Delta Air Lines is employing radio frequency identification technology to improve the visibility of oxygen generators installed within its aircraft, and thereby reduce the amount of waste associated with discarding generators, as well as the time required to check the devices’ expiration dates. Each generator has a limited service life—typically, 12 to 15 years—part of which could be lost if products spent excessive time sitting on a shelf waiting to be installed on a plane. Prior to Delta’s adoption of the RFID system, the company estimates that up to 15 percent of its generators’ life span was wasted due to devices sitting in stock.
In addition, when the devices are installed in aircraft, they require regular inspections to ensure that they are not approaching an expiration date. This necessitates a large amount of labor on the part of staff members assigned to this task. Prior to the RFID system’s adoption—when panels above seats had to be opened in order to perform oxygen generator date checks during certain maintenance visits—it made sense to replace every generator that would expire before the next series of inspections. That meant many generators were discarded prior to reaching their full shelf life, thereby creating an unpredictable inventory demand.
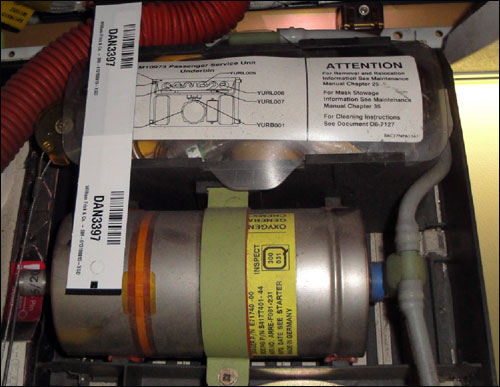
Rick Lewis, one of Delta’s business analysts for aircraft maintenance, spent approximately a year researching solutions, as well as another year in development with the solution providers selected. In carrying out his research, Lewis not only examined the technology used, but also met with maintenance, IT, engineering and other departments within Delta, to determine the type of functionality required. He discussed his experiences during a breakout session at last month’s RFID Journal LIVE! 2013 conference and exhibition, held in Orlando, Fla. (see Delta Air Lines Uses RFID in MRO and Security Operations).
According to Lewis, purchasing these items based on the average monthly stock balance did not reflect the actual demand from scheduled maintenance visits. The company sought to know when generators were close to expiring, so that they would not be removed and discarded prematurely, and also to reduce the incidence of “just-in-case” ordering resulting from not knowing the exact number of generators needed.
In 2011, the company launched a trial using RFID software called RFID AeroCheck, designed by TechnologySolutions and provided by Aerospace Software Developments (ASD) Ltd. Custom-designed EPC Gen 2 ultrahigh-frequency (UHF) passive RFID labels supplied by William Frick and Co. were attached to oxygen generators on 10 Boeing 757 planes. Delta had determined that the process it had been employing to check expiration dates on oxygen generators required about eight man-hours on each plane, to physically read the manufacturing dates printed on the devices and then calculate each item’s expiration date, based on that information. With a Motorola MC9090G handheld reader loaded with the RFID AeroCheck software listing each generator’s tag ID and expiration date, a single worker can accomplish the same task within two minutes, the Lewis told that audience at LIVE! 2013.
To inspect a plane, an employee launches the software on the handheld reader, and begins with a screen displaying a list of all oxygen generators installed in panels above the aircraft’s seats. As the tags are interrogated, the list is depopulated, so that all a user sees are the exceptions (missing or expired generators). The read distance, Lewis noted, is 10 to 20 feet.
Thanks to RFID, Lewis said, for a two-aisle Boeing 777 plane, it now takes personnel 45 seconds to check the expiration dates of all oxygen generators—which is the amount of time required for a worker to walk down one aisle of the aircraft, from cockpit to rear galley. A smaller, single-aisle aircraft can be checked within 30 seconds. William Frick and Co. custom-designed the labels, which are made with Alien Technology Squiggle inlays, says David Trebacz, the company’s marketing director, because they must meet specific environmental tests regarding flammability and tolerance for temperature extremes, humidity and vibration. William Frick & Co. custom-designed the RFID labels, which utilize an Alien Squiggle inlay layered with highly engineered specialized components, notes Jeff Brandt, Frick’s president. In addition to engineering and manufacturing the label, Frick developed a unique process to generate the industry-standard EPC and Spec2000 data pre-encoded onto each label’s RFID chip.
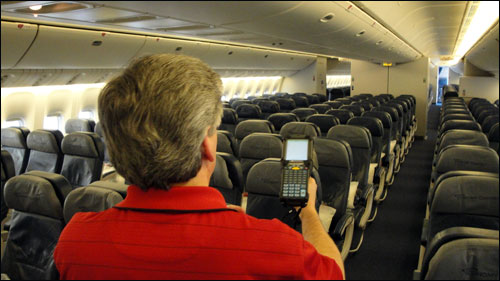
The RFID AeroCheck software interprets read data and links the tag’s ID number with the equipment type and other details, including the expiration date. The software not only resides on the handheld, but also runs on the airline’s back-end server. The software is designed to track up to 32 types of equipment. Each tag is linked not only to the object’s description, but also to its location, such as its seat number.
The RFID system was taken live in 2011, with the tagging of oxygen generators on specific Boeing 757 planes at Delta Air Lines’ TechOps site in Atlanta. Delta is currently developing maintenance procedures for the application of RFID tags on a variety of items other than generators. As the applications for RFID technology in aviation grow, Lewis said, appropriate tags will be developed for a wide variety of assets that the firm is not presently tagging.
Currently, the process of applying RFID tags to parts is being carried out by Delta employees. But as a growing number of suppliers begin tagging parts prior to shipping them to Delta, the airline company could use some of those existing tags rather than applying their own. To date, Lewis says, using RFID to check oxygen generator expiration dates has reduced labor time by 98 percent. Delta has thus far tagged all generators on 87 of its Boeing 757 aircraft (resulting in a deployment total of more than 6,000 tags), as well as on 13 of its Boeing 777 aircraft (for a total of 2,100 tags).
In the future, Delta plans to test tags intended for use on life vests, oxygen masks, aircraft manuals, escape slides and other types of equipment that must be checked for presence and expiration date status.