Kansas-based petrochemical company Invista aims to boost safety and productivity at two of its facilities with a wireless solution provided by United Rentals. The active 900 MHz radio frequency technology, using Spot-r wearables, receivers and software from Triax Technologies, was deployed in 2019. Triax and United Rentals formalized a partnership to provide such solutions the year prior.
The Spot-r technology has traditionally been used to help optimize the daily operations of a project or worksite. Recently, Triax also developed a solution that serves social-distancing and contact-tracing functions, according to Ian Ouellette, Triax’s product VP. The latest offering is known as Proximity Trace. The technology allows Invista to accomplish contact tracing in the event of positive COVID-19 tests, by enabling it to know who was in the same zone as someone found to have an infection.
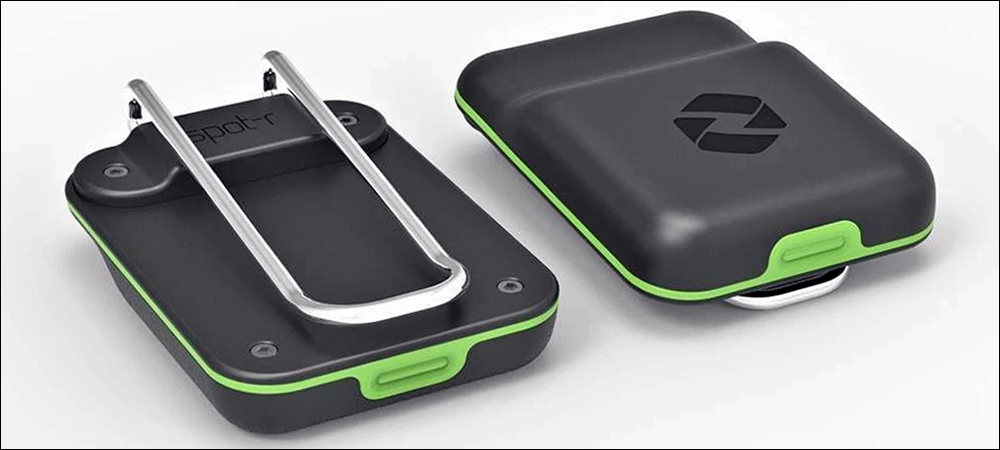
Triax’s Spot-r wearable technology
The petrochemical company’s initial priority was related to fostering safety by detecting and enabling the reporting of worker falls, injuries or other events, and by locating individuals in the event of an emergency. However, the solution also helps to improve productivity, says Kevin Noonan, representing United Rentals’ Advance Solutions Group. It does so by collecting intelligence regarding the locations of workers, which is married to other IoT-based data such as the locations of tools, and by offering analytics so that management can understand how each zone or operation could be better managed.
Invista, headquartered in Wichita, Kans., is a fiber, resin and intermediates company with locations around the world. The company, a division of Koch Industries, has approximately 10,000 employees worldwide. United Rentals, the world’s largest equipment rental company, has provided its services to the petrochemical firm for years to aid with operations and equipment management, among other services. In 2018, the company launched its partnership with Triax to bring the Spot-r worker-safety safety to its customers.
Spot-r provides proximity tracing for the energy and industrial markets. The Internet of Things (IoT) system combines a proprietary reader network, intrinsically safe worker wearable devices and a cloud-based dashboard to provide real-time, data-driven visibility into workers, equipment and specific areas of interest, in order to increase productivity and safety across facilities.
With the Invista deployment at two Texas facilities, located in the cities of Victoria and Orange, workers wear the device while onsite. The 900 MHz active proprietary sensors, known as Spot-r Clips, are about the size of a traditional beeper. Each comes with a rechargeable lithium battery built into it, which can be worn by an employee and has a unique ID number encoded in it that is linked in the software to that individual’s identification. The sensors come with altimeters, an accelerometer and a gyroscope to identify a person’s movement, direction and impact in case of a fall.
Tracking personnel at industrial sites is inherently challenging, Noonan says. The space often covers hundreds of acres and contains large buildings, steels structures, areas for supplies and logistics, a variety of vehicles, and people. A thousand or more workers can be onsite at any given time, some with more experience than others. These might include contractors, as well as full-time employees.
To manage such a challenging environment, Spot-r receivers, known as nodes, are installed around a worksite or at the entrance gate. The devices, which are about half the size of a typical lunchbox, can receive transmissions from sensors at a distance of up to 1,000 feet in an open environment, or 200 feet in a dense indoor environment. The nodes operate in a mesh network, with some using a cellular connection to forward data to Triax’s cloud-based server and dashboard, where software can integrate that information with a company’s project-management software.
If a Spot-r sensor detects that an individual has fallen, it issues an alert, along with its location, to authorized personnel via the receivers. Users can also press a button if they need help. “It’s not only notifying the safety team of an unsafe environment—it knows where they are,” Noonan states. “That level of information adds a tremendous amount of value.” What’s more, the device provides audible evacuation information in the event of an emergency or the need to muster.
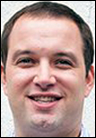
Triax’s Ian Ouellette
During an emergency evacuation, everyone with a Spot-r Clip will receive an alert. They can view or hear this notification and would be prompted to acknowledge it by using the same button they would press to report a problem under other circumstances. They would then move toward their appointed mustering site. Management or appointed evacuation leaders can view who has failed to acknowledge the alert, as well as the locations of those individuals or others wearing the clip. In that way, the company can identify anyone who may not be properly evacuating.
At the mustering site, a point-of-interest sensor captures the transmissions of each clip as individuals arrive, and it can thereby notify the mustering leadership when all are accounted for. The process makes evacuations faster, more efficient and safer, Noonan says, adding, “They’re doing this without pads and pencils or air horns.” The collected data provides visibility into productivity as well, letting facility managers view where there may be bottlenecks or delays, or if materials need to be moved to a specific location. Information can include everything from when a contractor is onsite (so that tools and supplies can be made available at that location) to whether or not there is enough water to keep crews hydrated.
Most recently, the system has helped to protect workers in the event that someone tests positive for COVID-19. “With Spot-r, you can contact-trace by zone,” Noonan says. If an individual has a positive test result, he explains, that person could provide his or her Spot-r Clip to managers, who could then identify other sensors that were within the same zone throughout the previous two weeks.
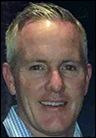
United Rentals’ Kevin Noonan
In the meantime, the Proximity Trace system can be used to ensure social distancing. In such a scenario, real-time alerting can warn workers if they are too close to each other, or if they spend too long in close proximity. The technology alerts workers with an audible and visual alarm, and the device stores a record of each proximity event, for the purpose of more granular contact tracing. Invista is not using the technology in this manner.
The partnership with Triax enables United Rentals to provide greater intelligence to facility and operations managers, Noonan says, which is part of what he calls a journey toward a connected jobsite. “It’s not just where tools or personnel are, but ‘How do you align the information?’,” he explains. “It’s all part of how they can optimize their site. They want to maximize productivity at a site.” For a typical deployment, he notes, United Rentals first meets with a customer to identify its needs, then evaluates the site and designs a network of nodes accordingly.
Invista has not responded to requests for comment, though the company indicated in a press release that the Sport-r technology has helped it to streamline operations, eliminate bottlenecks, measure productivity levels and provide a safety solution. Triax recently released its intrinsically safe (IS) version of Spot-r to provide onsite visibility to improve worker safety and productivity, Oullette says. This version, he says “is intended to meet unique needs in oil and gas chemical processing and other hazardous environments which require stringent controls to keep workers safe.”