Milwaukee Cylinder, a manufacturer of hydraulic and pneumatic tie rod cylinders, has begun selling a radio frequency identification function for its products to help users manage each cylinder’s maintenance schedule. With an RFID tag attached to each cylinder, a user can track inspections and maintenance, write data about those processes on the tag, and view not only a particular cylinder’s maintenance and inspection history, but also which part numbers would be needed if the seal or another part needed to be replaced.
Milwaukee Cylinder’s products are used in a variety of industrial industries, the company reports, including oil and gas, aerospace, automotive and foundries. They are installed in machinery used to run those companies’ operations, and periodically require inspection and maintenance.

In most cases, however, shutting down equipment for maintenance is a major operation that must be carefully timed so that nothing remains offline longer than necessary. Douglas Lacina, Milwaukee Cylinder’s global marketing and engineering leader, says he conceived of the RFID solution based on his own experience as a submarine officer in the U.S. Navy’s nuclear power program, in which maintenance activities had to be run like clockwork in order to prevent unnecessary downtime. If, during that maintenance, parts were unavailable when needed, or if the required replacements had not been anticipated, the shutdown period could be extended, thereby creating a major problem for operations.
Traditionally, equipment such as a cylinder comes with a tag printed with details that include the item’s serial number, bore size, pressure rating and date of manufacture, but reading that information can be nearly impossible if the printed data is oriented such that it faces into the machine, or if it is obscured by equipment, or is dirty or painted over. A cylinder’s identification information is absolutely essential when parts or repair kits are ordered, Lacina says. “If you can’t read the serial number,” he explains, “you can’t order parts.”
This year, Milwaukee Cylinder began working with Balluff on a solution. “Our role [at Milwaukee Cylinder] is to look at problems in the market and try to think through solutions,” Lacina says. The two companies determined that a high-frequency (HF) 13.56 MHz passive RFID tag, compliant with the ISO 15693 standard, would be the best solution, since the tag would not require a battery (meaning no battery replacements would be necessary). What’s more, an HF tag would have a relatively short read range, ensuring that a reader would capture data only from the specific RFID tag that a user wanted to access.
Balluff makes an industrial IP 67-rated HF RFID tag, known as the BIS M-150-02/A, that Milwaukee Cylinder opted to use. The cylinder company developed its own patented mounting bracket to attach the tag to the tie rod or to the cylinder’s side.
The tag contains 2,000 bytes of read and write memory, and can be interrogated from a distance of up to 75 millimeters (3 inches). The memory, Lacina notes, is sufficient to enable the writing of seven sets of comments for as many inspections or maintenance events. After that, a user would need to rewrite one section of data.
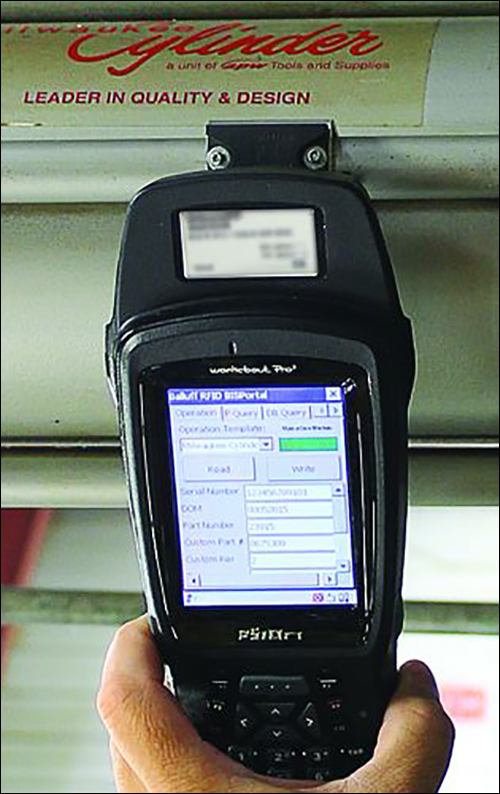
When a customer orders a new cylinder, that order can include the option of an RFID tag, for an additional cost of $99. Milwaukee Cylinder encodes the tag’s memory with such details as the serial number, the date of manufacture and replacement part numbers.
Milwaukee Cylinder ships the cylinder with the RFID tag attached to one of its tie rods, but expects customers to move the tag to the proper orientation and location once the cylinder is installed, so that the tag can most easily be accessed via a reader in the future. Companies can use their existing RFID software (if they have other RFID programs in use), and Milwaukee Cylinder provides a Memory Map document to identify how to interpret codes in the tag data.
Alternatively, a firm can utilize a Balluff handheld reader (model M-871-1-008-X-001-3002), for which Milwaukee Cylinder offers templates that can be downloaded onto it, so that the reader can automatically recognize the cylinder maker’s format.
When a tagged cylinder needs to be inspected or serviced, a worker would use a handheld reader to view its history, serial number and repair kit part number. To minimize maintenance shutdown timeframes, workers could visually inspect the cylinder and read its tag ID number days prior to the machine’s shutdown, and thus determine if a part requires replacement so that it can be ordered ahead of time. Without the RFID tag, repair parts could often not be ordered until after the machine was deactivated, since the ID number could not be accessed until the equipment was partially disassembled or the cylinder was removed.
After performing any maintenance tasks, an employee could use the reader to input data about the services provided, along with any comments. This information is then written to the tag’s memory, along with the date.
The data stored on the tag could also reveal historical trends, Lacina says. For instance, improperly mounting a cylinder could result in unnecessary strain being put on the equipment, leading to a shorter maintenance cycle and excessive wear on parts. Such a problem could be identified by reading the tag’s comment history. “The tag makes it difficult to lose information,” he adds, since its data can be captured and updated on the cylinder tag at any time, as opposed to an employee having to seek paperwork or input documents into a computer system.
The tag is highly durable, Lacina adds, and is expected to last for the cylinder’s lifetime. A customer wishing to retrofit one of his company’ existing cylinders with a tag can provide that cylinder’s serial number to Milwaukee Cylinder, which will then encode the relevant data to a tag and ship it to the customer for mounting on the cylinder.
“We’re the first company in this space that’s done something like this,” Lacina states. “We’re leading the industry.” When it comes to RFID-tagging cylinders, he says, customers will require some education to learn the system’s advantages. In November, he adds, the firm plans to hold a webinar, which will be available on Milwaukee Cylinder’s website, to help potential users understand how the solution works.