Palex Medical, a health-care technology firm based in Barcelona, Spain, is marketing new RFID-enabled solutions to help hospitals manage their inventory of prostheses and other medical assets. The company developed its Dyane smartCabinet and Dyane smartKanban solutions with the assistance of Spanish RFID systems integrator Saident. Hospital Universitari Sant Joan de Reus, located in Spain, is the first hospital to use part of this solution for stock management, to automate the restocking and purchasing of medical supplies. Other medical facilities have been testing the technology as well, and will determine whether to implement the system permanently.
The Dyane smartCabinet is designed to provide access to, and track the usage of, high-value medical items, such as implants, stored behind a locked door. The Dyane smartKanban system is intended for lower-value, frequently restocked supplies, such as gloves or gauze, to help employees ensure that stocks never run low.
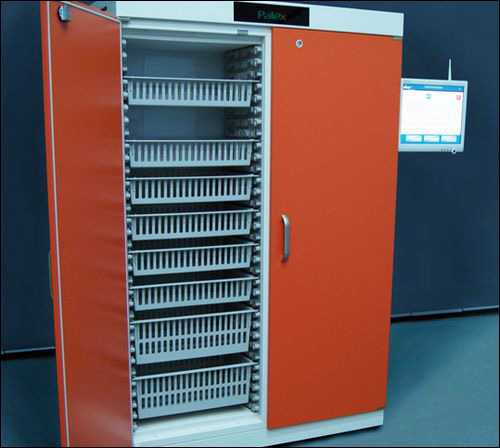
The Dyane smartCabinet acts as an automatic dispensing cabinet, with built-in RFID readers to track tagged inventory stored within, explains Juan Carreño, the head of Palex Medical’s hospital engineering division. A user who needs to access the cabinet’s contents must either provide an RFID card, use biometrics (such as a fingerprint) or log in via a password on a touch screen at the front of the cabinet. That data is received by Dyane logistics-management software, hosted on the hospital’s back-end system, which confirms or denies authorization. If the user is listed as authorized to access the cabinet, the system displays several options to that individual. The worker may indicate that he or she wants to return, search for or retrieve a product, or verify the availability of a full kit loaded with tools specific to a particular surgical procedure. Once a choice is selected, the lock is automatically released and a green light is illuminated on the touch screen.
The user then opens the door, removes the products required for a specific procedure and closes the door once more. The doors relock automatically, and the reader then scans the RFID tags in the cabinet in order to confirm the remaining inventory. Once this occurs, the interrogator can no longer read the unique ID number encoded to the tag attached to each removed item, and that change in read status is received by the software, thereby providing a record of what that individual has taken. The screen on the front of the cabinet displays the items returned or removed, and also notes if there was a discrepancy with the products that the individual initially indicated would be taken or returned. In the event that a door is accidentally left open, a red light flashes on the cabinet and an audible alarm is sounded, warning personnel to the problem.The smartKanban solution focuses on consumable items that do not require a locked cabinet. Kanban is a “just in time” (JIT) method of ensuring an uninterrupted supply of products. Dyane smartKanban consists of plastic RFID cards with embedded RFID tags, as well as readers incorporated into panels or boxes mounted on walls, in which the cards are placed when re-ordering is requested.
With the smartKanban solution, all materials are stored in sets of two compartments: one filled with items that are consumed first, the other serving as the replenishment compartment, containing products more recently removed from the stockroom. Each compartment comes with a plastic card with an integrated passive RFID tag encoded with a unique ID number that links to data regarding the material stored within that compartment. When the initial compartment is empty, a staff member removes the RFID card and places it in a smartKanban reading device mounted on the wall.
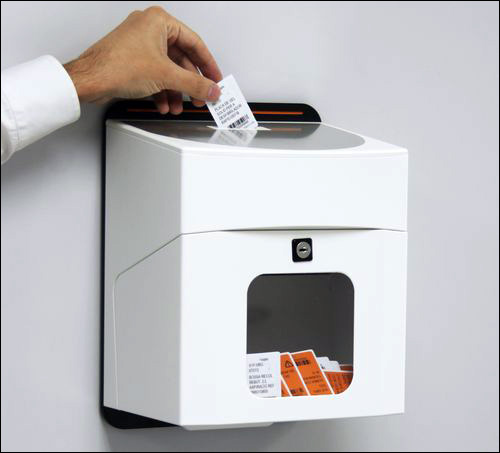
The Dyane smartKanban system is available with a choice of three different reading devices: The PK600 and PK160 are offered in the form of a panel with plastic pockets or slots that accommodate a maximum of 600 or 160 RFID cards, respectively, while the BK200 comes in the form of a box with an opening on top, through which RFID cards are dropped. The PK160 model works with ultrahigh-frequency (UHF) passive RFID tags complying with the EPC Gen 2 UHF RFID standard, while the PK600 and BK200 versions work with 13.56 MHz passive high-frequency (HF) tags complying with the ISO 15693 standard. The reader sends each tag’s ID to the Dyane software, which then determines which materials require replenishment. In the meantime, staff members can continue utilizing the stock stored within the second compartment. If that compartment is running low and the material has yet to be replenished, a worker takes the RFID card from that compartment and places it in the reading device, linking the ID number with data indicating an urgent need for replenishment of that specific item.
Upon refilling the compartments, the stockroom staff takes the RFID cards out of the panel reader and places them back into the appropriate compartment.According to the company, this system ensures that products do not run out, and also helps the staff track the consumption of those goods, thereby preventing an item from being missed and expiring prior to use.
Hospital Universitari Sant Joan de Reus’ staff are using the Dyane smartKanban solution, with 57 of the PK600 panels mounted on walls to read the IDs of tags removed from empty compartments allocated for holding supplies used within the hospital’s surgical area. The collected data is forwarded to the Dyane software, residing on the hospital’s own back-end system, which then sends a message to the stockroom staff that specific products need to be replenished.
Although the hospital has declined requests for comment, Carreño says it has found that the technology allows it greater control over its inventory. What’s more, he adds, the technology also reduces the number of labor hours that employees spend tracking stock levels, thereby enabling workers to devote the bulk of their time to patient care.
The Dyane smartCabinet system works with EPC Gen 2 UHF RFID tags. To date, Palex has provided Smartrac DogBone and Web tags to its customers, for attachment to products stored within its cabinets.