Elatec RFID Systems, Polaris Automation and Caron Engineering will describe their smart factory-authentication solutions at RFID Journal LIVE! 2023. The event will feature end-user companies discussing RFID’s use in various industries, as well as exhibitors offering tagging solutions for multiple applications.
Several technology companies have partnered to innovate and deliver a machine operator authentication solution that provides visibility and accountability of workers at manufacturing sites. The solution, which includes software and integration by Caron Engineering and Polaris Automation, leverages wireless, credential-reading access hardware from Elatec RFID Solutions.
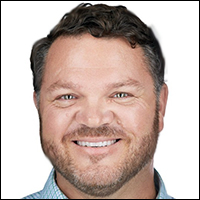
Wolfgang Kratzenberg
Manufacturing companies have begun adopting the system to identify operators not only as they enter a worksite, but as they operate or interact with machinery and tools, or enter secured areas within a facility. The collected data ensures that employees only access or operate authorized equipment, while providing information to management enabling them to improve efficiency and measure the costs and value of production processes for specific products.
The solution can employ Caron Engineering’s RFID-enabled tool-monitoring management, as well as operator identification and equipment access, while Polaris Automation provides software that uses Caron’s operator data to analyze and interpret information regarding operator and equipment activities. The two companies are combining their offerings with the use of Elatec’s access-control hardware that reads more than 60 different credentialling technologies, based on frequencies such as 13.56 MHz (HF RFID), 125 kHz (LF RFID) and Bluetooth Low Energy (BLE).
Traditionally, RFID technology has been used to manage work-in-progress, or to identify supplies, raw materials and finished products at manufacturing sites. However, this solution is aimed at answering the question of who is operating which machinery, as well as where and when, according to Wolfgang Kratzenberg, Elatec’s RFID specialist.
Labor demands have been putting pressure on manufacturers as older workers retire. That means many worksites have a larger percentage of employees with less experience. At the same time, companies must meet customer requirements for just-in-time product delivery and lean manufacturing. Some businesses are turning to technology to help them train and support workers. RFID or other wireless reading technologies can eliminate the signing-in process for workers operating equipment onsite.
How the System Works
Traditionally, machine operators have used physical keys to stop or start a production line, or to enter a username and password. In many case, companies do not always have a complete picture of who is operating specific equipment. On the other hand, every worker tends to have a unique ID number in the form of an employee badge, which the Elatec reader can leverage.
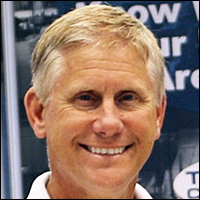
Rob Caron
Companies can either leverage the existing credential used by workers, such as an employee badge, or use their smartphones to be uniquely identified at a workstation or a piece of equipment, Kratzenberg says. Manufacturers using the full solution from Caron and Polaris can deploy the Elatec readers at any key piece of equipment or production line.
When workers arrive at a site, they present their credential to the Elatec reader. It captures the unique ID of their card of phone, then the software from Caron and Polaris confirms their identity. Caron’s software makes the association between the operator’s ID and the computer numerical control machines along the production line. The system then enables the operation of that equipment by allowing the power to be turned on or off, or by releasing a lock enabling maintenance behind a cabinet door.
Polaris’s software receives that data and provides contextual information, such as how long an operator was at a site, as well as what operation they completed, based on their access. The software can provide other features as well, such as reminding workers to follow proper safety procedures, like wearing the proper personal protective equipment or steel-toed shoes. The system can provide instructions or additional information that may help workers in their job, based on their training background. Management can then view the information not only to confirm the equipment is in use and by authorized parties, but also to conduct analytics about the efficiency of the work being done.
All-in-One Reader
By offering an all-in-one reader, Elatec aims to eliminate the need for companies to acquire dedicated credentials. In fact, operators could have a badge with multiple chips in or attached to it, and the reader can be set to interrogate the badge according to the company’s requirements, since Elatec readers work with most RFID transponder technologies, as well as numerous iOS- and Android-based mobile credentials. In that way, Kratzenberg says, the employee badge serves as a ticket to access the machines required to conduct their work.
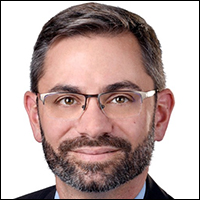
Benjamin Trace
That was a critical requirement for its customers, Elatec reports, because so many companies already used badges for a wide variety of purposes, such as industrial vending machines, printers and front-door access. The ID can prompt the machine to visually display specific content for an operator, and the solution can provide a level of security to ensure that confidential data or drawings are not accessed by the wrong employee. In September 2021, Caron first released its solution to control the operation of equipment. The company also provides solutions for tracking tools via UHF RFID.
The RFID system, which Caron’s customers have used for several decades, includes RFID tags to monitor tools being used in a machine, such as cutting components, according to Rob Caron, Caron Engineering’s president. With a tag on the component’s holder and an RFID reader at the machine, the technology can determine the proper equipment setting for that tool, as well as confirm it is the appropriate tool for a specific job and does not require maintenance or inspection. With the operator-management offering, Caron says, “We’re integrating the whole solution together.”
The operator-identification solution provides a faster and more accurate process for operators on the manufacturing floor, Caron reports. “It eliminates people from having to remember their username and password for specific access to different systems,” the company explains. A site may have a work-area cell consisting of three machines, which could be a robot, a measuring machine and a related component, each of which requires authorization to use or access. Caron provides the Elatec readers, along with the software integration to any machines requiring secure access.
In one example, service or maintenance personnel could be approved to access equipment, but only an operator could operate that same machine. “Someone may be able to open the door to a cell [and] fix something,” Caron says, “yet they can’t actually turn it back on again.” Workers may have access to open a tray in which parts are stored as well. “There can be quite a few levels of access.”
Caron software operates on a local server, while also offering MiConnect, a flexible software that resides locally but communicates to an SQL database or employs an application programming interface to link to existing software. The system can provide an audit log of all individuals who have tried to log in to a specific reader, as well as the access they were given and what happened with that equipment once they received it.
From Pilot to Deployment
Deployments are now beginning with pilots, sometimes with badges from around 10 individuals and a single reader. Following the pilot stage, companies testing the technology may opt to fully deploy the solution with thousands of workers and hundreds of readers and stations or cells.
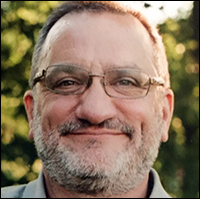
Mark Merino
In addition, Polaris has been providing the technology to manufacturing customers. The company offers its solution through its Digital Factory Solutions (DFS) Group, a division that has been growing exponentially to serve the manufacturing industry, according to Benjamin Trace, Polaris’s senior sales consultant. The DFS Group offers the company’s Manufacturing Execution System software to help businesses gain value from the operator-access data, adds Mark Merino, Polaris’s director of digital factory solutions.
The company has been investigating software solutions to track worker training and skillsets for some time, Merino says. “Some customers have indicated they wanted to get more granularity into how their value streams were working,” he explains, which meant tracking how much time was being spent on various operations within the plant. “So we partnered with Elatec on deploying their solutions,” Trace says, “which do a great job of reading these badges.”
The company then joined forces with Caron to employ its access data. The technology not only enables automated access, but also helps companies achieve a return on investment (ROI) in terms of the efficiencies of their value stream for specific products. For instance, the solution can track operator performance on a particular piece of equipment so that management can better schedule jobs, or identify a particular person who is especially efficient at operating a machine. That worker could then be appointed as a master trainer for others within the organization.
Polaris’s customers have described operator error incidents in which a single mistake by one individual, such as incorrectly configuring a machine, can result in the loss of a half-day’s worth of product. Preventing even a single situation related to such operator error could provide a ROI very quickly, Trace says. The three companies will present their solution at RFID Journal LIVE! 2023, being held on May 9-11 in Orlando, Fla.
Key Takeaways:
- Operator management with RFID and related IoT technologies, provides manufacturers with an automated way to provide and track access to equipment.
- While the system serves an access functionality, it also provides knowledge to businesses looking to better manage their onsite efficiency, training and safety.