supervisor manually collected it at the end of a shift and entered it into a Microsoft Excel spreadsheet.
Therefore, AeroScout Industrial developed a system using its MobileView software that would enable both replenishment and quality-control reporting, via tags mounted in work areas that employees could press as needed. Tags are not applied to products being assembled, but rather for reporting issues on the assembly line. The company piloted a prototype on a single assembly line before going live with all five lines on which DeWalt tools are made by January 2014.
To transmit and receive data to and from the back-end server, the Reynosa plant had already installed a Cisco Unified Wireless Network before it began working with AeroScout Industrial. Because location data was unnecessary, Frederick says, Stanley did not need to add Wi-Fi nodes to its existing infrastructure. Therefore, he adds, the installation was fairly seamless, and was achieved without any interruption in production.
AeroScout provided its T2 and T3i tags, each of which comes with a button that can be pressed under predetermined circumstances. At each line, five such tags are mounted on a panel along the assembly line for operators to use during assembly. Each time a worker presses a tag’s button, that event is transmitted to the nearest Wi-Fi node, which forwards that data to the MobileView software. MobileView then determines what event has occurred, and where, based on the specific button pressed, and prompts another action based on that event (such as sending a text message to the warehouse if a component requires replenishment).
At the end of each line, a second set of five tags is installed for reporting quality-control data. These tags serve two purposes: to transmit production numbers and to enable inspectors to report a problem. As each boxed product reaches the end of the line, it is moved onto a weight scale. The scale measures the weight, and its built-in programmable logic controller (PLC) identifies if the recorded weight indicates a problem (such as a missing or extra component). The AeroScout tag, wired to that PLC, receives data related to each weight event, and then transmits that information to the back-end server, where the MobileView software collects batch data indicating how productive the line is at any given time. If an operator discovers a problem, he or she can press a tag button, which will cause that information to be forwarded to the appropriate party.
Since the system’s installation, Gilbert reports, product output has increased since any delays and anomalies on the assembly lines can be identified and addressed in real time. Inventory levels are down, he says, because replenishment now takes place in a more measured and consistent manner, while labor efficiency is up, since operators spend less time waiting for another part of the assembly line to catch up with a specific process.
Finally, Gilbert says, the rate of defective parts per million has been reduced by 16 percent, since a defect can now be identified more quickly. As a result, further such flaws can be prevented in real time.
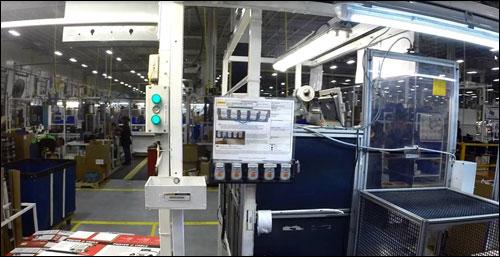
Based on the installation’s success, Frederick says, Stanley Black & Decker’s Reynosa facility intends to expand the system’s use to all of its dozens of assembly lines. Because the system does not require cables for installation, he adds, it can be deployed very quickly, or be moved as assembly lines change for new products. According to Frederick, the technology could then be used at all of Stanley’s plants globally.
Since the system was taken live, DeSimone says, the primary benefit has been instant real-time communication utilizing the site’s existing Cisco wireless network. “We see real-time production as units complete the assembly process,” he states, “which ensures that the lines are on rate.” The AeroScout active RFID tags, he says, “allow assembly line leaders to notify response teams instantly, to minimize any potential downtime. Since the AeroScout Industrial active RFID tags are also location-based, the teams know exactly where to respond within the plant.”
The plant line operators have been instrumental in customizing the system for their specific needs, DeSimone reports. “Once our production line associates observed how the solution worked and tested some of the push-button tags,” he says, they came up with the idea of deploying the Wi-Fi tags on the line to alert the staff regarding the five most frequent issues: safety, quality, materials, maintenance and end-of-line testing. “Our staff really has gotten excited and engaged, as AeroScout Industrial’s solutions fit right into our continuous improvement and lean-manufacturing efforts.”