A team of engineers has been studying how RFID-enabled robots could be employed to automatically measure a soil’s moisture level, as well as monitor the physical health of bridges and other hard-to-access infrastructure. The group developed a prototype system comprising commercially available components, including passive ultrahigh-frequency (UHF) RFID sensor tags, robots and ground control software (GCS) running on a laptop computer to plan the robots’ missions, send them commands, and receive and display the data they collected. Last month, the group published their project findings in a paper titled “A New Vision for Smart Objects and the Internet of Things: Mobile Robots and Long-Range UHF RFID Sensor Tags,” co-authored by Travis Deyle and Jennifer Wang, who work for Google, Erik Schluntz, and Brian Otis, an associate professor at the University of Washington.
The researchers began working on early prototypes in 2012, as they considered ways in which to experiment with Internet of Things (IoT) technologies. “We realized that sensorized RFID tags coupled with robots were a compelling approach to the Internet of Things,” Deyle says. RFID tags work well for a lot of applications, since they are extremely low-cost, can be coupled with almost any sensor and have virtually limitless lifetimes. “But they still have read-range constraints and the reader needs to be in close proximity to read them,” he explains. “This was ideally matched to mobile robots carrying RFID readers; the robot could help deploy and read the sensor tags in remote, hard-to-reach locations.”
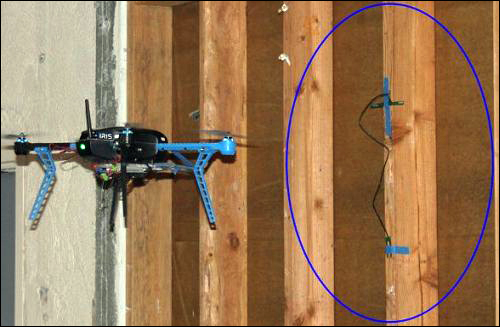
Deyle, Wang, Schluntz, Otis and several others—whom Deyle says are all avid technology hobbyists, especially in robotics, RFID and computer science—spend a lot of their spare time building drones and wireless sensors powered by ambient RF signals.
“We had been tinkering with the idea for several years,” he states. “The project really came together last year, when 3D Robotics released their IRIS+ Drone and Farsens released their sensor tags. With commercial off-the-shelf components readily available, integration was rather straightforward. I think it took us a few weeks’ spare time to get everything up and running.”
Once the plan was in place, Deyle says, it took only a few weeks’ time to construct the robots and set up the tests, which were conducted within just a few days. The test site was an open grassy field, 40 meters by 40 meters (131 feet by 131 feet) in size, and the flying area was free of obstructions taller than 1.5 feet. During the tests, the wind speed was less than 4 miles per hour.
“To make a more academic and peer-reviewed publication, we’d probably need to expand upon the experiments,” Deyle says, “but our goal was just to demonstrate a proof of concept and communicate it more broadly—robots and sensorized RFID tags could be a really good match.”
The researchers purchased a 3D Robotics IRIS personal drone quadcopter to serve as an unmanned aerial vehicle (UAV), as well as a Traxxas Stampede radio-controllable model truck to serve as an unmanned ground vehicle (UGV). To the underside of the UAV and the topside of the UGV, the team affixed a Pixhawk Autopilot module with GPS telemetry as the onboard controller, a ThingMagic M6e UHF RFID reader, a Kent Electronics (WA5VJB) log-periodic printed circuit board antenna and an Arduino Mega microcontroller board.
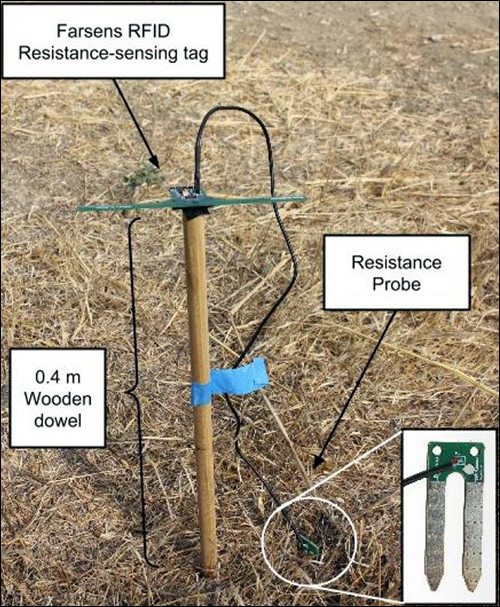
To measure the soil’s moisture level, the group used Hydro sensor tags from Spanish RFID developer Farsens (see Farsens Unveils Battery-Free RFID Moisture-Sensing Tag). The Hydro features a UHF EPC Gen 2 RFID chip and a dipole antenna coupled to a specialized RF integrated circuit (RFIC) that provides electrical power and a serial peripheral interface (SPI) to a companion sensor chip. The tag is wired to a moisture probe that can be embedded in the soil, in order to measure ambient temperature and electrical resistance. The tag communicates the moisture measurements and a 12-byte unique identifier to the robot’s RFID reader. The group mounted Hydro tags to the tops of 0.4-meter-high (1.3-foot-high) wooden stakes planted in the ground, in order to increase their read range. The group also deployed Alien Technology EPC Gen 2 Omni-Squiggle UHF RFID tags—which served as a control to provide identity information—mounted on the ground.
A Lenovo ThinkPad T430 laptop served as the ground control station. The modified Pixhawk firmware was configured to transmit the tag IDs and soil-moisture measurements, along with standard telemetry data, such as GPS locations, to the ground control station via a 433 MHz radio.
The researchers programmed the aircraft’s Pixhawk Autopilot to perform a series of simple robotic behaviors, including an action to navigate to a specific GPS coordinate, circle about a GPS coordinate, change altitude, take off or land. During testing, for example, the drone climbed to an altitude of 3.5 meters (11.5 feet) and then navigated to the first GPS waypoint (which corresponded to a tag location), traveling at 150 centimeters (59 inches) per second. Once at the waypoint, it would begin descending at a rate of 25 centimeters (9.8 inches) per second in an attempt to detect a tag. The drone would hover for 15 seconds, and if no tag were detected, it would begin to circle the waypoint. Once it successfully read a tag, it would leave that waypoint and proceed to the next one (if the drone failed to communicate with a tag after flying a three-quarter circle, it would also leave and continue on). The ground robot was programmed to perform similar tactics.
The engineers report that their tests successfully demonstrated that their prototype RFID robots could be used to automatically measure a soil’s moisture level. They also carried out tests of their robots that demonstrated some compelling future possibilities of sensorized tags, including monitoring water quality and crops, as well as infrastructure that would include measuring stress, strain, corrosion and wear levels for hard-to-reach locations on buildings, bridges, power lines and dams. For instance, the group outfitted their UAV with a boom arm tipped with an adhesive-backed sensor tag. They then used the drone to attach the tag to a hard-to-reach spot on the wall of a brick building, and later returned to take measurements. However, the engineers note, limitations regarding tag read range, battery life and robot control might pose challenges for larger deployments. Current costs are also a concern.
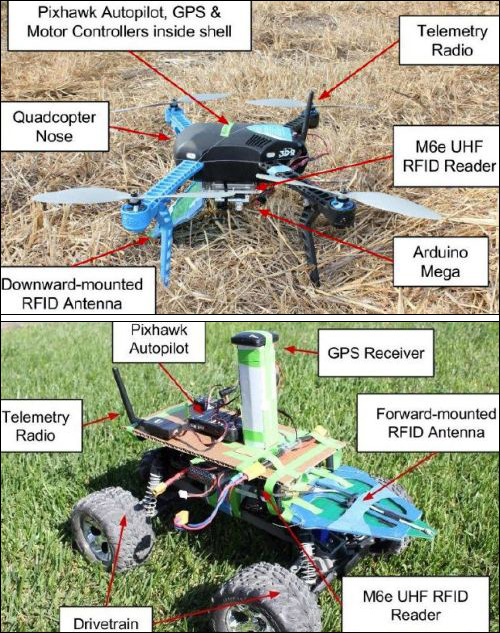
“The cost of UHF RFID readers is certainly an issue,” Deyle notes. “For high-value R&D applications, a $200-$500 reader is a non-issue. But for mass-market consumer applications, and even most hobbyists, current reader costs are a non-starter. You can buy the entire drone for less. If UHF RFID wants to really compete with other IoT technologies, the industry needs to find a way to deliver readers at a fraction of the cost.”
For now, Deyle says, the researchers have no plans to pursue the project further. “Being avid hobbyists, though,” he adds, “I’m sure we’ll find other fun things to play around with.”
This story was originally published on RFID Journal on August 10, 2015