Six retailers worldwide will begin piloting a new feature from Sensormatic Solutions (a Johnson Controls company) early next year, using passive UHF RFID for shrink management. The solution is part of the company’s platform designed to bring intelligence to electronic article surveillance (EAS).
RFID for Loss Prevention is an expanded line of RFID-based shrink-visibility solutions that leverages the company’s TrueVUE software-as-a-service (SaaS) retail analytics solution, using Google Cloud Platform (GCP). Companies can pay a subscription price for multiple solutions, ranging from RFID as EAS to inventory management and smart fitting rooms using RFID or other Internet of Things (IoT) technologies. Pilots are slated to begin during the first quarter of 2020.
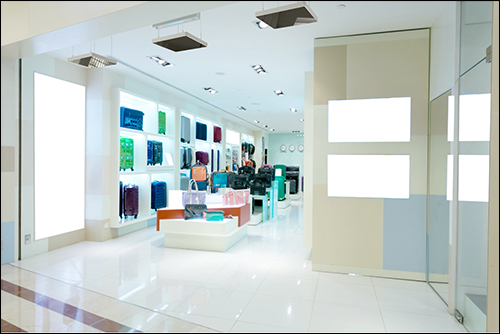
Sensormatic designed TrueVUE to provide an affordable solution for stores to automate the management of merchandise, better enable accurate unified commerce sales and “buy online, pick up in store” (BOPIS) models and improve the customer experience. The company launched the system approximately eight years ago as an on-premises solution to help track inventory, and it provided analytics regarding theft detection using EAS acousto-magnetic or RF technology.
Earlier this year, Sensormatic released a cloud-based version of the solution thay provides the Google-based stack of SaaS features for shrink visibility, as well as other features and functions as customers move toward other capabilities. The SaaS version offers a feature dedicated to capturing RFID tag reads at store exits, whether at the store front (as customers remove goods) or at the back door (where shrinkage can also take place). The feature can be added to an existing TrueVUE deployment, or it can be operated as a new service for which other functionality could be added as needed.
This feature signals the maturity of RFID technology for EAS as UHF tags, says Brent Brown, Sensormatic’s VP of global inventory intelligence and general manager, and readers are achieving greater read accuracy and reliability than in previous years. In parallel, he says, there is a growing presence of RFID tags on garments and other products in stores. Many retailers are finding RFID tags attached to their merchandise by brands and suppliers, Brown reports, and many are applying or using existing RFID tags for their own inventory-management purposes. Using those tags for EAS, however, has posed a challenge. Without the proper software managing such a system, he notes, false or nuisance alarms can be commonplace, and the data coming from the readers is often difficult to manage.
To address these challenges, Brown says, the RFID for Loss Prevention capabilities brings intelligence to the process. The software is designed to identify and capture only relevant tags—those moving through the exit that represent non-purchased items—while filtering out other tag reads. The software then manages the collected data to provide users with information about what has been removed and what needs to be replenished.
The system enables users to link the RFID data with other technologies, such as video cameras. In that way, stores could collect RFID-based data indicating what is being removed, along with a link to video footage showing what is taking place. This kind of feature, Brown explains, serves as a tool to combat organized retail crime (by which shoplifters remove large numbers of goods) or to identify staff members. By using RFID for loss prevention, he adds, retailers can gain greater value from the cost of an RFID deployment that might otherwise be used for inventory management alone. “We’ve moved the solution downstream,” he states, “to help retailers onboard and move into the world of loss prevention.”
Sensormatic developed TruVUE, then redesigned the solution as an SaaS offering. As an alternative to what was once a monolithic piece of software, Brown says, customers can purchase a stack of RFID- or EAS-based features, according to their particular needs. “This new architecture is able to provide core functionality to address basic features a retailer may need,” he states, but users can expand the ways in which they utilize the technology by turning features in the stack on or off.
Many existing TrueVUE users are leveraging RFID only for inventory-management purposes, Brown says. However, each retailer has its own unique requirements and objectives, and as those evolve, the TrueVUE stack can be deployed in varying ways. For instance, some companies like the visual deterrent of a hard EAS tag attached to garments that can be removed at the point of sale. Such a tag could discourage some shoplifting efforts. However, if RFID tags are already applied to products, the two technologies can be used together.
With an RFID reader built into the EAS gate, Brown says, RFID tag-read data can provide greater insight at the exit. Some companies are piloting the use of RFID to capture data about items behind removed, even while hard EAS tags are also attached to products. “There isn’t any single customer that looks like all the others.” he states. The physical layout of stores varies as well. Therefore, he adds, “We have a variety of exit solutions that accommodate different systems,” based on the retail environment. That can include readers that are installed in floors, on doors, overhead or on pedestals—and as store entrances become wider, he notes, the read rate continues to be effective.
Sensormatic can provide RFID-enabled EAS gates, employing the company’s own UHF RFID readers, or retrofit existing EAS systems with an RFID reader. The firm also provides Shrink Management as a Service (SMaaS) to remotely manage the EAS exit gates operations. “We monitor all that infrastructure and can do proactive maintenance,” Brown explains, such as enacting a remote boot before store personnel notices the problem.
With the loss-prevention feature, companies already using the TrueVUE platform could turn on features in their existing stack, such as inventory management. For instance, by retrofitting the gate with an RFID reader, and by subscribing to RFID for Loss Prevention, they could capture data regarding which items leave the store—even if a product is a single tagged item carried between multiple items that have been purchased—and automatically update the inventory-management system, as well as signal an alert. For those not already using TrueVUE, the RFID reader at the gate will still capture data about a product, and the store’s management can view that information to determine which goods have left the premises.
In the meantime, companies can benefit from inventory-management features to gain an accurate view into which products are available onsite. Sensormatic’s surveys of customers have found that inventory distortion starts rapidly after an initial inventory count is conducted without the support of RFID. That becomes a problem for retailers that offer omnichannel sales and BOPIS services. Cancelling a purchase because a product was found to be unavailable at the store nearest the buyer, Brown explains, hurts brand image and disappoints the customer.
For that reason, Brown says, the inclusion of the RFID for Loss Prevention solution helps to bring visibility to what is available at any given store. The system is designed to bring intelligence to determining which tags are read at the exit (thereby preventing stray reads) and what needs to be done with the read data. “Since we have a legacy in loss prevention, we understand the logic that needs to be built in,” Brown states. The company currently has largescale RFID for Loss Prevention pilots under way with customers throughout North America, Asia and Europe.