Atlas RFID Solutions, an automatic-identification materials control company, is selling a new ruggedized tag for the construction industry. The tag, called the Power 1, was developed by RFID hardware provider Omni-ID, and contains both a long-read-range active tag operating at 433 MHz, complying with the 18000-7 (Dash 7) standard, and a passive EPC Gen 2 RFID tag operating at 860 to 930 MHz, thereby enabling the battery life for operating as an active tag to be spared in situations for which a passive tag would suffice. The active tag can transmit a signal to an Omni-ID reader at a range of typically 100 meters (328 feet) in any direction.
Since developing the Power 1 tag specifically for Atlas RFID Solutions, Omni-ID has also released the Power 400, a tag with the same attributes, but marketed by Omni-ID for applications outside of construction. Both tags are commercially available as of this month.
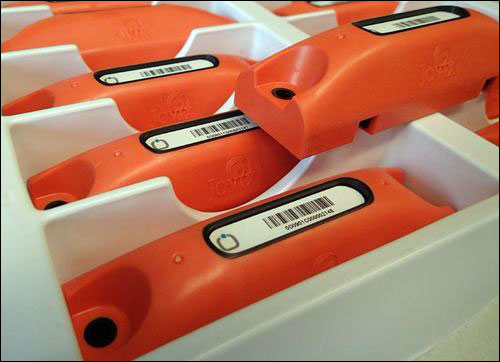
The Power 1 tag results from issues that Atlas RFID Solutions observed as being faced by its customers—companies that construct large industrial facilities for power and energy firms, such as oil-sands or deep-sea drilling operators. Many of these businesses prefer to use active RFID tags that can be located from a great distance and be read through sand, snow or ice. Passive tags do not offer such performance, says Josh Girvin, Atlas RFID Solutions’ product management VP, and most active tags simply do not last long in the types of environments in which they were employed. The tags are often attached to such items as piping, sections of steel or other construction parts and tools, and frequently end up being knocked loose or rendered inoperable in the harsh construction environment. The tags are usually placed by suppliers, who may not have sufficient knowledge of the environment in which the product will be located to be able to determine optimal tag placement. As a result, the tags may be dropped, crushed, stepped on or driven over. In addition, they are often exposed to temperatures that drop below -40 degrees Celsius (-40 degrees Fahrenheit) and then rapidly rise within a short span of time. These conditions, as well as the presence of water, snow and ice (which can freeze, melt and refreeze), can create fissures in a tag’s casing, crush it entirely and affect its battery life.
Atlas RFID put together a list of features that it sought in an active tag, as well as testing procedures, and shared that information with Omni-ID, which then began developing the Power 1 tag. Atlas RFID wanted a tag that could withstand 2,000 pounds of weight, be read from any direction at a distance of 100 meters and have a battery life of five years, operating within a temperature range of -40 degrees to +60 degrees Celsius (-40 degrees to +140 degrees Fahrenheit). It also wanted the tag to be affordable.
To meet these criteria, says Ed Nabrotzky, Omni-ID’s EVP of sales (Americas) and product development, the company designed a tag that operates with both ultrahigh-frequency (UHF) passive RFID interrogation, as well as active 433 MHz RFID. The use of the 433 MHz frequency, he explains—which has a longer wavelength than that employed by EPC Gen 2 passive tags (860 to 960 MHz)—ensures a read reliability in difficult reading conditions, such as ice, snow, rain and fog, or interference-causing materials, such as body tissue, mud and packaging. “Long wavelengths (low frequencies) are much more immune to the effects of reflections,” he explains, “thus penetrating liquids and other common interference materials with more clarity. The 433 MHz tags also achieve longer distance with less power required (less propagation loss) than their higher-frequency cousins.”
The tag, which measures 4.72 inches by 1.42 inches by 1.18 inches in size, can be read consistently from any angle, due to a helical coil antenna designed by Omni-ID (as an alternative to flat planar structures), which curves and is, therefore, easier to read from any position around the tag. To provide the ruggedization, Omni-ID created a bonded dual-layer structure with an ultraviolet (UV)-resistant shell, as well as a second bonded layer underneath for extra strength, thus earning the tag its IP69 rating (signifying it as being impervious to dust and high-pressure, high-temperature jets of water, including full immersion).
By including UHF passive RFID tag functionality, the Power 1 tag can be commissioned without awakening the active RFID tag’s microprocessor. The UHF tag is manufactured with an Impinj Monza X-2K chip, and is wired to the Texas Instruments CC430 microprocessor that serves as a system on a chip, with a processor and a radio module. Upon receiving a box of new Power 1 tags, a customer can read them and store the collected data in the user’s software, by simply interrogating the UHF inlays through the box, and allowing the active tags to remain dormant. The tag comes with a temperature sensor so that it can automatically reduce its beacon rate or decrease the power-draw settings, based on that temperature, thereby extending battery life.
Atlas RFID is selling the tag at the same price as its other active tags, Girvin says, noting that the firm does not disclose specific pricing. About one month ago, he says, a company building a facility for oil bed processing began using the Power 1 tag. He expects customers to save costs in their operations by utilizing the Power 1 tag, he adds, since fewer tags will be destroyed or require replacement due to battery failure. It may also attract customers that, until now, have not considered active RFID tags to be rugged enough for their environments. “Our customers work in some of the harshest environments in the world,” Girvin reports, and without assurance that the tag could survive such conditions, they have been reluctant to invest in the technology.
The Power 400 tag has the same attributes as the Power 1, Girvin says, but is being marketed directly by Omni-ID for different applications, such as tracking trailers or unit loading devices (ULDs) at airports. “For us, this is a step in our continuous evolution,” he states. The company is moving more into the active RFID tag market, Nabrotzky says, adding that the Power 400 is being sought by businesses for small niche applications. Omni-ID’s manufacturing facility is also utilizing the Power 400 to monitor work-in-progress (WIP) at its manufacturing facility.
Although the current technology is compliant with the ISO 18000-7 standard, that could change, pending the ISO 18000-7 standard under revision for 2014, as well as the proposed revised version of the IEEE 802.15.4f standard currently being tested by the IEEE.
“While we will maintain the current tag and protocol for the foreseeable future, to service existing customers and markets,” Nabrotzky says, “we are committed to open standards and will be releasing another version, built on either ISO 18000-7:2014 or IEEE 802.15.4f, in the future.”
Omni-ID’s readers that operate with the Power 1 and Power 400 tags consist of the newly released Link Adapter, a 433 MHz RFID reader that plugs into a computer, and the Link Gateway, a standalone 433 MHz reader that can communicate with a central server via an Ethernet connection. The company offers a variety of reader antennas that work with both models. The Link Adapter and Link Gateway can also be used to read Omni-ID’s View 433 MHz active tags, which have built-in bistable LCD screens controlled via RFID (see RFID Issues Instructions On the Fly).