When the molds used to manufacture aluminum engine blocks are built, visibility into the entire assembly process can help ensure that any defects are caught before the finished block is shipped to a customer. With that in mind, automotive components manufacturer Nemak has automated its work-in-process (WIP) tracking, with a radio frequency identification system supplied by Balluff Inc. that writes sensor data from automation equipment to ensure that any defects in the mold are caught before molten aluminum is poured into it.
Nemak makes aluminum power-train components, including cylinder heads, engine blocks and transmission parts. Traceability involves tracking every step of a mold-making process, using automated identification, at its plant in Windsor, Ontario.
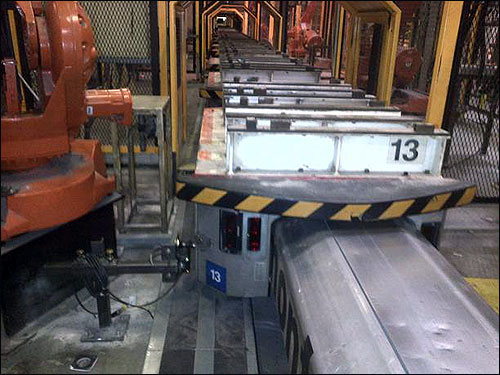
The company required a complex network of sensors, as well as RFID readers, for an assembly line on which it manufactures the molds that it needs to create aluminum engine blocks. Assembling the mold, which is composed of a mixture of sand and resin, is a highly precise process, the company reports. If anything goes wrong at any of the workstations along the 300-meter-long (984-foot-long) loop assembly line, it could affect the aluminum engine block’s integrity. However, because the work is automated, a defective mold might not be caught, resulting in a flawed engine block that could then continue on to be installed within a vehicle.
The Balluff system, deployed in late November 2012, consists of what is called a BIS V processor, which comes with an RFID reader, as well as four ports to read and write RFID data and provide I/O link functionality, explains Mark Sippel, Balluff’s industrial identification marketing manager. The BIS V processor can also be linked to a piece of equipment’s programmable logic controller (PLC), which stores sensor data as well.
Visual sensors detect the presence of each hole or other structure, and ensure that those features are in the correct position or orientation. The sensors also detect or measure the presence of those features, such as verifying that a hole on the engine block is present and in the proper position. Vision systems can then measure that hole’s diameter, and ensure that it meets the tolerance set by its customer.
When a new mold is created, a serial number is assigned to it, which is then stored in Nemak’s software system. The mold is placed on one of the 52 self-powered steel carriers that travel down the assembly line on a monorail. Installed along the assembly line, says Adam Fortier, an electrical engineer at Nemak, are a variety of sensors—in most cases, a vision or laser system—that detect the carrier’s presence and determine its location, as well as whether it is properly aligned, thereby indicating that each process is proceeding as expected. That sensor data, he says, is then evaluated by the PLC.
Attached to each carrier is a Balluff 13.56 MHz high-frequency (HF) RFID tag, compliant with the ISO 15693 standard, with 2 kilobits of memory. The tag’s ID number is interrogated by the first of 18 Balluff BIS V readers along the assembly line, thus creating a record that will then be linked to the mold being created.
At each station, the carrier’s RFID tag is read. The system then proceeds with the next step of the manufacturing process, and additional sensor data is written to the tag. Once the mold reaches the end of the assembly line, the carrier’s tag is read a final time, at which point the system determines whether there are any error reports written to the tag. If any are, the assembly line shuts down and an alert is issued to the staff, indicating that a problem has occurred, along with the specific station at which this took place. Employees can then either discard the mold or send it back through processing, after resolving the error. In addition, personnel can check the machinery at the station at which the error took place, in order to ensure that the problem does not recur.
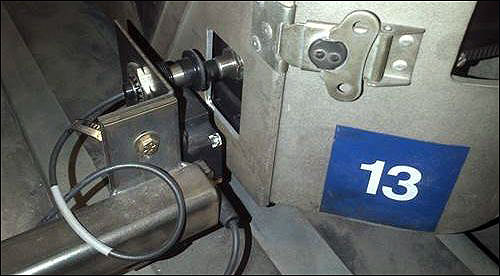
At this final station, the RFID data recorded on the carrier’s tag is stored in Nemak’s back-end system, and is linked to the individual mold’s serial number. The tag is then erased, and the carrier is reused to manufacture another engine-block mold.
“We know we aren’t sending a bad product to the customer,” Fortier states, adding that the system provides an automated record regarding the assembly of each block’s mold, so that in the event of a recall, the company could ascertain what occurred during assembly, as well as which other items were assembled simultaneously. Later this year, Nemak intends to open a new assembly line, at which it will include the same technology.
The next step for Nemak, Fortier says, is to find a way in which to track the mold beyond the assembly line. Once the mold leaves the line, it is filled with molten aluminum to create the engine block. Once the aluminum hardens, the sand and resin mix is baked off in an oven, and the remaining block is cleaned and shot-blasted. However, he notes, Nemak has not yet been able to identify an RFID tag that can survive the oven’s temperatures, which range from 400 degrees to 500 degrees Celsius (752 degrees to 932 degrees Fahrenheit).