Heavy highway contractors worldwide are employing an RFID-based system to automatically track the arrivals and departures of vehicles on a work site, and to link each vehicle to the weight of the dirt or other material it is delivering. The Sonitrax Online solution, provided by DTSystems, was initially developed to bring visibility and automation to deliveries and billing processes, and has since been used to manage traffic at work sites, according to Frank Nicotera, DTSystems’ president and CEO.
The solution saves road-building projects thousands or even millions of dollars by preventing errors or fraud during the delivery process, as well as reducing the amount of labor required for recording the activities of delivery vehicles. Nicotera says he founded DTSystems to solve a common problem in road construction. Having been a project manager himself, he has found that tracking the delivery of materials by third-party companies was a manual process that was time-consuming and labor-intensive, and that introduced the potential for errors and fraud.
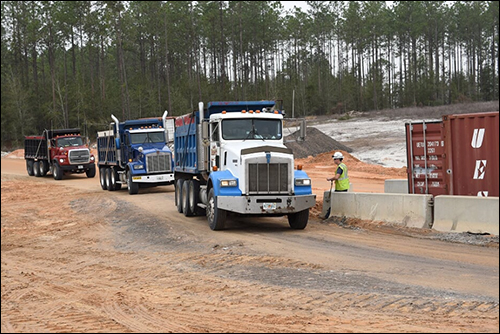
A large portion of road and highway construction requires dirt. Lime and rock are delivered from outside a site, often by third-party providers. Typically, vehicle operators bill for the amount of material they report having delivered, and a contractor employee will gather tickets from the driver at the job site. The general contractor will then quantify tickets to match the invoice received from the trucking vendor for payment.
However, Nicotera found, these third-party companies often tended to bill for more material than they’d actually delivered. Even though businesses use GPS technology to track the locations of their vehicles, and though they use scales to weigh the materials they bring onsite, there was no automated way to link a particular driver, company and vehicle to each delivery. The reality, he says, is that errors were being made.
At one airport where a runway was being built, Nicotera found that about half a million dollars’ worth of dirt had been purchased that was unaccounted for on the job site. There are several reasons this might happen, he explains. A driver could sell part of a load to another party, then still bill the contractor at the airport for that material, or he or she simply might not make a scheduled delivery. With hundreds of trucks entering and leaving a site, tracking every delivery proved nearly impossible.
Seeing no automated solution to capture the ID number of each vehicle arriving onsite, Nicotera decided to build his own. He designed what he called the Data Track System (DTS) system, which employed bar codes. When a driver arrived onsite, the bar-coded ticket and a bar code in the form of an “iButton” on the truck were scanned. If the material was from a quarry with a weigh-scale ticket, the DTS would be able to differentiate between a load ticket and a quarry ticket and thus populate two independent databases for both tickets. “That turned the project around,” he recalls. “We had no theft, no problems.”
Nicotera received a patent for the solution in 2003, then moved toward RFID to further automate the system by capturing each vehicle’s ID during every transaction. “With RFID,” he states, “drivers didn’t have to physically touch a device to a scanner.” The system consists of RFID tags and readers, as well as cloud-based software to manage the collected read data. He created a quarter-sized UHF RFID tag with a special backing for attachment to metal, using peel-off adhesive and a ruggedized casing to protect it from weather conditions. The company also provides its Sonitrax Scanner, made by Videx, with dual RFID and bar-code functionality.
With the RFID system in place, drivers are each assigned an iButton tag upon starting a job. The tag has a unique ID number encoded on it. They can use DTSystems’ cloud-based software to enter four pieces of information: their company name, the bed size, the vehicle’s call letters and the RFID tag number. That data is then stored in the software, and they can attach the tag to their door, mirror or other easily accessible location.
As a vehicle approaches the pit or quarry that serves as the loading site, its tag is read, typically via the Sonitrax Scanner. Although passive UHF RFID can accomplish a long read range, DTSystems opted to dial the range down to about 2 to 3 inches, in order to prevent stray reads of other vehicles that might be in the area or at another spot in the queue.
The encrypted bar-code ticket is scanned first, then the RFID interrogation of the iButton will display the truck’s call letters or ID, so the operator can confirm that the vehicle was loaded and initial the ticket before handing it to the driver. The driver can then continue to the project’s dump site.
At the dump site, the driver will present the ticket received from the pit or quarry to the operator, who then scans the ticket bar code and reads the RFID-enabled iButton to complete the data-collection process. This provides confirmation of the delivery, while also creating cycle times between when the driver left the load site and when he or she arrived at the dump site.
The driver takes the ticket back to his or her employer for proof of delivery. If there is a scale, the weight is captured at the same time, and the operator prints a paper receipt for the driver that can be provided to the employer. In the meantime, the software stores the data related to when each vehicle arrived, along with its net load weight, which is linked to the ID information.
Scan operators at both the load and dump sites can, via cell-based hotspot access, synchronize the Sonitrax Scanner on-demand to forward the collected data to the secure, cloud-based data center for real-time access and reporting on all cross-platform devices. Sonitrax’s Web-based service is a comprehensive PostGreSQL database with extensive reporting and exporting capabilities, Nicotera says. DTSystems has recently become an alliance partner with fleet-management solutions company Zonar.
The technology not only automatically confirms how much material is delivered to each site, thereby preventing errors or fraud, but also speeds the delivery process since data can be collected at the tap of an RFID reader. That, Nicotera says, results in more deliveries at a quicker pace, and thus a faster project completion.
Because the technology is tracking vehicles as they move through gates and choke points to weigh scales, the data accumulated can help project managers better understand the movements of vehicles around a project area. With the software, they can view traffic and bottleneck data so that they can modify delivery schedules and improve efficiency. “The software gives you a broad spectrum of when trucks enter and leave one site,” Nicotera explains, while also enabling historical analytics. Companies are now using thousands of the tags on vehicles that enter project sites.