Aerospace component manufacturer Sekisui Aerospace embarked on a mission several years ago to improve its on-time delivery rate for aircraft components, using a solution centered around radio frequency identification (RFID) technology. The system, deployed at one of the company’s two manufacturing sites and now being launched at the other, has raised the visibility of products throughout the assembly and shipping processes, bringing on-time delivery rates from 30 percent to more than 90 percent. Sekisui’s software partner, Xemelgo, leverages reader hardware selected by Controltek. The technology team described the deployment at RFID Journal LIVE! 2023, recently held in Orlando, Fla.
Sekisui Aerospace operates under the umbrella of Sekisui Chemical, a Japanese plastics manufacturer that makes lightweight composites for multiple industries. Operating out of Renton, Wash., Sekisui Aerospace produces aircraft parts, including environmental ducts in fuselages, for such companies as Boeing, Spirit and Lockheed Martin. Several years ago, the company launched an effort to improve its work-in-progress (WIP) visibility. “We had a big problem around a low on-time delivery rate,” recalls Matea Osojnik, Sekisui’s global senior technology leader.
The company employed an enterprise resource planning system to manage information indicating when components or finished products entered or exited the facility, but it lacked a view into where they were in the interim, including when and why bottlenecks developed at the site. Osojnik had a vision of a technology-based solution by which users could track where each new product was along the assembly or shipping process, and which would allow operators or management to simply pull up a map and answer such questions as “Where are my parts?” or “What are the bottlenecks?” Such a solution, she says, could enable the firm to know when finished products would be delivered.
Automating the Capture of Unique IDs
Osojnik brought in Julie Traweek, the company’s senior product manager, and teamed up with Xemelgo’s engineering director, Renuka Agrawal. The all-female team created an IT innovation lab, then got to work selecting and testing RFID hardware, as well as developing and integrating software. Aerospace manufacturing, by nature, tends to be a more traditional industry that makes changes gradually, though CEO Daniele Cagnatel was committed to innovating a solution.
The team started their efforts with a problem statement, then set a strategy aimed at creating a paperless, data-driven factory. They first targeted the plaster operation. At this site, operators make the tools used to create the composite ducting used for environmental air-control that brings fresh air into each airplane. This section of the company’s operations was experiencing the greatest challenge, for it internally shipped 300 pieces of plaster daily, yet as many as 800 plaster parts in use at any given time could end up missing within that same 24-hour period.
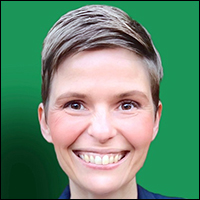
Matea Osojnik
The group tested a solution leveraging barcodes, by which operators scanned the barcode labels on parts as they moved through the production process. With that system, Traweek says, the rate of missing plaster was reduced to zero. However, she adds, workers “hated it” since it demanded an additional manual effort of scanning the barcodes of every item on which they worked. Therefore, the team began investigating the use of passive UHF RFID to automate the capture of each part’s unique identity.
Working with Xemelgo, the team created a prototype solution to test out an RFID reading system that was accurate, seamless and non-disruptive to operators. Once they had tagged plaster pieces and installed readers at key locations, they began testing read rates. The team took the trialing a step further, Traweek reports, by creating challenges: hiding the tagged plaster components to see if those items could be located once they went missing.
Mapping Each Component’s Production
Next, the team began tracking a single work order across the facility to gain visibility into all operations across the production floor. That provided work-in-progress data based on a job-management map, which the cloud-based software could display. To accomplish the map, Agrawal says, the team leveraged existing facility maps to build a visual representation of where orders were located. “We designed a map, broke it into zones, and placed readers and antennas in the appropriate locations to provide visibility into every operation,” she recalls.
The result was a Google Maps-style solution by which a tagged piece of plaster could be tracked in real time as it moved from one station to another. The team input rules related to dwell times and the scheduled movement of each component being assembled, and the map displays each zone in changing colors according to the status of the work underway at that station. For instance, a green zone indicates all work is being accomplished on time, while yellow means there may be a delay and red signifies a problem. The team also installed large screens on the assembly floor to display those statuses for operators.
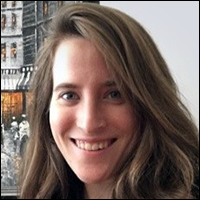
Julie Traweek
At the production site, the team installed 105 fixed RFID readers, which are located at the entrances to new stations, as well as under shelves at some worksites, and in staging areas for shipping. Each new piece of plaster receives a passive UHF RFID tag with a unique ID number encoded on it. The tag is commissioned and stored in the software, where it is associated with its type and descriptive details, as well as the specific customer order it will fulfill. It then begins its journey through the assembly process. At each new zone or station, a reader captures the tag ID as the component comes within range, and that part’s status is updated in the software.
Most stations require just a single reader at the entrance, and the tagged item is recognized as it enters a given zone or workstation. If the same reader at a workstation reads that tag again, the software updates the status as having gone back through the entrance, indicating it may have been sent back to another station. In addition, the system enables users to monitor reader status and identify any failures by recognizing a problem, such as a reader losing power and not operating.
Adjusting the Technology for New Use Cases
Throughout the course of development, a variety of adjustments were made, Traweek says, including tuning issues and the reflection of RF transmissions. Eighty percent of the readers worked exactly as required, she recalls, while the other 20 percent required some reworking or tuning. With the solution now in full operation, operations and management personnel can view where bottlenecks occur, both in real time and historically, as well as the priorities on the assembly floor. Users can also drill into a specific time, operation or product, Osojnik says, and examine trends.
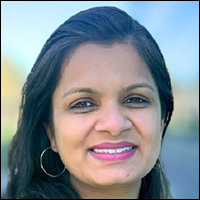
Renuka Agrawal
According to Osojnik, the company can conduct morning strategy sessions around proactive scheduling and thereby better ensure they continue to keep operations on schedule. “In the past,” she says, “we were reacting to data from yesterday. Now, we are seeing the real-time status.” The team has begun deploying a similar RFID solution at the second Sekisui site, with 150 more readers. This second site manufactures interior components for aircraft, as well as engine components. The project’s site survey has been completed, Osojnik reports, and the team intends to leverage the same UHF RFID technology, embedded in plaster parts.
The next challenge, Osojnik says, will be to provide integration of the software data with aircraft manufacturers. That will consist of sharing information about work-in-progress for customers related to their product orders. In this way, the company intends to offer additional value to its customers that will differentiate it from other manufacturers. In the long term, tags embedded in the plaster parts could continue to provide value further along an aircraft’s life cycle, enabling maintenance personnel or airlines to capture and manage data about a part throughout its lifetime. Learn more in this YouTube video.
Key Takeaways:
- The first phase of Sekisui’s RFID deployment brings real-time updates regarding the status of WIP and the shipping of environmental duct work destined for aircraft companies.
- The solution is now being expanded to the second of the company’s two production facilities in Renton, Wash., with customer integration still ahead.