Michigan podiatry clinic Great Lakes Foot and Ankle Specialists has automated the tracking of surgical instruments or tools used on its patients via radio frequency identification, in order to speed up the process of packing the tools onto trays, ensure that no instruments are left inside a patient or misplaced, and track their lifespan. The Surgical Safety Scanner system, provided by startup Surgical Scanner, of Brighton, Mich., consists of passive ultrahigh-frequency (UHF) tags, handheld readers and software to manage the collected read data. The software also links each tag ID number with a particular instrument’s photos, manufacturer, part number and history.
The solution enables the clinic to overcome several challenges, says Jeff Szczepanski, a physician at the facility. Each surgery requires a specific set of tools, but it can be difficult to differentiate between one tool-packed tray and another. Many of the instruments look alike, so the wrong item could end up on a tray unless each tray is double- or triple-checked during the manual packing process. Once a packed tray is wrapped following sterilization, it can also be difficult to determine and confirm which tools are on it. As a result, the wrong tray could be taken to surgery. Additionally, Szczepanski says, the tools are expensive (some priced at $300 to $400) and can end up missing. When this occurs, he adds, tracing back where a particular instrument was lost is often impossible.
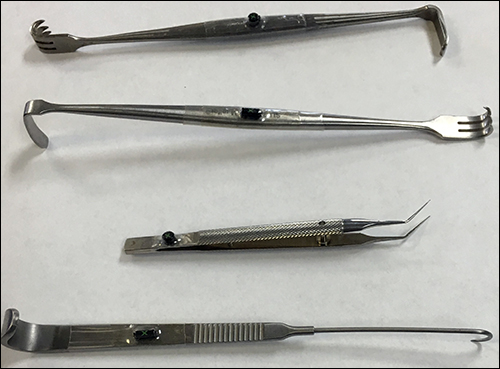
The Surgical Safety Scanner system has been three and a half years in the works, according to Fred Schoville, Surgical Scanner’s president. He developed the technology after speaking with his friend Carol Schmucker, a retired nurse who had identified a problem related to tool tracking. The solution is designed to automate the process of counting and managing surgical instruments and supplies, both before and after surgery and washing cycles.
Initially, the system—which debuted commercially in April 2015—was intended to simply replace a laborious tool-counting process for health-care workers prior to and following surgeries. But the version being employed by Great Lakes Foot and Ankle Specialists, as well as being offered commercially, includes the ability to monitor when tools are used, sterilized and sent for repair, with built-in reminders that are triggered if an instrument is delayed. The system can also determine how often an item has been used.
The manual tracking process is highly time-consuming, however. Surgical Scanner conducted its own testing to find that it usually takes two employees four minutes to count instruments for a typical surgical tray. Once the procedure is finished, the tools must be counted again, which takes longer—usually about 10 minutes, in part because the instruments are dirty and more difficult to identify. On the other hand, the company reports, its own solution requires about 30 seconds for a single worker to accomplish the same task simply by waving a handheld reader over the tray.
To develop the system, the company spent several years testing a variety of passive UHF RFID tags, but determined that most simply did not fit on or adhere well to the small, metal tools that health-care facilities wanted to track. The solution they opted for consists of a Xerafy autoclavable Dot XXS or Dash XXS tag inserted in a secondary heat-shrunk plastic sleeve designed by Surgical Scanner. Surgical Scanner welds or glues a tag to each piece of equipment, and then heat-shrinks a layer of plastic around it. Xerafy has tested the tags through 1,000 washing and sterilization cycles to date. Surgical Scanner, meanwhile, has completed hundreds of its own sterilization cycles, and reports that they are still functioning well.
The company also designed the software to make the process of tracking equipment before and after surgery more reliable and less labor-intensive. That software resides on a user’s own server.
For the Great Lakes Foot and Ankle Specialists deployment, Surgical Scanner attached a Xerafy passive UHF tag to each tool, linking the tag’s unique ID to information regarding that item, such as a description, its manufacturing and expiration dates, and a photo, in Surgical Scanner’s software.
When staff members build a surgical tray for a physician, they follow a list of tools that the doctor has already input into the Surgical Safety Scanner system. That list can either be generic to the type of surgery and patient, or the physician can individually select it for that specific procedure.
After packing a tray, an employee waves a CipherLab 1862 handheld RFID reader over it. The handheld transmits the read data to a PC running Surgical Scanner’s software, enabling the worker to verify that the tray was properly packed. Missing items are highlighted in the software in red, while those whose tags have been interrogated are green.
The tray is then delivered to the surgical room. Health-care workers in that room are also equipped with an RFID reader, and they can scan the entire tray as well, in order to confirm that all items are present before surgery begins. As a tool is used during the procedure, it is removed from the unused tray and placed on a dirty-equipment tray. If an instrument is dropped on the floor and an add-on tool is applied to the tray as a replacement, that event can be input into the software via the handheld reader to detail what occurred.
Before an operation is complete and the surgical cavity is closed, the employee reads the tags of all instruments on the unused tray, as well as those on the used-equipment tray. The software then determines if anything is missing.
The software displays an alert if any item is unaccounted for. In the event that a tool is missing, a picture and description of that instrument are displayed on the screen. The system also enables workers to override it if necessary by inputting information during surgery, such as an RFID tag no longer functioning, thereby ensuring that the non-working tag’s ID does not appear in the system as a missing tool.
Tags are again read prior to the dirty tools being put into a cleaning and sterilization unit, and once more as they come out. By accomplishing these tag reads, a user can create a record of what was sterilized, and when this took occurred.
Great Lakes Foot and Ankle Specialists is using the technology in the manner described above, and has also been conducting three daily inventory checks of the trays within its cupboard: at the beginning, middle and end of each day. The clinic, the system’s first user, instructed Surgical Scanner to apply tags to all of its tools (about 250 to 300, Szczepanski says) two years ago. What began as a trial is now transitioning into a full deployment.
Most of the podiatry clinic’s trays have 10 to 12 instruments packed on them, with 20 to 25 packed trays being tracked throughout the office. Automating the counting processes, Szczepanski explains, makes staff members less likely to lose a tool—and if one does end up missing during surgery, it can be more quickly found via a handheld reader, sparing employees from having to manually search through the surgical room’s trash, for instance.
Because the software displays a picture of each item as it is being read, the system provides a training benefit for new personnel who need to learn what each tool is called, as well as the types of surgeries for which it is used.
While Szczepanski says the system has initially boosted efficiency and reduced the incidence of missing tools, he plans to expand how the technology is used. “In the long term,” he states, “we are looking at tracking the instruments’ lifespan” by identifying how many times each tool has been used. That functionality is already available in the Safety Scanner software, but is not yet in use by Great Lakes. The system could also be utilized in the event of a problem, he says—such as an autoclave unit malfunctioning and not sterilizing at the proper temperature, for example. In such a scenario, the Surgical Safety Scanner software could help to identify what had recently been through that autoclave, so that workers could re-sterilize those items prior to their use on a patient.
The system costs $3,000 to $5,000 for a small clinic, and up to a million dollars for a large institution. It can also be provided on a pay-per-click model so that organizations only pay based on how often the tags are scanned. By the end of the first quarter of this year, Schoville says, Surgical Scanner intends to offer a dental version of the solution as well, for use in tracking dental tools.