California technology company Locix is expanding the wireless locating solution that it offers warehouses and logistics providers to factories, office buildings and hospitals, in part to meet demands created by the challenges caused by the COVID-19 pandemic. The post-pandemic supply chain may be more complex than the previous versions, Locix says, in order to bring goods more directly and efficiently to consumers. The company intends its SmartLPS solution to be used in urbanized e-commerce centers to improve direct consumer supply chains.
The LocixLPS solution leverages the 802.11ac based Wi-Fi network using higher RF-bandwidth, up to 80 MHz, to pinpoint the locations of tags or smartphones to within less than 1 meter (3.3 feet) indoors. The company has a deployment at Prologis‘s urban warehouse in Tokyo that illustrates the benefits, says Vik Pavate, Locix’s CEO. Tracking the locations of forklifts and workers enables the company to improve operational visibility for better productivity and utilization of space. Locix also intends the technology to serve hospitals for the purpose of locating patients, healthcare staff or high-value assets, as well as for tracking the movements of individuals to ensure social distancing, while assisting with the use of collaborative service robots (cobots) in warehouses.
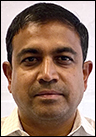
Vik Pavate
The solution consists of the company’s Wi-Fi anchor devices, which use channel state information (CSI) and triangulation, as well as software algorithms, to identify the location of a tag or Wi-Fi device within less than 1 meter. Locix’s cloud-based API then provides data related to the location of that device or tag.
The company was founded in 2014 by Pavate, along with two UC Berkeley professors with backgrounds in electrical engineering and computer science, to provide an affordable, wireless spatial-awareness solution. “While there were a lot of companies in the commercial space,” he explains, “they were using solutions developed for the consumer application, using existing systems that employed cameras, Bluetooth and GPS.” Locix wanted to develop a solution for companies to track their own assets or inventory, whether indoors or outdoors. “We’ve been working on this for a few years,” Pavate states.
The company’s Local Positioning System (LPS) solution leverages Wi-Fi. While Bluetooth Low Energy (BLE) and ultra-wideband (UWB) technologies both offer wireless location data, Pavate says, “BLE didn’t have the performance we needed.” Moreover, the company felt that UWB would be too expensive to deploy if fixed UWB anchors and UWB sensors were utilized. “So we took the approach of using Wi-Fi,” he says. “We started building algorithms and found we were able to get accuracy within less than a meter while maintaining low-cost.”
Last October, the company released its SmartLPS, a full stack that includes cloud-based analytics, anchors (which serve as Wi-Fi access points) designed by Locix, and trackers. In warehouses, the technology is being used to track forklifts and high-value assets. The system is also designed to locate human workers or robots moving through aisles, as long as they carry a tracking device. In addition, the technology can monitor Wi-Fi-enabled devices such as smartphones or tablets.
Mitsui-Soko Supply Chain Solutions completed a three-month pilot in its e-commerce facility, owned by Prologis Japan, before deploying the system throughout its 6,000-square-meter (64,600-square-foot) space. With the SmartLPS solution, Mitsui-Soko can track workers and forklifts as they move through aisles measuring 3 meters (9.8 feet) in width, providing both real-time and analytic-based data.
In real time, the technology provides management with safety-based data by determining where individuals are located and when collisions with forklifts could pose a risk. By knowing how often forklifts are used, for instance, and by then adjusting their movement for efficiency, Pavate explains, companies can reduce the number of forklifts they require to operate. The data also enables businesses to adjust the placement and storage of inventory, thereby improving warehouse space allocation and space efficiency.
“In that way,” Pavate states, “they can increase the utilization of less-occupied spaces,” for instance. Additionally, the technology can track the movements of cobots, making their use, along with the human workers, safer and more efficient. “Warehouse-management systems today are missing the real-world data of worker movement and insights into what is actually happening to further improve placement of inventory,” he says.
The solution serves a similar purpose at factories, Pavate notes, and the company is carrying out proofs-of-concept in the factory environment to improve efficiency. With COVID-19 quarantines, some plants are seeking a technology-based solution to understand where workers go and whether or not they are maintaining the necessary distance from each other, as well to improve efficiency. The company is currently in conversations with several hospitals that need to locate high-value assets and monitor healthcare providers, where traditional Wi-Fi and BLE systems have not been sufficiently accurate to locate assets or individuals.
Locix’s algorithm uses ranging and triangulation algorithms based on a combination of received signal strength indicators (RSSI), channel state information (CSI) and higher-bandwidth Wi-Fi, Pavate explains, as an alternative to traditional systems that depend heavily on RSSI. The system can use either time of arrival (TOA) or time distance of arrival (TDOA) between a tracker and an anchor. The TDOA version is slated to be released later this year.
Typically, a user would install Locix’s anchors (also known as Wi-Fi stations) every 150 to 250 square meters (1,614 to 2,690 square feet). Each device has a Wi-Fi chip set, as well as a microcontroller connected to a power source, and can be mounted on pillars or a ceiling. A 10,000-square-meter (107,600-square-foot) space would require approximately 50 such stations. For a smaller space, there would need to be at least three or four anchors to create the necessary triangulation.
The anchors are priced between $100 and $150 apiece. Most deployments are leveraging Locix’s trackers that could be worn by workers, Pavate reports. The firm designs those trackers, as well as anchors that are manufactured by a third-party provider, and it provides an application programming interface for use with a company’s existing warehouse-management system or other software.
Prologis’s warehouse in Tokyo represents a similar use case to the distribution centers of the future, Pavate says, in which urbanized warehouses will operate closer to customers for faster delivery of goods. That’s because customers are ordering directly from manufacturers and expect to receive goods faster, and to have them delivered directly to their door.
Locix also offers a high-definition (HD) image sensor solution to manage dock-level efficiency at DC by tracking which vehicles come and go to and from a facility, along with worker efficiency. The solution includes cameras that capture images of each truck, along with computer vision in Locix’s cloud-based software to recognize that vehicle’s identity and company owner. In the future, such data could be connected to Wi-Fi-based data regarding the movements of forklifts and workers, enabling a company to understand when a particular vehicle was loaded or unloaded, and thereby improve efficiency. The collected data can then be linked to machine learning and artificial intelligence, Pavate says, to provide real-time actionable data.