Ortrander Eisenhütte, an iron foundry located near Dresden, Germany, is rolling out an RFID-based system to track forklifts and containers at its facilities. The system, when fully implemented, will employ ultra-wideband (UWB) active RFID tags for tracking 20 to 30 forklifts, as well as passive ultrahigh-frequency (UHF) EPC Gen 2 RFID tags for tracking 10,000 metal containers and their contents.
Ortrander—which reported sales of €23 million ($30 million) in 2008, for its fiscal year ending June 30—casts iron parts for the automotive and domestic appliance industries. In 2001 and 2002, the firm invested heavily to expand its production, and by 2008 it had doubled product turnover. In 2007, the company’s management launched an enterprise initiative to update its material flow, storage and information processes so they’d be more transparent and efficient, and better equipped to handle its higher-production volumes.
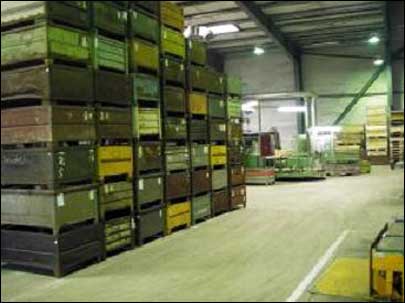
Part of that initiative included a plan to employ radio frequency identification to track forklifts and containers. Ortrander contracted the Fraunhofer Applications Center for Logistics Systems Planning and Information Systems (Fraunhofer ALI), to help it research the market for RFID-based information management systems that would be well-suited for production processes in industrial environments. Specifically, the company sought RFID systems that would work despite the foundry’s harsh industrial conditions and a metallic environment that might interfere with an RFID system’s radio waves.
The research led Ortrander to Ubisense, a supplier of real-time location systems (RTLS) that leverage UWB technology. Ubisense’s UWB tags emit a series of short signals (billionths of a second or shorter); the extremely short nature of the pulses makes the tags less vulnerable to RF noise and interference from metal and other nearby objects. The company’s RTLS includes interrogators (which Ubisense calls sensors) that receive tag signals by means of phased-array antennas. The interrogators calculate tag location by employing two complementary techniques: time difference of arrival (TDOA) and angle of arrival (AOA). By using both techniques simultaneously, Ubisense reports, the RTLS requires fewer readers to cover an area, compared with systems that just use TDOA.
Ortrander is still in the process of selecting a vendor to supply the passive UHF RFID system. Details regarding the exact technology to be used are still undecided. Fraunhofer ALI has developed software to connect the Ubisense RTLS to Ortrander’s ERP system, and will do the same for the UHF RFID system.
In early 2008, Ortrander tested Ubisense’s active tags and interrogators, as well as passive EPC Gen 2 tags from Euro I.D. and other components, for one month. It then began a phased implementation to install the solution throughout its facilities, first focusing on the project’s active RFID element.
The solution currently in operation features a forklift outfitted with two Ubisense tags on its roof, on the outside of the driver cabin, as well as two more on the forks themselves. The tags generate signals between 6 and 8.5 GHz up to 20 times per second. Thanks to its large 1.2 GHz bandwidth, the signal is less affected by interference, enabling the forklift to be located with an error range of +/-15 centimeters (+/-6 inches), according to Holger Hartweg, a sales manager at Ubisense in Dortmund.
Eleven interrogators are affixed to the ceiling of a 2,500-square-meter (27,000-square-foot) production facility used to clean iron parts after they are poured. The facility is one of three that will be outfitted with the forklift-tracking system. The RTLS captures the signals and unique ID numbers sent out by the forklift tags, then analyzes the forklift’s location within the warehouse. Since the tags are affixed at different points on the forklift, the system can also determine in which direction the vehicle is moving.
Ortrander is now implementing the passive UHF RFID application to track containers, with work expected to be finished on the solution by mid-year. The containers are drop-side mesh containers on pallets, which Ortrander uses to move around the parts it casts. A passive RFID tag will be affixed to the long side of each container’s base. After being filled with cast parts, the containers will be transported to the warehouse and stored temporarily in unmarked stacks on the floor, or in storage racks. They will then be moved to different stations, such as the cleaning station, and stored temporarily.
The forklifts carrying active RFID tags will also have UHF RFID readers and antennas to identify the UHF RFID tags on the mesh cages. Ortrander and Fraunhofer ALI are still working out which types of tags and tag casings they will employ. When a driver picks up a container, the forklift’s interrogator will identify that container’s UHF RFID tag, and the system will note which container was moved, and at what time. This information will then be combined with location information from the forklift to let managers know the location to which the container was moved.
At present, Ubisense is integrating scales on the forklifts to weigh containers. The system will calculate a load’s weight by subtracting the weight of the empty container (such information is stored in the database) from that of the loaded container. This data will then be used to help determine the container’s contents, since batches can comprise a variety of different castings.
Bernd Williams-Boock, Ortrander’s CEO, says his company will benefit by being able to locate particular items more quickly, and by having a better overview of production. “We will be able to calculate what can be delivered to the customer, and control the sets of castings,” he says. “We will know if we have the right 30 parts for a particular set [of castings].”
According to Hartweg, the RFID project was originally slated to be finished in early 2009, but other production-related projects at the iron foundry took priority. He now expects the system to be fully implemented by summer 2009.